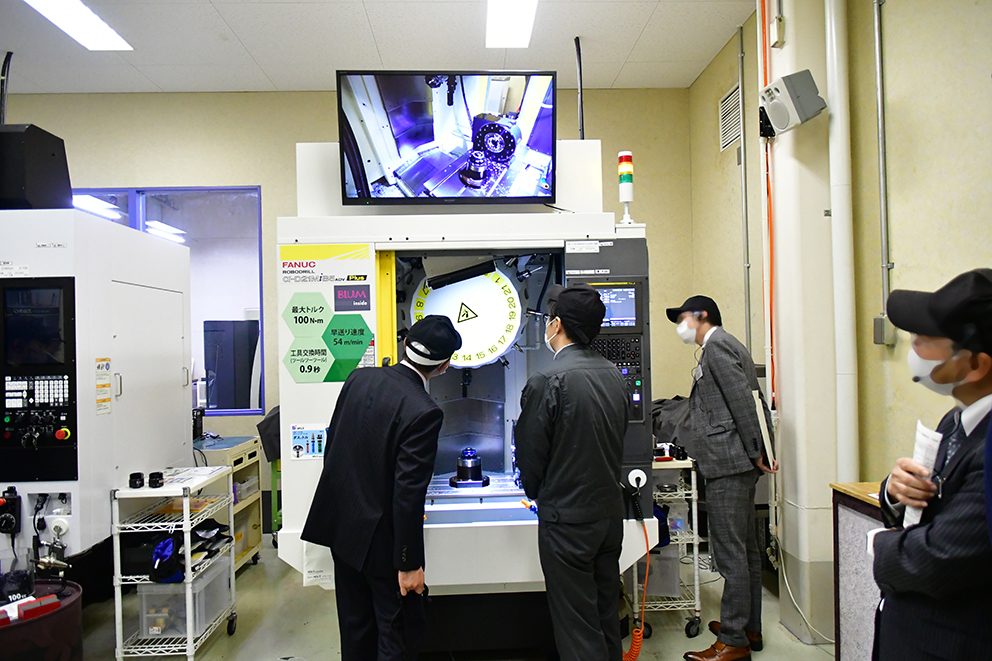
自動化、生産改善を提案
MSTコーポレーションは4月19日、中部地方のディーラー、ユーザーを対象とした工場見学会を実施。製造DXや自動化・省人化のヒントを探りに約40人が参加した。
同社は、日本のツールホルダメーカーでは創業86年と最も長い歴史がある。「すべてを見ていただこう」(弓場隆顧問)との方針で積極的に工場見学を実施しており、コロナ前は1500人に迫る見学者が訪れていた。感染の落ち着きで今年は1000人ほどに回復する見込みだ。
同社の主力商品の「焼ばめホルダスリムライン」はネックとベースを分けて生産しビーム溶接工法で接合する方式により4000種類ものバリエーションを可能にする。また大幅な自動化・省人化により「短納期」「コストダウン」を実現し、人間の作業によるばらつきを抑え品質向上にもつなげる。
同社工場の自動化の中心的ソリューションは素材、完成品、切屑パレットをAGVが自動運搬、回収するシステムにある。「よくある方法は、工作機械の横に素材などをストックして加工する。しかしロボットを活用し自動化してもストックが切れると止まってしまう場合もある」(担当者)。そこでパレットヤードにて一括でストックしAGVによる運搬と回収を行う。
「外部からの運び入れ、運び出し、工具の交換、機械の段取り替えなどはまだ人の手が残っているが、パレットヤードに素材を切らさなければラインは動き続ける」と話す。将来的にはAIを活用してさらに省人化を進めたい考えだ。
■焼ばめホルダの剛性を体感
焼ばめホルダスリムラインのデモンストレーションも行われた。たわみ量は工具の突出し長さの3乗に比例して大きくなる。担当者は「ワークを治具で掴み側面を加工したいときコレットチャック方式だとナット部分が治具に干渉するので工具を長く突き出す必要がある。焼ばめホルダスリムラインでは締付ける部品がないので先端を細くでき、工具の突出しを短くできる。その分、ビビリのない安定した加工を実現できる」と説明。コレットチャックで工具突出しが30?_の場合、表面粗さはRz=7・2ミクロンであるが、スリムラインを使用し同13?_と短くすると剛性が高くなり表面粗さは同2ミクロンに向上するという。
参加者は、実際に焼ばめホルダスリムラインとコレットチャックを使いデモ加工されたワークの表面をさわり比べ、違いを確かめていた。
他にもマシニングセンタを中心とした工作機械の予知保全の実演も行われ見学者の関心を集めた。主軸、モータ、移動軸、スライドなどは経年劣化するが、すべてを日々点検するのは難しい。そこで同社では最も酷使する主軸の振れ精度を自社テストバー「チェックメイト」を用い定期的に計測し、チェックしている。測定値が問題無く使用できる範囲を超えると劣化のサインであり、メーカー点検や部品交換などを実施する事で、突然の故障による長期間の機械停止や不良品防止に役立てている。
「『チェックメイト』は本体にマーキングされた長さ、直径、振れ精度、振れの位相の実測値を利用することで、正確な振れ精度と位相が分かります。Z軸の原点出しにも活用できますし、リーズナブルな価格で導入可能で高精度加工の実現に寄与します」(同社)。
(2023年5月25日号掲載)