【座談会】新鋭マテハン企業トップが語る日本の物流の過去・現在・未来
- 投稿日時
- 2024/12/25 09:00
- 更新日時
- 2025/05/07 16:31
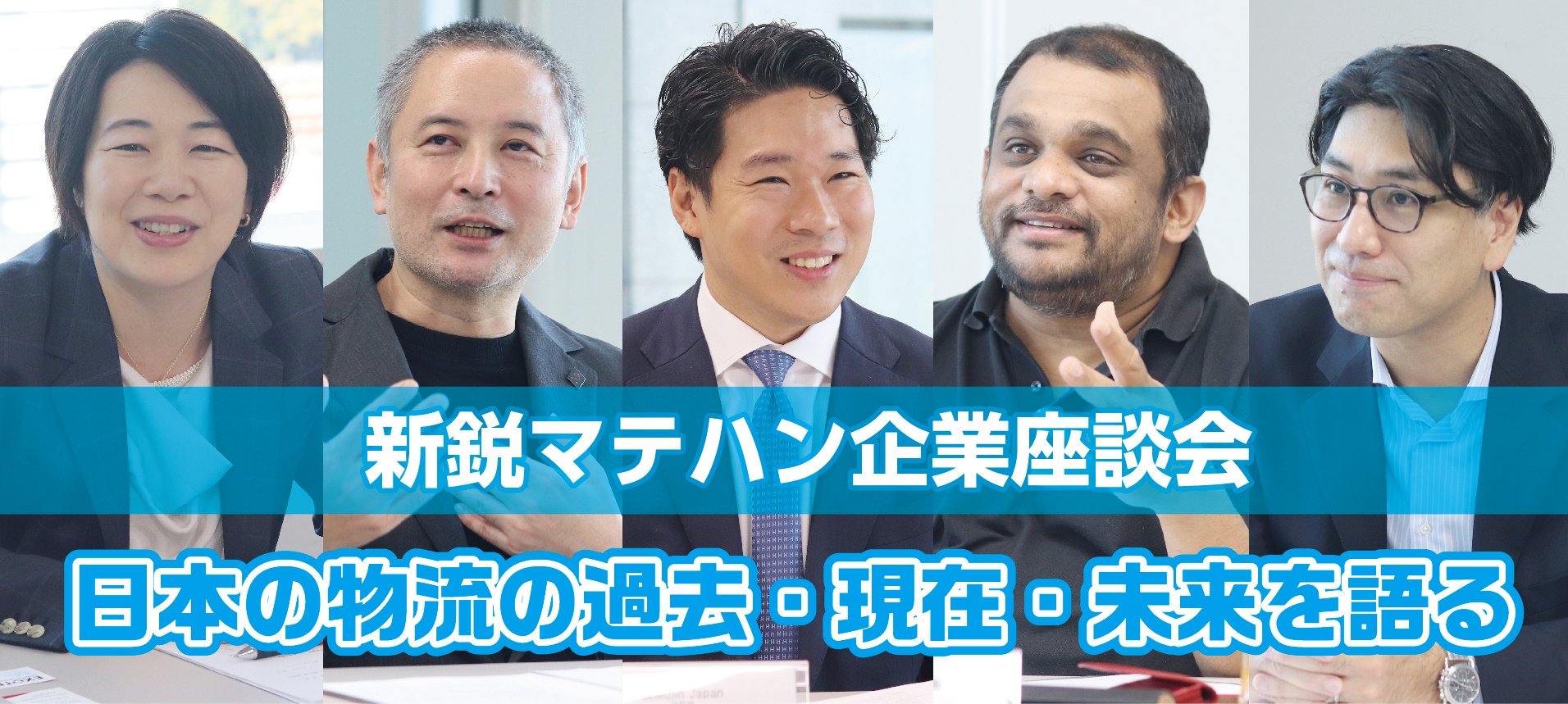
物流改革の最前線で戦う新鋭のマテハン企業4社(Exotec Nihon、AutoStore System、ラピュタロボティクス、Mujin Japan)の首脳とサプライチェーンマネジメントを専門とする河合亜矢子氏(学習院大学・経済学部経営学科教授)をモデレーターに迎え、変化が起こった2010年代から現在までを振り返るとともに、物流改革のあるべき方向性やもたらされる未来の可能性を探った。
PAST:Kivaで変わった物流現場
投資金額も10億→100億円超へ
河合亜矢子(学習院大学) 2000年頃にオンラインショッピングが日本に入って来て、10年ごろにはそれを利用するのが割と当たり前の雰囲気になってきました。それに伴い、物流現場もどんどんと変化していたと思います。今回お集まりいただいた方はそうした変化を目の当たりにしていた方も多いので、まずは現場が変わり始めた2010年代のお話をAmazon・小田原フルフィルメントセンターの立ち上げにも携わられた安高さんからお聞かせください。
安高真之(AutoStore System) 私はAmazonがKiva Systems(現アマゾンロボティクス)を日本に入れる12、13年頃、同社のプロジェクトマネージャーを務めていました。それ以前、Amazonの倉庫も棚から商品をピッキングしてソーテーションしてパッキングするというトラディショナルな形で運営されていて、ソーテーション以降の工程で一部自動機が導入されていましたが、「棚から物を取る」ところはずっと人頼りで課題となっていました。そこに、Kivaが登場しゲームチェンジを起こした。
河合 具体的にどう変わったのでしょうか。
安高 KivaをはじめとするGTP(Goods to Person)登場以前、一人当たりのピッキング量は毎時120~130行できれば御の字でしたが、GTPにより上限350~400行まで向上できるとわかり状況が変わりました。同時に、様々な会社がGTPにチャレンジし始め、自動倉庫をGTP的に使う取り組みも見られるようになりました。AutoStoreはそれ以前から電子機器商材の自社在庫管理システムとして活用されていましたが、GTPかつ高密度に在庫を保管できるという特徴は、小売りやECのみならず、在庫を抱えるすべての業態のニーズと合致します。このため、日本においても2010年代中盤からGTPの導入が進み、AutoStoreだけで見ても日本での導入実績はこの10年で実に70件を超えています。
河合 Exotecもそうした新しい波を捉えた企業の一つですね。立脇さんはいかがですか。
立脇竜(Exotec Nihon) Exotecが創業した15年は、まさしくKivaがAmazonに買収されたタイミング。GTPのソリューションがAmazonに独占されることを危惧して創業者の2人が倉庫自動化システム「Skypodシステム」を開発しました。創業から9年経ち従業員数は世界で1300人を超え、累計売上高も10億㌦を超え、フランス工業界初のユニコーンにもなりました。この成長を支えるのが、オムニチャネルなど現代の小売り形態に合致したシステムです。ECがどんなに拡大しても店舗で商品を買うニーズもあるわけで、それらをどう組み合わせていけるかが現代の小売りの課題です。当社のソリューションなら1つのシステムで対応できるため、欧米では新しいビジネスの核として、物流、Skypodに投資しようとする企業も多いです。
河合 ガジャンさんと荒瀬さんはいかがですか。
モーハナラージャー・ガジャン(ラピュタロボティクス) 私はその頃、スイス連邦工科大学チューリッヒ校の大学院生でした。物流との接点としては、私の先生がKivaの創業者で、Amazonに買収されたタイミングに在籍していたこともあり、様々な話を聞かされました(笑)。14年の博士号取得後に会社をスタートさせ、最初の4年はドローン開発などを行い、18年から物流分野に参入しました。コロナ禍の影響で、ECで商品を購入するニーズが加速したことも追い風となり、現在ピッキングアシストロボット「ラピュタPA-AMR」は同種のサービスの中で約7割のシェアを持っています。
荒瀬勇(Mujin Japan) 私も10年頃はまだ学生で、14年に住友重機械搬送システムに入社。そこで流通系の仕事や中国向けの電池関係の自動搬送や高機能フィルムの自動搬送などに携わっていました。入社当時の物流現場は、まだマテハンに対する投資金額がそこまで大きくなく10億円を超えると「ちょっと大きいな」、30億円を超えると「でかいな」とビビッているくらいでした。それが今では下手したら100億円、200億円を超える提案もある。それだけ物流に投資をしなければ現場が回らなくなってきていますし、人件費の高騰などで投資対効果が見合ってきた側面もあると思います。また、これまで日本のマテハンメーカー様が取り組んできたカスタマイズ品から、汎用的でコストを抑えた新しいマテハン機器が出てきたことで、中堅企業でも検討できるものが出てきたことも大きいですね。
処理性能躍進でビジネスにインパクトを与える存在に
河合 過去を振り返っていただきながら、少しずつ現在への接続点をお話いただいています。まず、荒瀬さん。コストを抑えた機器が出てくることで、なぜ投資金額が10倍近く跳ね上がったのでしょうか。
荒瀬 例えばユニクロさんの倉庫には、10年までは基本的にソーターくらいしかマテハン機器は入っていませんでした。パレットに段ボールを並べて人がピッキングを行っていたので、マテハン機器への投資は10億円くらい。しかし、GTPなど新たな製品の誕生によって処理能力が格段に向上し投資に見合う能力を発揮できる設備が出てきたことで、そうした機械を「どーん」と入れるとなると金額が100億円を超えてきます。
立脇 ユニクロさんなど100億円規模の投資をする企業は、人件費やスペース効率、処理能力などを複合的に見ながら導入によるビジネスインパクトを考えている。倉庫単体だけ見ていたら100億円という金額はなかなか出せないと思いますよ。
荒瀬 そうですね。例えば、人手でやると50店舗しか対応できなかった倉庫が、設備を導入することで100店舗に対応できるようになるなら、その瞬間に投資を検討する余地が生まれてくる。ヨーロッパ市場など伸びている市場では、どんどん倉庫の機能・能力を高めていかないと店舗の伸びに合わない状況です。そうやってマテハン機器に付加価値を見出していかないと人件費削減だけで考えたらROI(投資利益率)が低く、回収期間が10~12年とかで、「無理だな」となってしまう。
河合 100億円規模の投資に見合うだけのアウトプットが出ないとペイできないということですね。皆さん基準とされている期間などはありますか。
荒瀬 まちまちです。卸やメーカーさんの自社倉庫なら積極的な投資で費用回収期間が7、8年と長くてもいけます。ただ3PLさんで3年後の契約継続の可否がわからない、物量が安定せず将来的にそのビジネスを維持できるかわからないとなると、回収期間の目安が2、3年というケースもある。AMR(自律走行搬送ロボット)はハマりますが、自動倉庫はなかなかペイできないですね。
立脇 3PLもビジネスモデルをしっかり作って取り組んではいますが、最終的には「3年の壁」にぶち当たる。3年後に契約を切られたらどうしようということが頭を過り、設備導入の踏ん切りがつかない。そこは欧米の3PLの動きを見習うべきです。もちろん顧客なので荷主の方が強いですが、先進の自動化への投資を軸に他の3PLとの差別化を打ち出した上で、上手にパートナーシップを構築し、長期の契約を勝ち取る動きが必要だと思います。
安高 3PLの3年縛りは本当に厳しいですよね。というのも、日本で投資回収をしようと思うとどのソリューションを24時間365日回してもだいたい5年は超える。4年だとかなり優秀なイメージで、3年契約ではそもそも設備投資ができない。立脇さんの仰るように欧米では3PLでもAutoStoreを契約いただく事例が増えています。それは契約方法だけでなく、日本の3~4倍にもなる人件費の高騰によって、投資回収の目安が1~3年に圧縮されていることが大きな要因です。
ガジャン 確かに我々が進出しているアメリカでも人件費は倍以上ですし、2シフト、3シフトで稼働するのは当たり前。日本の倉庫は1シフトが普通なので、今アメリカに日本と同じロボットを持って行くと投資対効果は4倍くらい出る。元々我々がAMRを開発し始めた際も、皆さんが仰った「3年縛り」は強く意識しました。サブスクリプションで提供するモデルにしたのもそれが理由で、そのように提案しやすい商材に仕上げたこととコロナ禍で進展したECニーズの後押しもあって、投資と効果のバランスが取れてきたのかなと思います。
Present:付帯機器・AIの進化で完全自動化にも対応
マテハンが差別化・競争力の源泉に
河合 マテハンに大規模投資をする企業が出てきたとのお話もありました。技術的にも自動化できる領域はどんどん広がっていて、完全自動化を標榜する企業も出てきています。ロボティクスの現在地について教えてください。
荒瀬 これまでボトルネックとされていたアーム型ロボットによる搬送工程は、専用のハンドなどを作ることでほとんどすべての荷姿に対応ができるようになっています。しかし、地球温暖化対策として段ボールはどんどん薄くなっていますし、店舗での陳列作業を省力化するため段ボールにミシン目を入れ補充がしやすいもの、段ボールに意匠性の高い印刷を施したものなど、要求はこれからも変化していくものと見られています。当社としては、荷物を上からだけでなく横や下からも支えるハンドを開発したり、段ボールの認識技術を向上・調節するなどで対応しています。
立脇 荒瀬さんの言うように、現在ロボットで掴む技術というのはすごく、掴めないものはほとんどない。問題はピースだといろいろなものがそこに来るので、ハンドを持ち替える必要が出てくる。持ち替える時間も含めるとそこを自動化する意味が本当にあるかは考える必要がある。
荒瀬 当社ではツールチェンジに対応したシステムを用意していますが、仰る通り時間がかかる。さらに、バラピックのもう一つの課題として、きれいに積まないといけないということ。海外だとピッキングした製品を箱に落としている事例も多いのですが、落とすとダメな場合が多々あって、ピックだけでなくきれいに積むことも難易度が高い。それらはいずれも当社であれば対応できるけれども、そこまでやると人間のほうがはるかに早い。一方で、ダンボールのパレ/デパレタイジングなどそもそも人でやるのが大変な作業は、ロボットを導入してもペイすることが多い。なので、立脇さんの指摘の通り、活用条件に合わせて一番ロボットが効率よく処理できる商品やフローに当てはめていかないと、ファンタジーの世界で終わってしまう。
立脇 我々もまさしくその考え方で、人間によるピッキングがあることを前提にロボットピックを入れて、システム側で効率良く分配する仕組みを構築している。掴める掴めないもシステムが勝手に勉強していくので、ロボットピッキングは最初から入れておくことをお勧めしています。
河合 学習はAIを使ってやるのですね。
立脇 そうです。ピッキングだと製品形状などの基本的なデータを入れて、あとは3Dカメラで現場を撮像しながらトライ&エラーを繰り返す。カメラで掴めたか置けたかを判別して、それが10回やって8回しか成功しないのであれば、残りの2回の理由をシステム側が探るという感じ。最終的に掴めないと判断したものは人間の方に流れるので、倉庫全体の稼働は止まりません。
ガジャン AIの活用にはロボットのデータを取るのが一番の課題になるので、立脇さんの言うように早めから入れておくというのは大切だと思います。他の分野だとインターネット上にたくさんの教師データがあるので、そこからデータを取って来れば学習させられますが、ロボットに関するデータはインターネット上に落ちていない。AIに学習させられるだけのデータを取得することがロボティクス分野の一つ課題になっています。
河合 人が成功や失敗を判断しているのかと思っていましたが、学習もAIがやってしまうのですね。
立脇 そういうケースもある。アノテーションと言って、人が判断して定義を決めるパターンもありますが、そこも生成AIがだいぶ助けてくれるようになっています。
ガジャン そうですね。当社の自動フォークリフトを例にすると、パレットの認識に3Dモデルシミュレーションを使っていて、その環境の中でパレットがどう見えているのかをAIを使って自動で生成できるようにしています。そうすることで、そのデータを学習としても使える。ただ、気をつけないといけないのは、結局AIは確率の話なので、それだけでは現場で使えるものは作れないということ。なので、当社はAIの他に2つ別の方法を用意していて、それらがどちらもだめだった場合の3番目のレイヤーとしてAIを用意している。でも、必ず使う場所はあると思っています。
荒瀬 当社もダンボールとかの認識にAIを使い始めましたが、飲料系のダンボールはカラフルでAIが騙されやすい。なので、そうしたものは人が頑張ってアノテーションをかけてやるのですが、そうすると今まで処理できていたものが駄目になったりする(笑)。100回に1回失敗してもいいというお客様であったら使えますが、そういうところばかりではないので、それを理解したうえで使う場面を考えることは大切かもしれませんね。
安高 河合先生の最初の質問に戻ると、荒瀬さんが仰ったように、完全自動化というファンタジーなゴールを目指すよりも、何を自動化するかの方が重要だと考えています。AutoStoreとロボットアームを組み合わせた事例で96、7%自動化している現場があります。それは箱形状の商品が全体の96、7%占めているからで、どのくらい自動化率を高められるかはほぼSKUに依存してしまいます。このように究極のゴールを求めるよりも、実際にお困りごとを抱えている分野に注目し、そこを自動化していく方が大切だと思います。例えば、我々が今力を入れているのは冷凍分野。日本だけでなく世界でも冷食需要は非常に高まっています。しかし、冷凍環境を自動化するソリューションの選択肢は多くなく、未だに人がマイナス25℃とかの極寒の倉庫で作業をしています。こうした環境こそ本来自動化を進めていくべきところだと思っています。
マテハンを経営の核とする企業も
河合 マテハン機器の導入が進む中で、物流やマテハン機器に対する企業の見方も変わって来ているように思います。日本でも物流をビジネスの核にするような企業もでてきていますね。立脇さんいかがですか。
立脇 そうですね。そうした意識を持たれる企業が多くなっています。企業によって濃淡はありますが、積極的に議論や検討を進めている会社がだいぶ増えてきていて、欧米での導入事例を勉強したいという企業さんもおられます。しかし、まだまだ十分ではありません。入口と捉えています。
河合 海外の導入事例を見てビジネスを改革される例もありますか。
立脇 いろいろありますが、例えば、オンラインで買ったものを購入者が自分で取りに行く「クリック&コレクト」という仕組みは、日本ではあまり聞かないですよね。ただこれは日本でも絶対に取り入れられるビジネスだと思います。都市部はピックアップポイントが多いですし、郊外は郊外で仕事帰りに取りに行った方が再配達を依頼するよりも早く受け取れる。我々の導入先を見に行った日系企業のトップの方は「これは」という風に見て、国内に適用するにはどうしたらいいか検討いただいています。そういう新しい小売りの形態もこれから始まっていくのかなと。
河合 ガジャンさんはいかがですか。
ガジャン 最近、日本でも物流に関する責任者を付けましょうという動きがでてきていますよね。アメリカなどではSCM(サプライチェーン・マネジメント)が学問として確立されていて、その専門家が会社で適切なポジションについています。そのため、物流を深く経営と連携しながら考えられているのですが、そうした流れが日本でも本格化すると期待が持てそうですよね。
河合 CSO(チーフ・サプライチェーン・オフィサー)ではなくCLO(チーフ・ロジスティクス・オフィサー)に留まったのは残念でしたが。
ガジャン 残念ではありますが、そうした機運が高まっていくことはいいことだと思っています。
河合 今の日本の風潮の下では、CLOでは物を運ぶというところだけの話になりかねず、SCMの観点で全体最適を追求できるのか懸念が残ります。ガジャンさんの言う通り、アメリカやヨーロッパではCSOを設置して、部門間の横串を挿しましょうというのが当たり前だと思うんですが、日本だと別々。酷いところだと物流部は物流部、調達は調達部、生産計画は生産計画部、販売は販売部という感じになっているので、「どうしてこれでSCMができるのだろう」といつも不思議に思います。
安高 おそらくCSOとCLOの一番の違いは、コストセンターとプロフィットセンターの違いだと思うんですよ。この10年間、倉庫系の仕事をしてきましたが、物流をコストセンターとしか見ていない人が余りにも多いと感じています。コストセンター思考ではコストをいかに下げるかというバイアスしか働かない。プロフィットセンター思考になると、例えばAutoStoreの特徴はどこよりも保管密度が高いことで、「同じ商品回転数なら、同じ量の商品が倍入る=売上が倍になる」という考え方ができる。
河合 本来、物流・マテハンを管理会計的に見ないといけないですが、多くの関係者が財務会計から見ていてそれが問題ですよね。
Future:伴走型コンサルで物流・SCの未来を創る
Win―Winの関係で連携・連帯を
河合 先日、積極的に無人化を推進している工場を見学してきました。物流倉庫ではMujinのピッキングシステムなどを入れて完全無人化を達成していますが、よくよく話を聞くと、一日の受注量の関係でまだシステムの能力を100%使いきれていないと仰っていました。そういう意味では、皆さんが様々な最新の技術を使って倉庫の中を高効率に稼働できる様にしても、パフォーマンスを出し切ることができない可能性も考えられますね。そこはどう乗り越えていきますか。
荒瀬 Mujinは昨年からコンサルティング事業を始めています。当社が横串となって全ての工程の部署・部門それぞれでいくらかかっているかを把握する。そのうえで「この工程の負荷が高いから軽くする」など負荷やコストを調整し、「マテハンに大きな投資をしても、全体のコストを見ると全然減る」というのを知っていただく取り組みをしています。そうやって1つでも2つでもシステムを導入してみないと人も業界も発展しないので、「Mujinコンサルを通じて一緒に成長しましょう」と、企業と伴走する形で取り組んでいます。導入企業に「こういう風に要件定義を進めればよいのか」とか「ここに地雷があるのか」といったノウハウを蓄えていただきたいと思っています。実際に、ノウハウが溜まっている企業とそうではない企業では、当社の同じシステムを入れていてもなぜか処理能力が変わってきたりします。なので、コンサルをご提案するときは「我々が人を派遣してそれで完結するものではないですよ。残ったノウハウが差別化ポイントになるので、御社からも人を付けていただき一緒にやりましょう」とお伝えしている。逆にそこを企業側がわかっていないと、後々無駄にシステムに投資してしまったとか後悔することになるのだと思います。
ガジャン 我々は違って、ファーストステップとして既存のレイアウトやプロセスに一切手を入れず、とりあえずマテハンシステムを入れてもらうようにしています。本来、導入するマテハンシステムに合った形で入れる方が効率は出しやすいです。しかし、多くの現場が既存のプロセスを抱えていて、実作業を行うパートさんたちが一番力を持っている現場も多々あります。そうした人たちは自分のやり方に愛着を持っていて、今の生産性がすごいと思っていたり、それが強みだと思っている方もいます。そうすると、新参者の我々が「ちょっとこれだけ変えて…」と言っても「嫌です」と言われて終わりです。我々の基本スタンスは、現場改善をするにはデータで話をするしかないと考えているので、そこに辿り着けるようとりあえずシステムを入れてもらってデータが取れる環境をまずは作る。信頼関係ができてきた頃合いを見て、「荷物の配置をちょっと変えるだけで生産性をこう上げられますよ」ということをデータで説明する。手間はかかりますが変わっていきやすいです。新規倉庫だけでなく既存倉庫にも力を入れている我々としては、プロセスを全部直してから入るのはなかなか厳しいなと思っています。
立脇 おそらく2種類のアプローチがあって、一つはガジャンさんが仰られたボトムアップですよね。日本が得意とする、どんどん改善して現場のノウハウを溜めて最終的に経営層まで行ってというプロセス。それに対し、私達はどちらかと言えばMujinさんと同じで、トップダウンでコンサルティングして横串を挿して全体最適を図り、ビジネスをどう改善するのかをお客様に理解いただく。大体マニュアルでオペレーションしているところは人が倉庫内を時間や作業内容ごとに回遊する。最初はピッキングをやって、それが終わったら梱包をやって、仕分けして、一段落したら明日に向けた作業というように、人がバッチと一緒に動いていく。我々はそれを全部変えましょうと提案しています。加えて、倉庫内だけでなく入庫や出庫のところ、その先のお店や一般消費者に届けるところまで全部見て、どういうふうに全体のフローやビジネスを変えていこうかという結構アグレッシブな提案をするんですね。
河合 そこまで踏み込むと、なかなか導入までが難しそうですね。
立脇 その提案がそのまま通ることは稀です(笑)。各社いろいろな制約条件があるので、落とし所を見つけながら提案をしていく。それが導入前のコンサルティングのプロセスで、そうやってお客様とガッツリ話をすると成約以降もスムーズに立ち上がって、入れた後もお客様に喜んでもらえる。突き詰めていくと、重要なのはマテハン機器やフローを変えることによって、いかにお客様のビジネスにいい影響をもたらすかですから。そこを導入前からお客様が納得できる形までに落とし込むことを徹底しています。
安高 それは私からすると羨ましいです。AutoStoreが創業したノルウェーは、そもそも人口が500万人くらいしかいないので、自分たちで営業まで回り切るのが難しいとの割り切りのもと、パートナー100%モデルを構築してきました。結果的にそのモデルがあったので、私たちが直接お客様にコンサルティングしなくともパートナーがそれを実行してくれています。しかし、一つ言えるのは、我々のパートナーさんがそこを一生懸命やってくれたのが大きくて、例えば日本ではパートナーとして10周年になるオカムラさんなどがそうですが、お客様をガッツリ掴んでいただいているので成り立っています。なので、皆さんがおっしゃっていた通り、マテハン機器のパフォーマンスを上げていくには、正直お客様のビジネスに合わせてできる限り最適な提案を入れることしかできないのではないかと思っています。コンサルについても、欧州ではマテハン設備を入れるときにコンサルを入れることが多くて、日本でもそうした方々が活躍する場面が増えてきたことは私は健全だと思っています。
共通OS化で新たな需要が発生?
河合 皆さんが仰られていたように横串を通すためには、いかにデータを取得してそれを組み合わせるかが重要になっていくと思います。特に、マテハンを効率的に使うには、実運用時のデータ把握が重要だと思いますが、なかなかそこも上手くいっていないのではないでしょうか。
安高 そうですね。メーカーだからこそ取れるデータは結構あって、AutoStoreだとロボットがどれくらい遊んでいて、どのロボットのバッテリーが弱くなっているかとか、色々な情報を持っている。これはRCS(ロボット制御システム)の領域です。しかし、これとWMS(倉庫管理システム)やERP(基幹系情報システム)の間をつなぐ標準的なシステムは確かにありません。本来、WCS(倉庫制御システム)がそれにあたりますが、これが昔から課題で、「間の部分」に共通の土台が無いんですよね。
荒瀬 面白いのは、それぞれに対応したソフトウェアはあるのですが、それをつなぐことができないので、USBを持って動き回る現場さえある。
安高 下手をするとExcelのCSVをコピーして渡したりする。なので、横串がないどころか各部門共通で持つシステムが無いんですよね。昔はダイフクさんのMOSやPLCという基盤を使っていましたが、その上位概念のリッチなものがない。なので、Mujinさんがソフトウェアプラットフォーム「Mujinコントローラ」で様々な種類の機器を全部コントロールしようとしているのはすごくわかる。個人的には誰かがスタンダードを握って、なるべく標準化してほしいと思います。庫内物流のコスト構造を吸い上げられる土台となるシステムができ、上位のERPと組み合わさってくると部門間での話し合いがよりしやすくなると思います。しかし、そのプレーヤーがまだまだ少ない。
立脇 課題形成ができ始めたと思うんですよ。そのひとつの例として、我々みたいにパーツにもなるし、全体ソリューションにもなるというハイブリッドなシステムが出てきたので、それらを繋ぐのに現場は困っている。特にGTPとロボットピッキングを組み合わせるとそれを管理する仕組みが必要になるじゃないですか。その標準となる土台が未だなく各社各様でカスタマイズしている状況です。
ガジャン 技術的につながること自体は、ほとんどの製品がある程度スタンダードなインターネットプロトコルを使っているため、そんなに課題じゃないと思うんです。一番時間がかかりやらなければいけないのは、プロセスをどうモデル化・標準化していくかということ。つまり、倉庫に入ってきたパレットをバラで行くか、ケースで行くか、あるいはそのままで行くか、その後はどこで保管して、どのタイミングで出すのかといった物の流れを、いかにデータモデル化するかということです。それに加えて、在庫モデルを標準化してやっと、「このへんはこの設備を使えるね」とか、「この情報とこの情報をつながないといけないね」とか、「つなぐときにこういうスループットが必要だね」といった具体的な話ができるようになるんです。そこが抜け落ちて、いきなり導入する設備の話をするからうまく接続ができないですし、求めた効率が出ない。
立脇 プロセスのモジュール化ですよね。我々も色々なお客さんと話していくと、皆さん「ウチのハンドリングは特殊だから」と言う。実はモジュールに分けて同じ業界で見ていくと、そんなに特殊なことはやっていない。本来、効率的にできている企業と同じことができるはずなんです。なので、プロセスをしっかり見直してモジュール化・標準化していって、それらをソフトウェアでしっかりつないでいけば、どんな状況でも「この現場ならここのモジュールをこの機械に入れ替えよう」ということができる。Mujinさんがやられているのはこれに近いと思う。色々なところからハードウェアを買ってきて、ソフトウェアで作りこんでいく。様々なプロセスのモジュール化・標準化のデータがかなり蓄積できているんじゃないですか。
荒瀬 仰る通りで、プロセスを紐解いてどう数字に、ロジックに置き換えるかはかなり注力しています。例えば、倉庫の現場に行くと「こんくらい流れたなら、そろそろバッチ切ろうか」といったことを耳にします。我々からしたら「そろそろバッチ切るって何? 何でどういう判断なのか?」と疑問だらけです。それを在庫がこれくらい溜まってきて、終わり時間がこれくらいになったら切りますとか、プロセスをしっかりと分解して組み立てていかないと。人間が何かしらの判断を下すということは何らかのロジックがあるわけで、そのロジックをプロセスの中に数式として落とし込んでいく。そこはやはり大事なところですよね。
河合 例えばどのようなイメージでしょうか。
荒瀬 例えば、パレット自動倉庫から物を出しますという場合に、どこまでのレベルで制御しますかということ。このパレットが欲しいから出して下さいというような簡単なレベルが良いのか、このロケーションにあるパレットをどのロボット、スタッカークレーン、シャトルを使ってこの経路で出しなさいと制御するのか。これには大きな違いがあります。前者的なやり方ではおそらく予測も立たないですよね。何分後に出てくるのかわからないし、どれくらいコストになっているのか、稼働率に影響するのかがわからない。そうなってくると設備や情報を連携させてもあまり意味ない。
安高 難しいのが、我々もまさにそうですが、どんどん新しい発想の機器やシステムが生まれてきています。そうするとコントロールのやり方も変わってきて、常にパターンや型が増えるんですよね。例えば、ラピュタさんの新しいASRSは施工が割と簡単にできる。これはすごくいいことで、AutoStoreだとアルミGridを作るのに必ず建築の工程を入れる必要がある。ラピュタさんの物だと場所の移動や保管量の変更がおそらくやりやすいはず。一方で、そうしたフレキシビリティのある製品が入ってくると、今度は共通で持つシステムもそれに合ったものに変えないといけないはずです。新しいものが出るたびに加えたり変えたりしていたら、どこかで破綻すると思っています。なので、AutoStoreとラピュタさんのASRS、ExotecさんのSkypodのインターフェースを共通化して中間的なドライバーで制御できるとなると業界が一変する可能性はあります。
河合 WindowsOSのようなものですか。
安高 そうです。これはメーカーからしたらたまったもんじゃないですけど(笑)。お客様はどの製品を選んでもよくなるため選択肢が増えますし、スイッチングコストも低下します。また、インターネットがない時代にインターネットの有益性やそれで何ができるかは多くの人が想像できなかったはずですが、現在、インターネットという共通の土台があることで様々な新しい製品やサービスが生まれていますよね。まさに、こうした新しい何かが、インターフェースを共通化してそれらとお客様のデータを組み合わせることで生まれる可能性はあって、先に述べた限界のことも考えると連携の重要性は増していくと思います。
河合 一方で、色々なものが標準化されてしまうと、今度はコモディティ化して、レッドオーシャン化していくと思いますが、その辺りのリスクについてはどう考えていますか。
荒瀬 我々はまさにロボットの共通OSの構築に取り組んでいます。これは、安高さんが仰っていたようにメーカーにとってはたまったもんじゃない話です。しかし、Mujinにはロボットメーカー各社様がインターフェースを開放してくれている。それは、結局Win-Winの関係を作れるかどうかだと思っていて、共通OS化によって確かにハードウェアで差別化できる要素は減っていきます。しかし、OSが普及して皆がロボットにアクセスしやすい世界をつくることができたら、ロボットの販売台数は倍増どころではないと思います。当然、新たな活用方法や需要も出てくると思いますし、ロボット外観の好みなど新たな差別化要因が出てくるかもしれません。そうした世界観を共有しWin-Winの関係を築いて行こうとしているからこそ進められていることです。それはマテハン機器でも同じことだと思います。
他業種との連携が高効率化実現のカギ
河合 日本国内では市場が細分化されてしまっていて、一企業が扱う物量に限界があります。必然的にマテハン設備を投資するほどの物量を確保できないケースも出てくると思います。例えば、3PLが最新の自動倉庫や無人化装置を導入し、荷物を集約的に管理するという形も想像できますが、そうしたことは実現可能でしょうか。
安高 まさに、ソフトバンクロボティクスに在籍していた際にやったのが、荷主さんを集めてでっかい設備倉庫を作るモデル。同じようなコンセプトで佐川グローバルロジスティクスさんのXフロンティアやロジスティードさんなどがやられていますが、この方式は皆さんそれなりに苦戦しています。荷が決まっていない状態でマテハンを入れるのは本来一番やってはいけないこと。荷が決まっていてそれに適したマテハンを入れるから自動化が上手くいくのであって、1社だけだとパワーが足りない、物量が足りないという理由で複数を束ねればいいのでは、というデスクトップ的な考え方は上手くいかないと身をもって体験しました。
荒瀬 台湾の物流不動産デベロッパー・ALP社(Ally Logistics Property,Co.Ltd.)は、8万パレット分の自動倉庫を建物の真ん中に設置して、それプラスAGVも共有で使えるようにして、各フロアのテナントが従量課金制で使える新たなモデルで成功しています。日本でも野村不動さんとIHIさんもパレット自動倉庫を最初から組み込んだ倉庫を作っていますよね。
河合 安高さんと荒瀬さんの例は同じに聞こえますが何が違う。
立脇 不動産デベロッパーと組むというのがポイントではないでしょうか。彼らは不動産をパフォーマンスで見ているので、不動産賃料にプラスαできる差別化要因は大歓迎です。また、彼らはテナントさんが撤退したら次を入れればいいので、投資回収に10年、20年見てもいいわけじゃないですか。
荒瀬 彼らの資金は潤沢だから、建物で300億かかるのであれば、パレット自動倉庫が20億かかってもそんなに問題ない。また、立脇さんが仰るようにそれを武器にして賃料に設備利用料をプラスして貸し出せる。一方で、各テナントとしても単独では導入しにくい高効率なシステムが利用できて、メーカー側も費用はデベロッパーが先に払ってくれるのでキャッシュ的に嬉しいWin-Win-Winの関係を作りだすことができます。
河合 安高さんが指摘した荷が決まっていない状況は解決できますか。
荒瀬 パレット自動倉庫とAGVの搬送だけに絞っていることが肝です。この部分はどのテナントもあんまりオペレーションが変わらない。それより先のピッキングや梱包といったところにも自動機を入れて一手に引き受けようとすると、各テナントから段ボールのここにバーコードリーダーを貼って欲しいとか、感謝状を同梱して欲しいといった標準化と真逆を行く要求がたくさん出て来てしまう。最大公約数ではなく、最小公倍数でモノを考えて、共通ルールの濃いところだけ抽出したらあり得るのではないかと思っている。実際にALPは上手くいっていますし。
ガジャン デベロッパーと組むことで、防火区画とか初めから管轄省庁と交渉して免除してもらえば、より効率的に設備を入れられそうですね。現状、場所が先に決まってから設備を導入するので、どうしても空いたスペースや防火区画を避けて入れざるを得ない。そうした非効率な状況も打開できるといいですね。
安高 ALPの事例のように部分的な共用化という発想は、もしかすると日本でも上手くいくシステムかもしれませんね。また、今回の座談会を通してマテハンのプレーヤーだけで究極の効率化は難しいと改めて思いました。不動産や他のプレーヤーを巻き込んでやるのは、非常にいいキーファクターになると思う。まずは、国内で1社でもいいから大きな成功事例が出てくることに期待しています。
左からMujin Japan・荒瀬勇氏、AutoStore System・安高真之氏、学習院大学・河合亜矢子氏、Exotec Nihon・立脇竜氏、ラピュタロボティクス・モーハナラージャー・ガジャン氏
(日本物流新聞2024年12月25日号掲載)