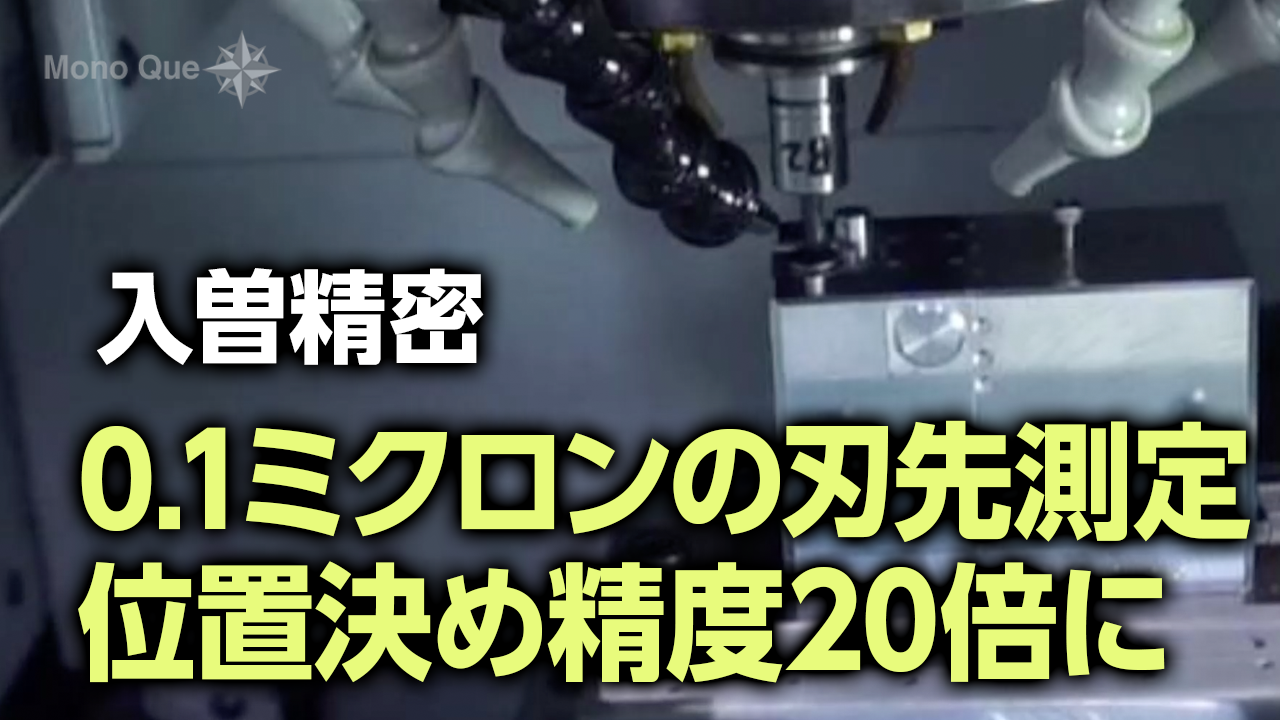
- ここに
注目! - 0.1ミクロンの刃先測定 位置決め精度20倍に
切削の高密度化へ、限界突破にかける情熱
斬新なアイデアと微細精密加工の技術で世界中から注目を集める「株式会社入曽精密」(埼玉県入間市)。この動画では、切削加工のテクノロジーマップを塗り替える同社の技術について、接触式工具長測定システム「HAGOROMO?nano」を中心に、斎藤清和社長に伺いました。
入曽精密は1990年代に3次元CAD/CAMとマシニングセンタによる造形システムを構築。アルミ削り出しのバラや、バサラ大将などの一品ものや図面のない部品を精密に複製することに成功しました。世界最小0.1?o角のサイコロを重心に偏りなく造形するなど、マイクロパーツの量産でも注目を集めています。
2020年1月に開催された「日進工具プライベートショー」では接触式工具長測定システム「HAGOROMO?nano」を初披露しました。
機上で用いる工具刃先測定機の精度は、従来は±2ミクロン程度が限界。機体振動も伝わるため、マシニングセンタでZ軸(上下方向)の位置を5ミクロン以下の精度で管理するのは、匠の離れ技が必要な特別領域です。薄く削っては手作業で工具を測り、測っては削るの繰返しで3?20時間以上かかることもあります。
一方、入曽精密の接触式工具長測定システム「HAGOROMO?nano」はプログラム操作で匠の技を必要とせず、瞬時に実用精度0.1ミクロン単位で刃先の位置を自動測定できます。外部から機体に与える振動の影響も当社の実測で0.05ミクロン以下であることも判明。Z軸の位置決め精度が従来の20倍に向上し、マシニングセンタによる自動加工の精度の限界点を塗り替えられるようになりました。
この技術を活かして、切削加工にどんな革新が生まれるのか。斎藤清和社長の斬新な発想と展望を、動画でぜひ、ご覧ください。