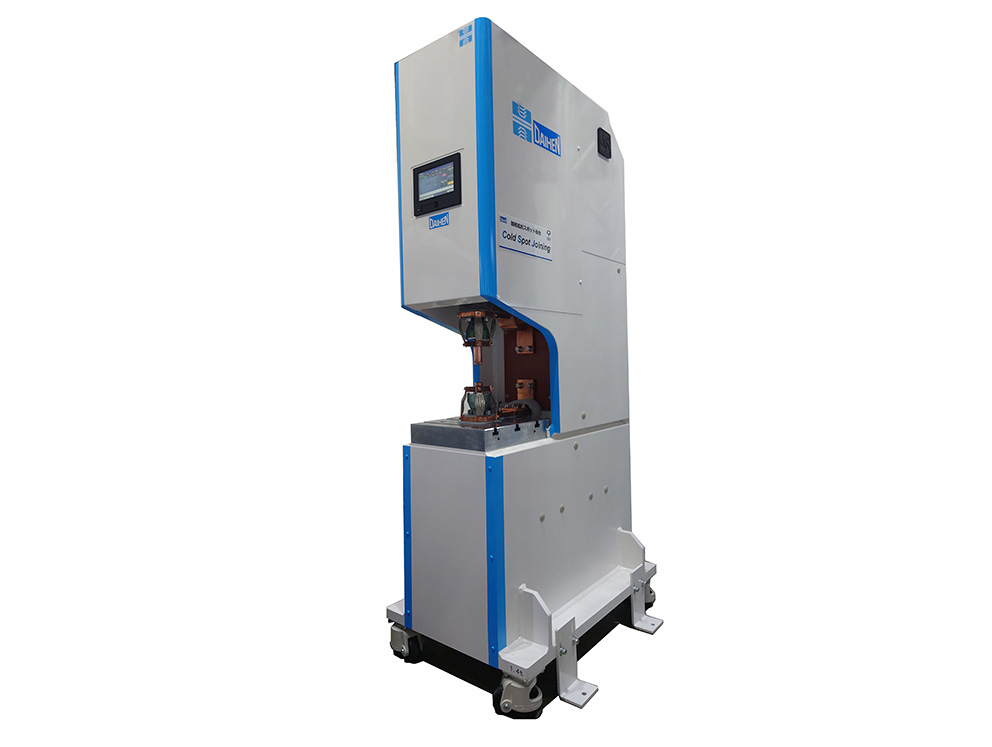
次世代溶接技術を新開発
ダイヘンは超ハイテン材やアルミ合金をはじめとする難接合素材の安定接合と従来比最大50%の省エネを両立する次世代接合システム「Cold Spot Joining」を開発した。
同システムは、大阪大学接合科学研究所の研究成果「固相抵抗スポット接合」をベースに、産学連携による協働研究を経て実用化したもの。
カーボンニュートラルの推進を背景にEV化が加速する一方、自動車をはじめとする輸送機器業界では、車体軽量化が課題となっており、軽量素材として超ハイテン材やアルミ合金等「難接合素材」の適用が進んでいる。
しかし、現在一般的な接合方法として使用されている抵抗スポット溶接法では、母材を高温で溶融するが故に発生する接合部の硬化や熱影響部の軟化等に起因する接合部分の強度低下や品質面の不安により、素材の特性を最大限に活かした軽量化(薄板化)を断念しているケースが多々ある。
こうした背景の中、同社は、溶接・接合技術で世界的トップ水準の研究を行う大阪大学接合科学研究所の研究成果である「固相抵抗スポット接合」に着目。産学連携による協働研究を経て、低温域で素材の特性を損なわずに安定した接合を実現する新接合システムの開発に成功した。
「強度のある超ハイテン材や軟質なアルミ合金まで幅広い素材の接合に対応可能。また溶融せず低温域接合するためスパッタ発生を抑制、後工程での除去作業が不要になる。また従来の抵抗スポット溶接に比べ最大50%消費電力を抑制し、CO2排出量削減にも貢献する」(同社)。
また接合機器以外は既存の抵抗スポット溶接の設備が流用可能で、置換えも容易に行える。
(2022年11月25日号掲載)