ヤマハ発動機・本社工場、6台のeve autoで建屋間搬送を無人化
- 投稿日時
- 2024/09/20 18:00
- 更新日時
- 2024/09/20 18:00
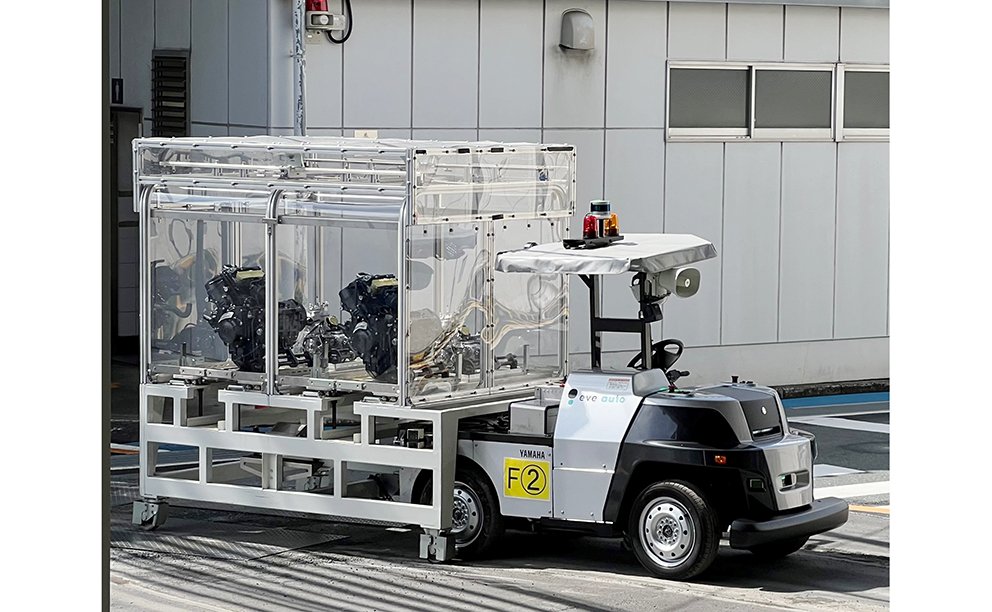
作業者12人分の削減効果
ヤマハ発動機の本社工場正門
年間約20万台の二輪車を製造するヤマハ発動機の本社工場(静岡県磐田市、従業員数約7000人、総敷地面積約53万平方㍍)では、2021~24年にかけて生産ラインの見直しが行われてきた。多様化するニーズに応えうる柔軟なラインを構築するため、これまで一連となっていたエンジン・車体組立ラインを二つの建屋(5号館:エンジン、7号館:車体)に分離。各建屋を繋ぐ自動搬送システムとして同社が出資するeve autonomyの屋外対応無人搬送システム「eve auto」を選んだ。工場改革の取り組みについて聞いた。
左から一ノ瀬正行課長と野口英樹主務
静岡県磐田市に位置するヤマハ発動機本社工場は、スーパースポーツに使用される「YZF―R1/R6」やモトクロス向けの「YZシリーズ」など、主に国内・欧米向けの付加価値の高いモーターサイクル製品を製造する。アセアンやインドなどの需要地での現地生産を進めてきた同社は、昨今の市況の変化に合わせて2021年から本社工場のエンジン・車体組立工程の見直しを進めてきた。
「近年、国内の生産台数がシュリンクする一方で、消費者ニーズは多様化しており生産するモデル数にはあまり変動がない状況が続いていた。多品種少量生産に対応できるライン構築を目指し再編に取り組んだ」(ヤマハ発動機・生産本部製造技術統括部組立技術部物流合理化グループ 野口英樹主務)
従来、5号館と7号館に4本あったエンジン・車体組立ラインをエンジン組立ライン2本(5号館)と車体組立ライン2本(7号館)に分離。規格化が進んでいるエンジンは生産効率を重視した形に、オプションやカラーリングなどが多様化している車体向けは多品種少量生産に柔軟に対応できる形を目指した。モデルごとに専用ラインを組む生産方式も見直し、同一ラインに全モデルを流せるようにした。
「従来方式では、モデルごとの季節変動によってラインごとに大きな作業負荷がかかってしまう時期がバラバラと発生していた。労働環境改善や工場の安定稼働のためにも大きな改革だった」(同社・生産本部製造統括部組立工場推進課 一ノ瀬正行課長)
■建屋間搬送を無人化
2種類の組立ラインに分離する上で問題となったのが、組立て済みエンジンの建屋間搬送だ。同工場では1日約900台もの完成エンジンが5号館から7号館へと搬送されるが、これを人でやろうとすると最大12人が搬送にかかりきりになる必要があった。
新たな生産ライン構築の横串となったのが屋外対応無人搬送システム「eve auto」。ヤマハ発動機のゴルフカートをベースとした車体と自動運転システムを開発するティアフォーの自動運転技術が組み合わさったAMRで、LiDARなど複数のセンサーを活用することで昼間だけでなく夜間や雨天時の屋外搬送の自動化に対応する。
「23年2月より3台で運用を始め、現在は最大6台体制で運用している。1周10分程度の周回コースを設定しているため、各車体は1時間あたり大体6往復している」(野口主務)
周回コースの詳細は次の通りだ。eve autoは、5号館にあるエンジン在庫を保管するための自動倉庫から供給されたエンジン4つを受け取り、連動するシートシャッターを自動開閉させて建屋を出る。幅約10㍍のトラック往来のある建屋間道路を横断。胸ほどの高さのトラックバースへの急坂を上り、バースに設けられた幅3㍍弱の狭路を25㍍ほど走行。再びシートシャッターを自動開閉して7号館に入ると、垂直搬送機に繋がるコンベヤに4つのエンジンを受け渡し、別のコンベヤからエンジン搭載用の空パレットを回収して5号館に戻る。
複数台のeve autoをピストン輸送に活用することで、建屋を跨ぐ形でエンジンと車体ラインを分離したにも関わらず、1連のラインのように運用することを可能にした。「eve autoの導入によって5号館から7号館へのエンジン供給をほぼ無人化できている。eve autoが安定稼働していることによって供給の指示も、7号館でエンジンが車体に組付けられると5号館の自動倉庫に次に使うべきエンジンの供給指示がいく簡便な形にすることができ、生産計画などの周辺工数の低減にも繋がった」(一ノ瀬課長)
エンジンをeve autoに供給する様子。コンベヤ側に位置補正機能を持たせ、ミスのない搬送を補助する
■海外工場での横展開も?
導入にあたって最も大きな懸念は「安全性」。積載する4つのエンジンはランダムで決まるため、大型エンジンが4つ集まると架台を含めた牽引重量は約1㌧(eve autoの可搬重量は1.5㌧)、車体重量と合わせると2㌧近くになる。
バースに設けられた狭路は単線運用になっており、eveauto同士の調停機能を活用して相互往来の自律運用を可能にする
「人も多く働いている当社の工場にeve autoを導入するとなると、人や通行するトラックと協働する場面が頻繁に発生することが予想された。実際、eve autoが走行している際にルート上で人がカゴ車を搬送する光景は日常的に見られる。そのため、物理的・心理的な安全性が最も大きな懸念であった。導入前にはeve autoの特性周知や走行ルートの明示などの対策を行ったが、eve autoの走行精度や安全性能を現場作業者が体感することで安心感が得られた」(野口主務)
導入から約1年半が経過した今、一ノ瀬課長は「ほぼ目標としてきた運用は達成している」と話し、工場間の連携を強化する同社では本取り組みの情報が既に全社に共有されているという。「海外工場からの問い合わせもきている。建屋間に高低差がある工場では、eve autoの走破性が特に生かせるのではないか」と横展開の可能性も示唆した。
■台風10号にも負けず
8月22日に発生した台風10号は静岡県に大きな影響をもたらした。
本社工場のある静岡県磐田市でも猛烈な雨を記録したが、eveautoは難なく稼働し続けた。
「瞬間雨量82㍉超を記録した昨年の豪雨では一時運行を停止したが、雨が少し落ち着けば問題なく再稼働でき生産への影響もなかった」(野口主務)
(2024年9月10日号掲載)