【座談会】利用広がる「ロボット切削」
- 投稿日時
- 2025/03/21 16:00
- 更新日時
- 2025/03/21 16:00
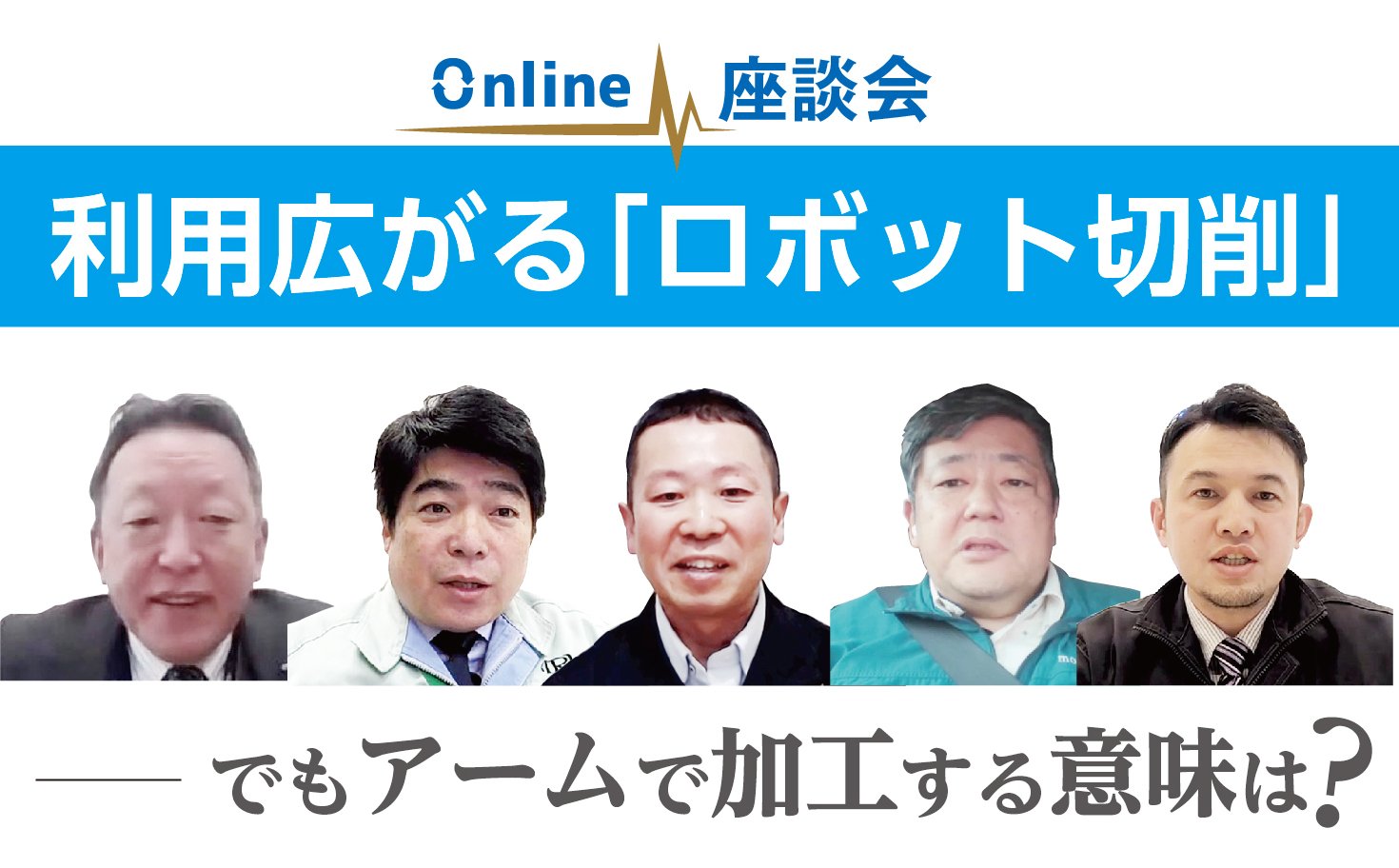
でもアームで加工する意味は?
ロボットアームを使った切削加工が広がりを見せている。加工負荷を検知するスピンドルユニットや切削抵抗を減らす刃物、保全管理を促す測定技術などの開発が進んでいることがこの流れを加速させそうだ。ただ、ふと疑問が浮かぶ。ATCを備え長時間自動運転できる工作機械もある意味、ロボットと捉えることができる。では切削加工をアームを使って行う意味はどこにあるのだろうか。メーカー、SIerに議論してもらった。
ロボットによる切削・FSW・研磨に注目
――ワークの大型化を背景に
――ご出席各社の事業内容や得意とする産業分野などを教えてください。
岡久学(安川電機)当社は創業110周年の会社で、基本的には電動機、モーターを中心に発展し、その応用としてロボットがあります。全電気式のロボットができてもうすぐ50年になります。アーク溶接から始まり、人ができない大きな可搬重量のものや細かな作業など様々な用途展開をしてきました。やはりモーターの会社ですので、モーターの特性を最大限に生かした産業用ロボットでビジネスをしており、その中の1つとしてロボット切削が広がりを見せています。フレキシビリティーがありますが、課題もいっぱいあると思っています。
――産業用ロボットでとりわけ強い分野は。
岡久 最初に製品化したのがアーク溶接ですからその分野は強いですが、アプリケーションとしては非常にたくさん広がっており、そこが強みと言えます。最近一番よく使われる用途としてはハンドリング。そのなかには組立て、ねじ締めなどもあります。
岡丈晴(トライエンジニアリング) 名古屋市にある当社は昨年、創業50周年を迎えました。ロボットSIerとして産業用ロボットを使った様々な生産設備を設計・製作させていただいています。元々は自動車のドアやボンネットの外周のカシメ加工をするロボットヘミングシステムという装置を長年手がけ、国内外の自動車メーカーさんにこれまでに410システム(1300製品)の納入実績があります。10年ほど前からはロボット加工システムやFSW(摩擦撹拌接合)も手がけています。現在、ヘミングシステムの売上高が全体の約5割で残りの5割が切削・FSW・研磨加工・その他専用機のシステムです。現在はとりわけロボットマシニングと呼ぶ切削の受注が件数も金額も増えており、この10年ほどで42件ほど納めました。国内ではすべての大手自動車メーカーさんとお取引させていただいており、近年では航空機関係や鉄道車両、建設機械メーカーさんなど大きなものを作るお客様との仕事が増えています。
倉谷泰成(KADO) 当社はCFRPを中心とするFRP(繊維強化プラスチック)素材を使いヨットやボートのビルダーとして創業し、今年で創業25周年を迎えます。20年ほど前に自動車メーカーさんの依頼でCFRPの成形工法開発をさせてもらったことがきっかけで、それからずっと成形プロセス開発請負業のようなことを続けています。この分野でもやはり自動化が必要で、特に自動車、航空機分野では高品質で安定した自動化が求められますので、ロボットを使ってみることにしました。これが今で言うSIerという仕事で、当社の主要事業になりました。インテグレーターさんはたくさんいらっしゃいますが、FRPを熟知したところは少ないようです。穴あけを含むミーリングやカーボン素材へのテープの貼り付け、近年はFSW、フィラメントワインディング(カーボンによる水素の高圧容器づくり)もロボットシステムで手がけるようになりました。最近は食品の一次加工も扱います。厚揚げなどの柔軟物はロボットが苦手とする対象物ですが、FRPを扱ってきたノウハウがありますので、そのハンドリングロボットも手がけています。手作業によるモノづくりをロボット化することを当社は得意としています。
岩田昌尚(イワタツール) 当社は今年96年目になるソリッドの切削工具メーカーです。ベルトサンダーなどを作っていた時代もありますが、今は刃物1本です。特殊用途向けの小径ドリルが主体で、たとえば金型など高硬度材の穴あけ向けのドリル、元々センタードリルのメーカーとしてスタートしていますので、位置決めや面取り工具なども扱います。ロボットマシニングについては、実は当社はトライエンジニアリングさんから歩いて行き来できる距離にあり、9年ほど前にトライエンジニアリングさんがロボットマシニングを実施していることをお聞きし、それから少しずつ一緒に取り組むようになりました。ロボット切削に取り組むと、切削時の挙動や剛性の問題がわかってきて、最近はこれに適した工具を開発するようになりました。そのメインテーマは低抵抗切削工具。要するになるべく工具側からも加工負荷をかけないようにすることです。事例としては車のボディーなど板金向けの加工システムがようやく実用化段階に入り、各種方面から引合いをいただいています。ただ正直言いますと、消耗品としてロボットマシニング用の工具がたくさん売れるという段階ではありません。ですが、知らないところでロボット切削用に当社製品が使われていることが最近わかってきました。切削工具はどこでどのように使われているのかを把握しきれませんので、詳しいことは言えませんが、少しずつ利用が広がっているようです。
切削抵抗を減らすイワタツールのヘリカルエンドミル
梁谷大(レニショー) 当社は1973年、ロールス・ロイスの航空機製造で課題となっていた品質改善のためにタッチトリガーを開発したことから端を発し、これまで生産革新に貢献するような計測技術の開発を続けてきました。1982年に設立した日本拠点ではCMM(3次元測定機)のプローブ測定システムを提案することからスタートしました。「Apply Innovation」をブランドメッセージでも謳っており、生産革新に貢献するべく様々な計測技術の開発を続けてきました。多くの製品群をもち、それらはすべて独自のフレームワーク「The Productive Process Pyramid」に基づいて開発されています。生産準備から加工後に至る工程を4つに分けて、それぞれの工程向け計測ソリューションを提案してきました。製品ラインナップとしては生産財および工程内の測定機のほか3Dプリンター、医療用製品まであります。
――加工対象物がどんどん小さくなり難削材が増すなか、モノづくりにおける測定の重要性が相対的に高まっているように感じます。
梁谷 日本の場合、ベテランの作業者の手の感覚に頼ってきた技能が伝承しにくくなってきています。これを我々の測定機で誰でも簡単に測定できるということが非常に重要になっています。また切削工具の長さを正確に測れないと加工点がずれてしまいますから、準備段階における各種設定項目の測定も重要です。
何がきっかけでロボット切削に?
――専用機の置き換え、自社生産の自動化
――皆さんはどうしてロボット切削に取り組むことにしたのでしょうか。ロボット切削の最大の利点についても教えてください。
岡 当社がロボット切削に取り組むきっかけとなったのは、トラックの足回りの部品を加工する鉄鋼メーカーさんから相談を受けたことです。お使いのフライス盤が老朽化し、更新するならロボットを組み込んでみたいと雑談のような話からスタートしました。私の知り合いに加工用の主軸メーカーさんがいたので、まずはアームに主軸を接続してみようと進めました。いきなり加工負荷の高いSS400材から取り組んだので全然うまくいかず、採用には至りませんでした。でもその経験からロボット切削に取り組むことになりました。小型で安価な工作機械は世の中にあるので、小さいワークをロボットで削るメリットは少ないと思います。やはり話として多いのは1㍍を超えるような比較的大きなものの加工ならロボットを導入する利点があります。自動車分野では昨今話題のギガキャスト、バッテリーケースの加工に取り組む部品メーカーさん向けにロボット加工システムを導入させていただくことが増えています。ここ最近多いのは航空機関係でアルミやCFRPの穴あけ、トリミングにロボットを使いたいという話。あと相談事で多いのは開先加工などを行う鉄鋼メーカーさん。今までグラインダーでゴリゴリやって3K職場的なところをロボットを使って改善したいとおっしゃいます。
トライエンジニアリングのロボット加工システム
――ロボット切削の受注件数はどれくらいですか。
岡 去年は4、5件。ロボットの数としては7、8台でした。が、2025年度は設備導入したいという話は倍増に近いペースで増えていく見込みです。当初は剛性がそこまで高くないので重切削は難しいだろうと30番の主軸を中心に展開してきましたが、重切削ニーズが増えてきて40番、50番の主軸をつけてステンレスをゴリゴリ削りたいという話も増えてきています。ニーズは大型のものにシフトしている印象です。
倉谷 当社がロボット切削を手がけたきっかけは、FRPの提供メーカーとして自分たちが手で行う加工を機械化してみようということでした。FRPを切削、切断すると粉塵がすごく出るので作業環境が悪くなりますから。ただし、ロボットアームは門形加工機に比べるとやはり剛性が弱い。刃物の選択や加工の手順などがポイントになると考え、自分たちが行ってきた手作業をいかにロボットにティーチングしていくかを含めて、条件出しをしました。当社に寄せられる案件は、ワークの種類とタクトタイム以外はお任せということが多く、ツールメーカーさんに協力いただいてかなり特殊な刃物、刃具、あとワークを固定する治工具を含めてパッケージ化してお客様に提供することが多くなっています。昨年はFRPのミーリングロボットを8台出荷しました。2年ほど前からギガキャストのアルミの切削向けの仕事が増えています。自動車メーカーさん、ティア1さんを含めトライアルに来られています。実際導入されるかどうかは加工精度やスピード次第で、今後この種の仕事が増えるのかどうか正直わかりません。大きなガントリー型の工作機械をお持ちのあるお客様が当社のロボットを購入いただいた際、その理由を聞くと、テーブルに載らないものでもロボットなら加工できるとおっしゃいました。一方、ギガキャストの仕事をされるお客様は、加工スピードが最悪落ちたとしてもヘッドが小さい分、複数台でアプローチできるので生産性を賄えると言っていました。ロボット切削に求められるのはスピンドルヘッドがコンパクトでワンサイドでアプローチでき、融通が利くところかと思います。これについてはFSWも同じで、当社が取り扱うKUKA製のFSWもヘッドが小さく、海外自動車メーカーさんはそれを3、4台導入し、同時に1つのワークを接合していると聞いています。
岡久 アーム式ですので剛性に不安がありますから、当社はロボット切削が工作機械に代わるとは思っていません。ロボット切削のメリットは簡単に加工できること、ワークの様々な角度からアプローチできることがあろうかと思います。その中でやはり剛性が1つのキーワードになってきます。どのように高剛性にするか。アームを太くして、関節に搭載された減速機のバネ定数を大きくすることで剛性は高くなりますが、そうなるとロボットの良さが消えてしまいます。ゴツいロボットで微細な穴あけをするのはちょっと違和感があります。ですから今の形のまま、反力・外力に対していかに強くしていくのか。剛性を高めるというよりも、反力に対してどうピッチを守って作業するのかをキーワードに開発をしています。モーターの後ろに付けたエンコーダー(位置決めセンサー)をベースに減速機を回してアームを動かすという構造が一般的ですが、減速機の先に、我々は二次側と呼んでいますが、エンコーダーを付けてアームの位置を制御するロボットもその対応として展開しています。おそらくは工作機械なみの精度はお客様は求めないと思いますが、そんな要望も出てくる可能性はあり、それを片持ち式のアームでどこまで満たせるのかは1つの課題ではあります。加工状態を把握して補正をかけながら、ワークがたわんでもまっすぐ加工できるようにすることも視野に入れながら開発をしているところです。
岩田 当社がつくる特殊工具には2つの意味があります。お客様の実際のワークや加工に合わせて工具を設計してつくることもありますが、それでは使用量によってはコストが高くなります。そのためかなり特殊な用途向けのものを規格化して販売することも多いです。ロボット切削に関してはトライエンジニアリングさんと一緒に開発するなかで、薄板板金用のドリルでの穴あけがブレークスルーになったので、その製品を規格化して販売することになりました。先ほどロボットの剛性についての話が出ました。切削工具側のアプローチとしては、反力を下げることに主に取り組んでいるのですが、もう1つ大きな要素として振動の問題があります。工具側で振動をどれだけ抑えられるかということも大きなテーマになってきています。具体的に言うと刃の数を増やした方がいいのですが、そうすると今度は抵抗が増えて反力が増すという相反関係がありますので、そのバランスをどうとるかといったことに取り組んでいます。ただし、都度ロボット切削用の工具をつくることは必要ではないと思います。当社に限らず、世の中で市販されている工具の中でロボットに適したものを選定するという作業も重要かと思います。
梁谷 当社は現状、ロボット切削向けの製品を持っているわけではありません。どちらかというとロボットを運用するにあたって提案できるようなソリューションを考えているという状況です。当社のメインのお客様である工作機械メーカー様、3次元測定機メーカー様とお話をすると、ここ最近は労働人口の減少に伴うなかで自動化に非常にフォーカスされていらっしゃいます。自動化するなかで当社製品がどこで使われるのかというと、ハンドリングしてワークを載せる際の位置のずれ測定し、位置補正をするという使い方であったりします。ではロボット切削に対して当社はどんなことができるのか。それをいま探っているところです。具体的にはアームの位置、ワークの位置、刃先の位置をどのようにして測定するのかがやはり大きな課題になります。ロボットの動きは従来、人がティーチングすることで設定してきました。このティーチングをいかに簡単にするのかは、我々測定機メーカーの技術を応用すればできるのではないかと考えています。またロボットそのものの動きの精度をいかに保証していくかということも1つの課題だと感じています。ロボットを正しく動かすにはその動きの精度を見ることも必要になってくるからです。我々が今考えているロボット切削の利点は自由度が非常に高いこと。加工領域が非常に広いこと。何といってもコストメリットがロボット切削の大きな利点ではないかと考えています。ただし工作機械からの転用となったときに、ロボットの操作は工作機械のGコードやMコードと違うので、作業者が容易に扱えるかどうかは疑問です。工作機械と同じように使ってもらうには、座標設定を誰でも簡単に行えるようにすることが必要です。基準となる座標がロボットの場合にはありませんから。座標設定は我々の技術応用で可能になり、生産革新に繋がっていくのではないかと考えます。
レニショーの独自ワークフレームThe Productive Process Pyramidに関連する多岐にわたる製品群
――ロボット切削を行うにあたってアーム位置(ツールの先端位置)の精度は保証できますか。
梁谷 非常に難しいのですが、タッチプローブをロボットにつけたロボットプロービングに取り組んでいるところです。その測定精度はロボットの剛性や姿勢、サイズそれから測定速度によって大きくばらつきます。このノウハウをこれから積み上げていく必要があります。
――トライエンジニアリングさんはロボットシステムを納入する際に精度保証を付加されているのですか。
岡 精度保証はできないというのが正直なところです。何を削るのか、どのような条件で削るのか、どのロボットを使うのかでかなり変わってきますから。それに代わる取組みとして事前のテスト加工をして満足していただいた上で仕様を取り決めて設備製作に取りかかるということが欠かせません。とはいえ当社の経験値はどんどん積み上がっていますので、お客様が求める加工精度に対して、「大丈夫ですよ」と言えるだけの知見はあります。
倉谷 当社もトライエンジニアリングさんと全く同じです。当社はKUKAオフィシャルのシステムパートナーですが、ドイツ本社にデータはないのかと問うと、繰り返しの位置決め精度はカタログに出せますが、軌跡精度は出しません。これは日本のロボットメーカーさんも同様だと思います。お客様には当社で試していただいた上で販売しているのが実情です。そういった意味でロボットメーカーさん、工具メーカーさん、測定機メーカーさんに協力していただかないとシステムとして提供することはできません。
KADOが提案するCFRPのロボット切削
岡久 皆さんおっしゃる通りだと思います。ロボットの繰り返し位置決め精度というのは、条件が非常に多岐にわたるので表現するのが難しい。軌跡精度もある軌跡に対してどれだけ振動成分があるのかも含まれますし、指定した位置の絶対値に対する精度も含まれます。空間上の相対的、絶対的な精度だったりといろんな見方があろうかと思います。ロボットの動きの方向性、姿勢によっても当然剛性は変わってきますので、これらを含めて一番弱いところで精度保証をするとたぶん使えないロボットになります(笑)。
――加工精度については切削工具が担う役割がおそらく大きいと思います。
岩田 正直言いますと、高精度な工作機械では工具の精度はすごく要求されますが、ロボット切削では工具の精度はあまり問われません。加工時の変位などの問題を刃物側で少しは軽減できる目処はたってきていますが、やはり難しいです。精度に関してもう1つ大きな問題として面粗さやバリ、ビビりがあります。精度はある程度許容してもらえると話しましたが、これらについては見過ごせないお客様がいらっしゃいます。面品位などを含めてロボット切削ではけっこう出てくる問題だと思いますし、工具側で改善しなければいけないと考えています。
岡 精度の話でちょっと追加ですが、ロボットは今までティーチングプレイバックでやっていたのに対して、やはり切削加工ではCAMでデータを作ってNC加工機で加工するように、バーチャル空間上で軌跡を作ってそれを実機に入れて加工するのが当然になるなか、空間精度を向上するものがロボットアームの個体誤差を吸収するためにも必要になってくるのではないかと思います。安川電機さんもロボットキャリブレーションというオプションが適用でき、当社でも精度が非常に向上しました。レニショーさんから話があったようにロボット単体が良くても、加工定盤とロボットの相対関係もあるので、測定機とうまく組み合わせていかねばならないと思います。製品1つに対して複数台のロボットで同時加工するシステムがギガキャストや大型製品に対して求められていますが、それを実現しようとすると複数台のロボットが1つのワークが置かれた座標系で同じように定義できないと機能しません。位置ずれやひねりなどを座標を組み合わせて補正する、それぞれの個体差を補正する、といったことをシステムが高度になることで工作機械に近いかたちで扱えるようになるのではないかと思います。
ロボット切削の課題と市場拡大の可能性
――必ずしも高剛性でなくてもいい?
――ちょっと先の未来も見据えながら、市場拡大の可能性について話していただけますか。
岡久 ロボットを使っていかに精度よく加工できるかどうか。そのアプローチの1つが高剛性ロボットであり、ツールや環境、位置の補正もあります。ロボットの進化は我々ロボットメーカーの責務です。一方で、加工精度を高めるために剛性が必要か。必ずしも高剛性でなくても要求を満たすアプローチが、データマネジメントのような形でできないかという着目点もあろうかと思います。いずれにせよロボット切削加工の課題というのは、いかにアーム式でメリットを最大化するかだと思います。ですから精度がよくならないと売れないという話では必ずしもありません。皆さんと協力しながらニーズを把握し必要な機能を開発していきたいと思います。
高剛性の安川電機製ロボットでアルミワークに穴あけテストする様子
岡 当社がロボット加工システムを導入させていただくなかで、ユーザーさんには大きく2つの見方があります。1つは従来、手で加工していた仕事は作業者の負担が大きいのでロボット加工にしたいというもの。このお客様は割と従来のロボット制御をそのまま使う形でかなり満足していただけると思います。もう1つは専用機やNC加工機で行っていた加工をロボットに替えたいというお客様で、ロボットもGコードやMコードで動かしたいというニーズが多くあります。それに対応するものが徐々に出てきて、安川電機さんにもGコードコンバーターがあり、当社も目下お試し中ですが、こういったものが出てくることで加工機からの置き換えニーズに応えられると思います。
倉谷 私たちインテグレーターができる範囲は限られていると感じています。まだまだ成熟していない分野ですから、今回お集りの各業界の皆さんに協力していただかないとお客様が満足するようなシステムはできないと思います。(動画を画面共有しながら)これはKUKA FSWのモニタリングシステムのパッケージです。加工条件のデータを横で見ながら、それをフィードバックし、速やかに条件を出せるものも存在します。複数台のロボットを1つのソフトで制御することもできます。海外ではロボット3台で1つのスピンドルを持たせて剛性を高めるというテストも行われています。このようなアプリケーションがこれからどんどん生み出されることになると思います。
岩田 従来、剛性を高めるのは機械メーカーさんの仕事でした。ところがロボットマシニングをやるようになるとそうとも言えなくなりました。対策を考えていると、今までと違う開発の発想も出てきて、結果的には先ほどお話した抵抗を抑えたり振動を発生しにくくしたりする工具につながってきました。ロボットマシニングの工具の需要は現時点ではまだ少ないのですが、実はそれが従来型の工具の開発にものすごくいい影響を与えることがあります。ロボットは剛性が低いという話がありましたが、実はロボットマシニングで加工する際、得てしてワークの剛性も低いことに気づきます。となると、実はワークの剛性が低いものは従来型のマシニングで加工してもワークが変形したり、たわんだりするので、実はあまり加工速度を上げられない。ですからある一定以上にロボット側の剛性が上がってくれば、あとはワーク剛性とのバランスを満たせばよいことになる。ギガキャストなどの加工がそうです。ちなみにロボットマシニングで使う工具は、小型のマシニングセンタなどで径の大きな工具を使うときに様々なメリットが出てきます。あとGコードでロボットを動かすという話がありましたが、3軸はともかく、5軸のGコードを手打ちできる人がどれだけいるのか。どうせCAMでやるなら何もGコードを介さずに5軸をCAMでダイレクトに動かせばよいのではと感じました。
梁谷 5軸をどう捉えるかによって話は変わるかと思います。いわゆる同時5軸加工で形状を削る場合、皆さんCAMで行うのでGコードは不要です。というか手打ちで作れる人はまずいません。逆に割り出し加工で決まった面に対して加工する場合にはGコードがあってもいいと思います。ケースバイケースになりますが、おそらくロボットマシニングを導入されるお客様の多くが元々工作機械を使っていた方になると思われますので、これまでの経験が生かせないので導入時に少し抵抗感が出るのではないかと思います。
岩田 先ほど岡さんが言われた5軸の難しさは、同時5軸だから難しいのか。割り出した上での3軸なら今のGコードで動くのでしょうか。
岡 そのあたりを検証しているところです。どこまで制限されるのかを含めて。そもそもCAMソフトを提供されるメーカーさんには、いわゆるロボット言語に変換して出力できるようなポストプロセッサーがあまりありません。特に日本国内ではCAMソフトをロボット言語に変換できるものは「OCTOPUZ」(オフラインロボットプログラミングソフト)くらいしかありません。今後ロボットの市場が広がり、様々なCAMソフトメーカーさんからロボット用のポストプロセッサー的なものが出てくると、それはそれで何か可能性が広がりそうです。
――ロボット切削の課題と市場拡大の可能性についてレニショーさんはいかがですか。
梁谷 周辺機器メーカーの立場から言うと、たとえば古い工作機械では精度が出せないのかといえば出せますよね。機能をソフトで補い、加工に合わせたソリューションをエンドユーザーさんが考えるからです。同じようにロボットをどうやってうまく使うか。それに対して我々は測定を用いたソリューションを提案していきたいと思っています。ISOで規格化されている精度が今、世の中でどこまで守られているのかというと、実はロボットメーカーさんは全項目を見ていないというお話があります。お客様がロボット切削のユニットを買ったときに、経年的に変化する精度をどうやって見ていくのかという課題があります。当社はロボットの出荷前後の精度に対して新しい測定を提案することで、お客様のロボットの保全のタイミングを管理でき、計画停止をすることで製品稼働ラインの安定化に繋がるような提案ができると考えています。もう1つは設定の部分。現状、SIerさんの話では、同じ作業を3人のオペレーターがやると、TCP(ロボットツールの中心点)がコンマ1くらい変わるという課題があります。我々のタッチプローブの技術応用によって誰がやっても簡単に自動で同じような精度で測ることが実現できれば、作業者レベルに依存しない安定稼働に貢献できると思います。私はロボット切削はものすごく将来性のある技術だと思っており、たとえばBT30番の機械が非常に普及していますが昔はそんなに削れないと言われていました。でもいろんな工具、ホルダ、加工技術の開発によって能力が高まりました。そう考えると、ロボット切削は私達を含めソリューションを提案していくことで非常に大きな可能性を秘めた生産財になるのではないかと思います。
岩田 話は変わりますが、ロボットマシニングでクーラントも実は大問題です。従来の工作機械でジャバジャバとクーラントをかけるのが当たり前でしたが、ロボットでそれはやってやれないことはありませんが実用的ではありません。もちろんドライでいけるものはドライでいいのですが、オイルミストによるよい結果がでてきており、外堀が埋まってきたと思っています。
倉谷 ロボットアームが動ける範囲すべてを削るとなると、やはり剛性の高い門形機には多分劣ると思います。部分部分の狭い範囲の加工、ギガキャストなどがそうだと思いますが、であればロボット切削はマシニングセンタに比べても遜色のないレベルまで来ているのかなという印象です。
岡 実際の加工は一部分であることが多く、その部分での穴加工ピッチや面角度を出すのはおそらく計測装置とうまく組み合わせれば実現できると思います。昨秋のJIMTOFでスギノマシンさんなどがスライド軸をもつユニットを出品されていました。すべてをロボットの動きで加工するのを目指すのはおそらく得策ではありません。当社もZ軸をまっすぐ動かすヘッドユニットを作ったりしています。ある部分は直動軸を先端ユニットに持たせて行うことで部分的な精度を向上させるようなアプリケーションは今後も充実してくると思います。
(日本物流新聞2025年3月25日号掲載)