オピニオン
製造業DX実現のカギ~第3回
- 投稿日時
- 2022/01/07 09:17
- 更新日時
- 2024/08/19 13:21
レガシー設備、技能継承にもデジタルを活用
前回は部品表や工程表、生産設備のデジタル化について述べたが、今回は生産設備のデジタル化に関して、補足説明をさせていただく。
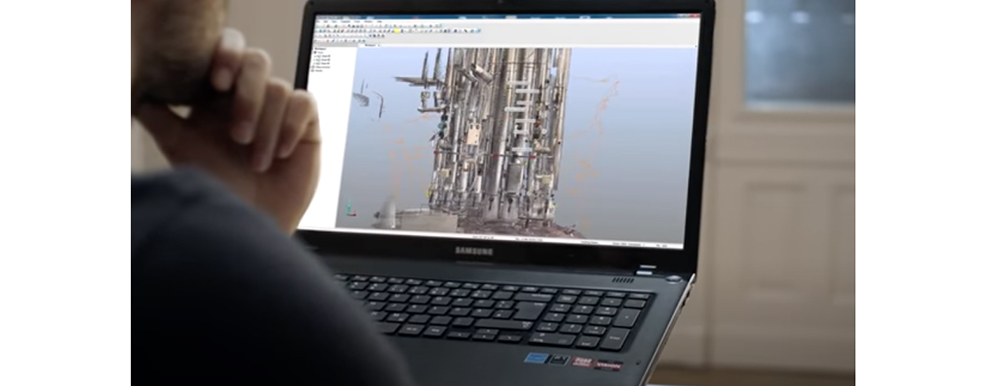
図面が無いような古い生産設備でも、今のテクノロジーがあれば、比較的簡単にデジタル化ができる。三次元スキャナを活用するのだ。実は三次元スキャナの活用は、私も2015年にドイツのBMW社に視察に伺った際に初めて目の当たりにし、その威力に驚愕したことを昨日のように覚えている。
その時は、ロールスロイスの製造工場全体を三次元モデルにしたものを見せていただいたのだが、搬送台車や仕掛品の在庫棚、天井の配管までリアルに再現されていた。「CGですか?」と質問したところ、「全て三次元スキャナで取りこんで作成したモデルを使って再現した動画です。元のデータは点群データとして寸法なども全て数値化されている、デジタルデータです」との回答をもらった。
つまり、大元の三次元CADデータが無くとも、立体的にデータを再現し、活用することが従来と比較にならないほど簡単にできるようになっているのだ。YouTube上でもそのデータを元にした動画が公開されているので、お時間のある方は是非ご確認いただきたい。
今では私が代表を務める会社でもこの三次元スキャナ(FARO社製)を導入し、活用をはじめている。「生産設備」のデジタルデータは、先に述べた物理的なデータだけではない。生産に関するあらゆるデータが製造業DXにおいては非常に大切になってくる。個々の設備の生産タクトはもちろん、各工程の部品搬送に必要な時間、製品ごとの段取り時間、設備メンテに必要な時間、不良率、手戻りに要する時間、故障率など、あらゆるデータのデジタル化が必要になってくる。
それらのデータを組み合わせることで、バーチャル空間上に仮想の生産ライン、工場を構築し、単なるデジタル上に構造物を再現して確認するだけではなく、「シミュレーションモデル」としての活用が可能となるのだ。目指す姿としては、リアルな工場全体がバーチャル空間上(PC上)に再現され、リアルな工場と連動する「デジタルツイン」を構築することである。
■課題の大半はデジタルで置換可能
これらのデジタル化の取り組みは、直近の課題解決にも役立つ。その一つが人々の働き方の変化への対応だ。特に国内では終身雇用が崩壊し、あらゆる業界で人材の流動性が高まっている。
さらに、労働人口の減少が人材不足に拍車をかけ、頼みの綱の海外人材の雇用も、諸外国との獲得競争にさらされ、思うような人材育成計画が進められていない企業が多い。
特にものづくりの現場においては、機械のオペレーションや部品の組み立て、検査といった「現場作業」から、生産計画の立案や最適な人員配置などといった「管理業務」まで、特定人材の熟練の技に頼りきってしまっている部分も多く、その人が退職してしまったら代替が効かないという話もよく聞く。そうなる前に早急にその技術をデジタル化し、複製できるようにしておくのだ。
例えば生産計画の立案などは、関係する要素のデジタル化というハードルをクリアさえすれば比較的自動化が可能だ。スケジューラやシミュレーションのソリューションは世の中に多数存在し、実際に活用している企業も増えている。現場の熟練作業についても、モーションキャプチャや、アイトラッキング(視線計測)の技術が発達してきており、従来はそれこそ背中を見て覚えるしかなかったことが、デジタル化できるようになってきている。
もちろん、私も全ての熟練技能が簡単にデジタル化できるとは思っていないが、課題になっている部分の大部分はデジタル化できると考えている。それができるだけでも不確実性への対応力は劇的に強化できるのではないだろうか。
(2022年1月10日号掲載)

チームクロスFA代表 天野 眞也
あまの しんや=1969年東京生まれ。法政大学卒。1992年キーエンス入社。2年目には全社内で営業トップの成績を残した「伝説のセールスマン」。2010年にキーエンス退社、起業。現在はFAプロダクツ、日本サポートシステム、ロボコム等の代表取締役、ロボットSIerによるコンソーシアム『Team Cross FA』ではプロデュース統括を担っている。趣味は車、バイク、ゴルフなど。