オピニオン
慶應義塾大学 教授 青山 英樹
- 投稿日時
- 2022/10/24 13:29
- 更新日時
- 2024/08/19 13:21
IoT・ローカル5G・DXによるデジタルツイン高精度化に期待
工作機械やロボットを含むものづくり現場の様々な機器はIoT化が進み、機器や製造物の状況を認識するためのデジタル情報の収集が可能になってきている。IoT機器からの情報を簡便に収集する仕組みとして、ファナックが提供するFIELD、コンソーシアムが提供するEDGECROSS、そして各工作機械メーカが提供するシステムなどがある。IoT機器からの大量なデジタル情報を獲得できる状況になっている一方、その活用法・活用技術が十分に確立していないのが現状である。
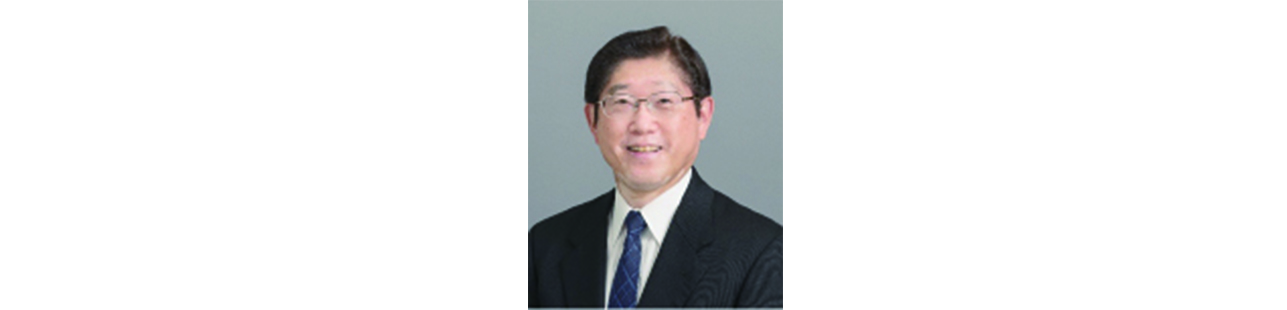
生産現場における各種IoT機器からの大量のデータを高速に処理するツールとしてAIが効果的であることは知られており、IoT機器からのデジタル情報をDXし、DX情報を基にものづくりを支援するAIシステムが開発されてきている。また、セキュリティレベルが高く高速にIoT機器からのデジタル情報を収集する手段としてローカル5G(4Gの20倍の通信速度)が注目され、その実用システムの開発も行われている。
生産機器のIoT化や5Gで、ダイナミックに大量の生産現場のデジタルデータを収集することにより、デジタルツインの高精度化が可能になると期待している。デジタルツインとは、デジタル空間(サイバー空間)にリアル空間(実空間)の現象・システムを構築したモデルである。デジタルツインで実空間の現象・状態を予測することにより、実空間で起こる不具合を事前に回避できるとともに、実空間のプロセスを最適化できる。
従来、デジタル空間でリアル空間の現象・プロセスを予測する様々なコンピュータシミュレーション技術が開発されており、大きな効果を上げている。コンピュータシミュレーション技術が実用になる以前は、自動車ボディーのプレス成形金型製作では、金型の試作を繰り返すことにより、目的とする形状を成形する金型を製作していた。金型を製作した後も、トライ(試し成形)で金型の修正が必要であり、トライで確定した金型も実機成形で修正が必要であった。この状況に対して、プレス成形のコンピュータシミュレーション技術の実用化により、金型の試作の繰り返し回数を激減し、大きなコスト低減・リードタイムの短縮を実現した。しかし、未だに、金型の試作・修正は必要であり、トライ機や実機での金型修正も必要である。ここで、ダイナミックに大量のプレスプロセスデータを収集し、コンピュータシミュレーションに反映してプレス成形の予測精度を向上するとともに、プレス機・金型のダイナミックな変形の状況を把握することにより、デジタルツインを高精度化し、シミュレーションの精度を向上することにより、金型の試作や修正を不要にできると期待している。
■高度な加工面を予測
切削加工における高精度なデジタルツインを構築する仕組みが開発されてきている。図は、工作機械制御装置(CNC)から情報を抽出し、デジタルツインに反映するファナックが開発してるシステムを示している。現在の切削加工シミュレーションでは、工具の送り速度は加工データ(NCデータ)で指示された速度を基にしている。しかし、工作機械は、経路が変わる時、各軸に加減速制御が適用され、工具の送り速度が大きく変化する。すなわち、工具の送り速度は、加工データで指示された速度とは異なっており、現在の切削加工シミュレーションでは高精度な結果が得られない。ここで、CNC情報を反映し実際の送り速度を反映した切削加工シミュレーションにより、高精度な加工面の予測が可能になる。ファナックでは工作機械の特性を組み込んだCNCのシミュレーションを開発しており、その情報を活用することよりサイバー空間の情報で高精度なデジタルツインを構築でき、実加工することなく不具合を事前に予測し回避するとともに最適化する対応が可能となる。
JIMTOF2022において、ローカル5GやDXを用いてデジタルツインを高精度に構築するシステム、そして高精度なデジタルツインを基に生産の高精度化・効率化・最適化を実現するシステム、生産の不具合を事前に回避するシステムについて注目して頂きたい。
(2022年10月25日号掲載)