産学が注視する「ロボット切削」
- 投稿日時
- 2025/04/16 09:00
- 更新日時
- 2025/04/16 09:00
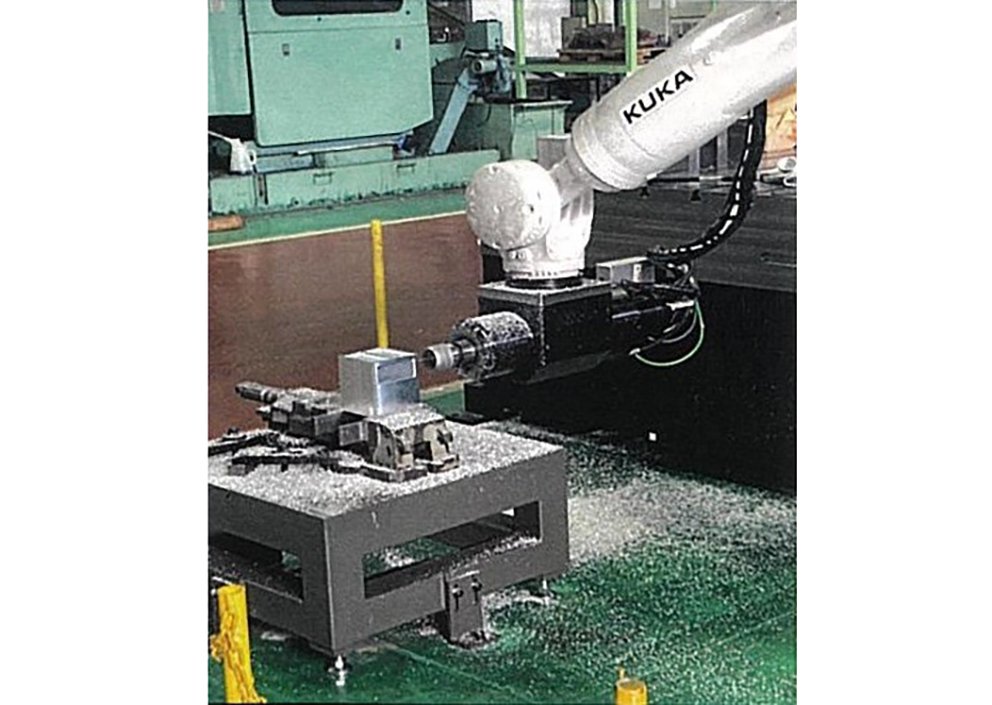
大物加工や建設現場で利点
多関節ロボットを使った切削加工が広がりつつある。切削に適した高剛性ロボットは欧州製(KUKA、ストーブリ、ABBなど)が主だったが、安川電機やファナックがたわみ補正機能をつけた剛性の高い製品を充実させていることがこの流れを勢いづけている。3月21日に東京・港区で開かれたセミナー「ロボットde金型 超大型金型時代の新加工技術」(型技術協会主催)でロボット切削を実施・研究する企業や大学が成果や課題を発表した。
ロボットSIerのトライエンジニアリング(愛知県名古屋市)は10年前からロボット切削に取り組み、これまでに46システムを納入した。岡丈晴専務取締役は納入事例として建機パイプ部品のチップソーによる切断、直径2㍍の船舶スクリューの鋳型づくり、アーク溶接による肉盛りで生じたビード(接合部の凸形状の盛り上がり)の後加工などを紹介。近年増えている仕事として「航空機のCFRP部品に直径1~2㍉の面直穴を6~8時間で6万個あけるものがあった。また、建設現場で大きな建材をその場で加工したいという相談を受けるようになった。工作機械は現場では使えない」と言う。工作機械にない強みとして長大ワークに対応(走行軸を使った17㍍材対応の設備を鋼材メーカーから受けたことも)、複数ロボットによる同時多軸加工(4台同時に使えないかという相談も)、6面加工やスピンドルを上向きにした高い切屑排出性、などを挙げた。
専用機メーカーの桜井製作所はロボット加工機「SAKU270」(KUKA製ロボットを使用、主軸HSK-63、ストローク1500×1000×500㍉)、「同270F」(ファナック製ロボット、BBT-30、1300×600×600㍉)を開発した。Gコードで制御し、加工精度は穴位置でそれぞれ±0.06~0.2㍉、±0.01~0.2㍉。工機部生産管理課の坂下昌史主査は加工例として溶接ビードを刃径30㍉・3枚刃のフライスカッターで除去する様子を動画で見せ、「今後、ターゲットとして車載用バッテリーケース(アルミ)やギガプレスの車体フレーム(アルミ)、ショベルカーのアッパーフレーム(鉄)などの加工を想定している」と言う。
■刃物で負荷・振動を抑制
ロボット切削による加工精度はいかほどか。広島大学先進理工系科学研究科の茨木創一教授の研究によると、1辺約150㍉の立方体(アルミ合金A5052)の5面について深さ4㍉のポケット加工を行ったところ(切り込み1㍉で荒加工後、0.2㍉で仕上げ)、最も精度がよかった天面でZ方向で±0.1㍉ほどの寸法誤差が生じ、面によるバラツキがみられた(KUKA製の500㌔可搬6軸ロボット、刃径10㍉ラジアスエンドミルは毎分9600回転)。重力やアーム姿勢の影響を受けるためだ。ただ、この誤差をキャンセルするように指令位置を調整することで加工精度は高められる。茨木氏は「本質的には、工作機械の空間誤差の補正の拡張と見なすことができる」とし、「オフラインプログラムが普及すれば、工作機械と同様に、ロボットにとっても空間精度は重要な性能と見なされるだろう」と話す。
イワタツールはロボット切削の課題を工具側から解決しようとする。同社は加工負荷および振動を低減するヘリカル加工用のエンドミルを開発した(近日発売予定)。中低角30度、ランピング角15~22度をもつこのヘリカルエンドミルは切れ刃長が一般的なエンドミルより短く、スラスト荷重は5分の1以下に抑えられる。岩田昌尚社長は「工作機械を使った際の剛性や振動への対応は機械側に問われたが、ロボット切削では刃物側にも求められる」と言う。ロボットの先端部分にもう1台の小型ロボットを取り付けたロボットonロボットの可能性も探る。小型ロボットにクーラントノズルを付ければ加工中のノズル位置を変更してその効果を高められる。聴講者からロボットonロボットの他の用途はないかと問われると、「CFRPなどの加工で切屑吸引ができ、エアーブローで切屑を吹き飛ばすこともできる」と答えた。
イワタツールが近日発売するヘリカルエンドミル
(日本物流新聞2025年4月10日号掲載)