【AM座談会】プロセス明確化を日本の競争力に
- 投稿日時
- 2025/03/11 15:04
- 更新日時
- 2025/03/11 17:45
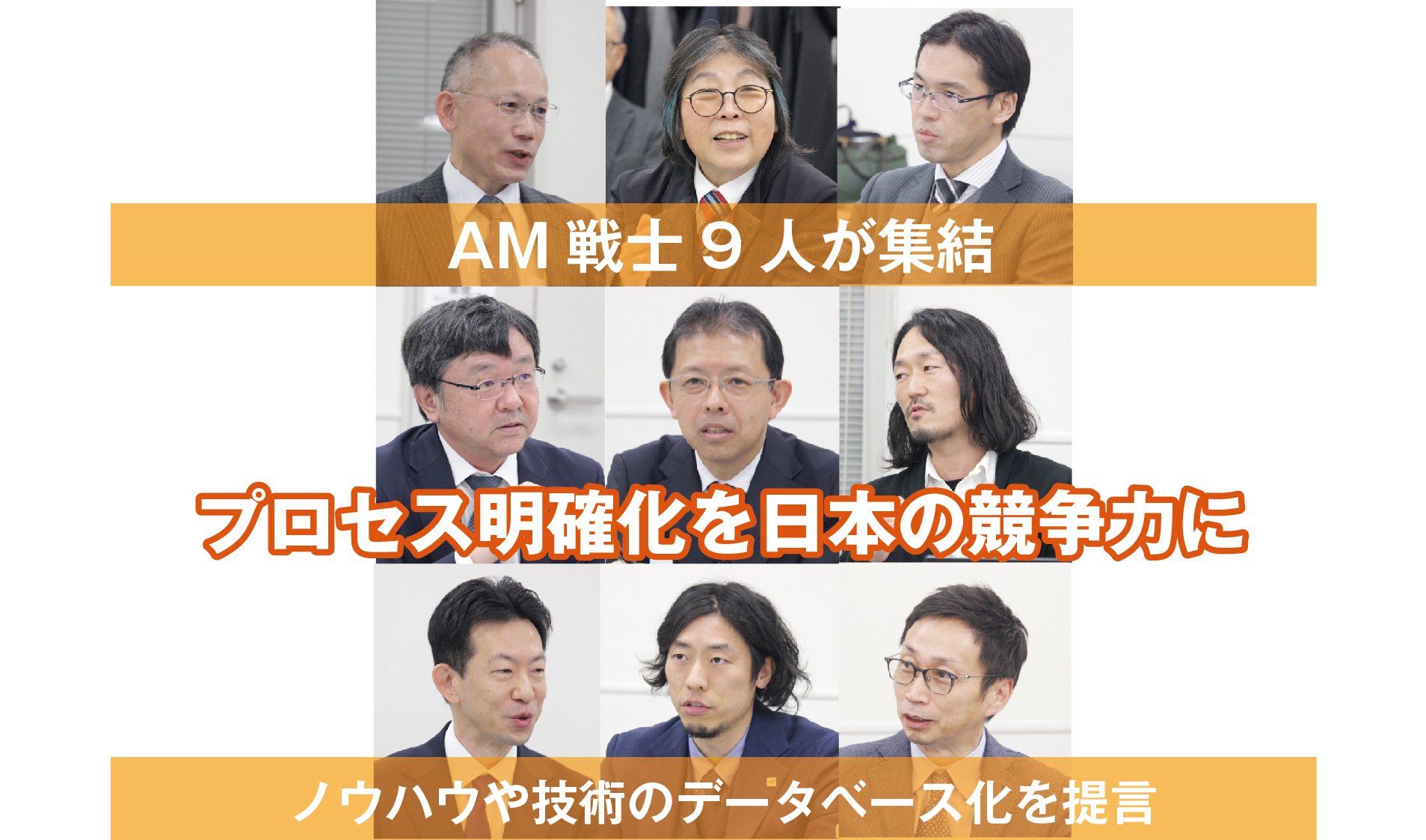
AM戦士9人が集結
周回遅れからごぼう抜きを
ノウハウや技術のデータベース化を提言
金属AM(金属積層造形、金属3Dプリンター)に取り組む人たちを、日本AM協会専務理事の澤越俊幸氏は「AM戦士」と呼ぶ。発展途上のAMは、まだまだ利益を生み出すには至っておらず、AM戦士の多くは社内のマイノリティーだ。「いつ利益を出すんだ!」「精度がでないじゃないか!」「耐久性は?」、社内外の圧力を受けながら、その研究や活用などに取り組む気概を「戦士」に準えた。だが2025年に潮目がかわるのではないか、との認識も広がる。
今座談会は、デンソーの寺亮之介氏の、「メーカーとユーザーが、AMのコストダウンと普及のロードマップが描けていない」という問題意識に端を発する。そこで新聞というプラットフォームを使い、ユーザーとメーカーがコミュニケーションを図ることで、何か現状打破のヒントを掴めないか。そのヒントをより具現化するため、特にメーカーからは、経営幹部の出席を呼び掛けた。
参加者は、経済産業省・星野昌志氏、マツダ・西昇一氏、豊田自動織機・佐藤良輔氏、デンソー・寺亮之介氏、ニデックマシンツール・二井谷春彦氏、松浦機械製作所・松浦悠人氏、三菱電機・木場亮吾氏、大同特殊鋼・大崎元嗣氏、ジェービーエムエンジニアリング・前田弥生氏のAM戦士9人に加え、オブザーバーに日本AM協会・澤越俊幸氏に同席頂いた。ビッグユーザーからは「現状の国内AM技術は、将来のためにデータベース化しオープンにして全体のレベルアップを図るべき」「原理原則の解明が競争力となり、大規模投資で先行する中国などに太刀打ちできる」と言った踏み込んだ発言も飛び出し、議論は白熱した。
(企画・司会 日本物流新聞社 服部泰平、撮影・運営 同社 岡田尚也、楠友郁子)
――マツダの西さん、口火を切って頂けますか。
西(マツダ・敬称略、以後同) AMの加工機を使用して製品を作る立場として、初歩でありながら普段なかなかお聞きできないことを聞きたい。例えば樹脂プリンターだと、出来はともかく、ボタンを押したら明日の朝にはそれなりのものが出来ています。「サポートはプリンターが勝手にやってくれるんだ、結構使えるよね」「少し形状を変えたいから次のやってみよう」、など2、3日のうちに形状もどんどん変わっていき「3Dプリンターっていいよね、使えそうだね」となります。ただ、当然強度はないから製品には使えない。ならば金属3Dプリンター(AM)で、となるわけですが「ボタン一つで出来るんだよね?」というと、材料の選定やレーザーの設定があって云云かんぬん。結局、メーカーと細かいやり取りを重ねていくしかない。粉体もワイヤーも、どういう原理原則があってモノが出来上がっているか、そこが明確になって初めて工程保証が出来ます。その理屈が分かっていないとなかなか制御できない。原理原則を設備メーカーはどのように考えていますか。
二井谷(ニデックマシンツール) まさにその原理原則が造形プロセスのスタビリティー(安定性)や造形物の品質保証に関わる部分です。当社はプロセスの制御が可能なスピードで造形を行うパウダーDED方式を選びました。TRAFAM(技術研究組合次世代3D積層造形技術総合開発機構)での活動に関わる中で、この温度だとこういう組織になる、といった技術開発や研究を行い、プロセスの原理原則(安定化のロジック)を確認しながら開発を進めてきましたが、西さんが指摘するように、原理原則が完全に解明されたわけではないです。DEDの特徴は異種材料の結合(バイメタル、マルチマテリアル)ですが、界面で発生する金属間化合物の生成や収縮量の違いによる亀裂の発生などまでは完全に予測、コントロールしきれていません。ただ、AIや機械学習の技術も上がっており、3Dモデルで予測制御していくアプローチと、加工データの蓄積によるリアルなアプローチをうまく活用しながら原理原則の確立を目指しています。海外では、難しい技術だからこそ、解決時の利益を求め莫大な投資が集まる。それに対抗するには日本企業の垣根を超えた取り組みも必要になってくるのではないでしょうか。
松浦(松浦機械製作所) 当社のPBF方式で言えば、いついかなる形状においても同じ溶融池 (メルトプール)をどうつくるかという技術開発が重要となります。そこで温度とメルトプールの法則の研究を進めています。逆に質問ですがAMが目指す「ボタンを押したらモノが出来る」という世界が実現すると、ユーザー側としてはどう差別化をしていきますか。
西 使うユーザーの幅は広く、製品設計に使いたいユーザーや現場の最先端でモノを作ってロケーションをやっているメンバーもいますし、もっと簡単なものに活用したいユーザーもいます。モノづくりの根底を変えようと思うと、どの難易度のユーザーも当たり前に使えるツールにしていくのが原理だと思います。「ボタン一つで」は現場の発想ですが、現場がいいと思わないと進んでいきません。ごく一部の難しい部品がAMで出来ても、それこそどの完成車メーカーでも同じようなことは出来るよね、という話になってしまうのでは。二井谷社長がおっしゃったように、今すぐに出来なくてもいいんです。材料の特性とエネルギーの加え方で急冷凝固は制御されますので機械と材料はセットです。そのデータベースをメーカー、ユーザー、ライバルの垣根を越えて共有化出来ないかと考えています。
ビッグデータのクラウド化で世界を席巻⁉︎
松浦 データベースを作っておけば、新たに挑戦されたい方も、競争のスタート位置に最初から立てますね。そこからの差別化の競争が出来れば、ますます普及は進んでいくということになりますね。
寺(デンソー) まだ製品は出来ていないが、それを目指す立場です。車の部品は(車が寿命を迎えるまで)壊れないように寿命設計し保証しないといけないわけです。設計するときに、何を制御すればその機能と耐久性を担保できるか、徹底的に勉強しないといけない。それは我々だけで出来ることと出来ないことがあり、金属物性になぜこの機能が出ているかは、材料や機械を熟知している設備や素材のメーカーと協力していかないと解明できない。ここが競争力となります。中国などがAMに莫大な投資をして先行しているように見えますが、西さんが言われた原理原則の部分の解明はまだ出来ておらず、おそらくあらゆる技術がまんべんなく進んだ日本にしかできないものです。日本のあらゆる技術を寄せ集め、爆縮を起こせる分野こそAMなのです。
――設備メーカーのご意見が続いているので素材メーカーの立場から一言いただけますか。
大崎(大同特殊鋼) 装置メーカーは、セールス的な必要性もあり形を作ることが優先になっているように感じます。PBF方式で言うとメルトプールの管理など、形状が崩れないということを設計思想の第一にしています。鋳造の世界に似て、溶かして固める過程での冷却や凝固速度が造形物の特性に影響を与えます。形を作ることで最適条件にする部分と、ユーザーが求める品質保証の部分がラップする領域を突き詰めないとAMが量産部品に適用される世界は来ないと思います。我々は鋼材部門で、ユーザーの仕様にマッチさせるために熱処理と冷却過程による最適組織の生成のノウハウがあります。そのノウハウを活用し装置メーカーとユーザーの要求特性をマッチさせる部分を探っていく動きが必要になってきます。現在は、この素材にこの条件、という一対一になっていますが、もう少し幅を持たせて形状を担保出来る、品質も担保できるパラメーターの閾値の設定が必要になってくるのではないでしょうか。
木場(三菱電機) 現在AMは、経験値をベースに、形を作ることが優先。造形物の特性については検査してみないとわからないという状況になっています。加工の再現性はあるので、一度試作を作って検査して大丈夫であれば、同じ条件、同じパラメーターの加工で品質は一定程度保証されるところまでは来ていますが、少し形を変えればまた同じことをしないといけません。造形プロセスをモニタリングしても、例えば5層目を加工した熱が4層目や3層目にどう影響するかなどは現在の計算速度では解析が困難で、近い将来の実現も見えてきません。造形が完成するまで、どういう結晶構造の造形物になっているのかは今のところわからない状況です。加工前に熱シミュレーターを用い、この熱履歴で加工すると、結晶がどう形成されるかを予測して、条件を定められるようになれば「ボタン一つで」という世界に近づいていくと思います。我々も取り組んでいますが、今は一つのシミュレーションをするのに数時間かかるという状況であります。ベンチャーなどとも協業し加工前に完成形状や特性を推測できるように研究を進めています。こういったシミュレーション技術の向上の為には、たくさんのノウハウ・知見があったほうがいいとは思います。議論にあるようにデーターベース化して知見を集めるというところも、社内で検討したいと思います。
――ジェービーエムエンジニアリングさんが大きくかかわる部分では。
前田(ジェービーエムエンジニアリング) いいふりをありがとうございます。私は普及ではなく社会実装したいと考えており、中小零細企業に使っていただこうと思えば、スーパーコンピューターをもってこないといけないようでは話になりません。ならどうするかと言えば、ビッグデータを吸い上げるんです。もちろん前出の議論にあった解析というアプローチも含めての二本立てで。先行して取り組んでいるユーザーが何に困っているかと言えば、作ってみないとわからないということ。極論すれば、松竹梅ぐらいの大まかな設定値で作れるということを我々メーカーサイドで提供できれば、あとはユーザーの事情に合わせてどんどん使っていけます。私はパウダー関係に力を入れていますが、中小企業のユーザーでも製品を設計して、「この製品はこのパウダーの配合でこう作る」まで特許を取れるチャンスが生まれますよね。配合も含めて変化していく中で、デジタル技術を使った分析では対応はできません。製造業にチャンスを生むことが重要であり、ある程度の閾値を決めるのはビッグデータになるので、夢物語かもしれませんが経産省なり政府なりが主導して、クラウド上にビッグデータを上げて、それが等しく製造業で使えるようになれば、メイドインジャパンが再び世界を席巻できますよ。
――星野さん、いかがですか?
星野(経済産業省) 前田さん、とても参考になるご意見ですね。AMのオールスターの皆様によるホームランが飛び交っていますね。ここまで皆様の技術のお話をお聞かせいただきました。優れた技術を日本のチームで協力、切磋琢磨して追求していく必要があります。また『ワンボタン化』というお話が出ましたが、システムが確立され誰でもボタン一つで製造できるようになる点については、メリット・デメリット両方の視点で見ていく必要もあると思います。AMはモノづくりの発想を変えてゲームチェンジできる技術です。プロセスの明確化、データベース化などの活用のお話もありましたが、そのうえでどうノウハウを蓄積していくか。協調領域としてみんなでやる部分、競争領域として切磋琢磨できる部分、ここをうまく分けて進めていくと日本の競争力を上げることに繋がると思いますね。
――品質保証の難しさ製品適用の難しさの議論が続きましたが、直接製品に使用しない治工具・金型では活用が進んでいますよね。ダイカスト領域ではいかがですか?
佐藤(豊田自動織機) ワンボタンという意味では金型で使う分には、皆さんの言うボタン一つに近い状態です。今まで1000個以上作って造形でトラブルが起きたことは一度もないんです。ただ現在の材料が外為法のリスト規制の対象で輸出が難しく、また人間の体への影響も懸念されるので現場の管理が厳しい。それを変えていきたいので新しい材料に10種類ほど挑戦しており、造形機も既存のもの以外も試している。そうなると材料粉末、造形機の組み合わせごとに、機械特性、熱特性等を評価、と決まったプロセスを毎回、当社で踏まなくてはいけない。これがとてもめんどくさい(笑)。当社はデーターを提供するのはやぶさかではないので、そこは協調領域としてみんなでやれないかなと。また材料、設備メーカー各社が提供してくれる機械特性、例えば衝撃値で微妙にUとVの値が違ったりして横並びで比較しづらいので、ユーザーとしては統一出来るところは統一してほしい。材料、機械を評価するのに毎回数カ月かかってしまうのは大きな負担となります。
――メーカー側からユーザーサイドにご意見や質問はありますか。
木場(三菱電機) どうすれば買ってくれるんだ(笑) というのを教えていただけると一番ありがたいですが……!大きな視点でみてAMへの投資が現状なかなか進まない原因はなんでしょうか。
佐藤 自分は投資について社内承認を得るのにあまり苦労を感じませんが、他社さんからAM装置導入のシナリオ相談などを何社かから受けることがあり、その中で去年3社ぐらいAMを入れられてますよ(笑)。AM導入のネックになっているという意味では、どの会社もはっきりと儲かると分からないことに投資をしない風潮になっていっている感じがします。やってみないと分からないことが面白いし、分かり切ってることは他社もやってますからね。お金をかける以上、投資効果は問われるので、手堅い領域でこれだけ効果があり、ワクワク領域というか、大きく儲かる可能性がありますよ、というのを描けるか、ですね。確実にこれだけ生産性があがるが、うまくいけば、倍までいけますよ、みたいな期待ですかね。
AM投資促進、コストダウンのロードマップ必要
寺(デンソー) 個別の投資の話で言えば生産技術は投資と効果の相場観を持っていて、通らない提案というのはそこからズレているということだろうと思います。費用対効果だけでなく将来性(ROI)を見て、自分たちのターゲット設定に合っているかを見ているのが一つです。なぜAMへの投資が進まないかという視点で見れば、装置が進化し、コストはこれぐらい下がっている「はず」だ、技術進化があり造形速度がもっと早くなっている「はず」だというロードマップへの期待があれば先行投資をするわけですが、信じてそれに賭けるだけのエビデンスがすくない。今ある装置の利点ではなく、どう進化し、どうコストダウンできるかというビジョンを共有できれば投資環境はずいぶん改善するのではないでしょうか。メーカーとユーザーが一緒にロードマップを作っていけないか、というのが冒頭に物流新聞さんがおっしゃったこの座談会の趣旨になるのではないでしょうか。
佐藤 開発費が設備費に大きく乗っていると思うので、桁が増えるくらい装置販売台数が増えれば自ずと安くなるとみているんですが。
寺 装置や材料の使用量が増えれば安くなるであろう、というのはもちろん想像できますが、何台買えば、今の半額になりますよ、とか材料も月何万トン買えば、これぐらい安くなるよ、というのが分かれば投資はしやすくなりますよね。当社だけでなく、トヨタグループでまとめて購入すればこれぐらい、自動車産業全体で協調していけばこれだけコストが下がるね、と普及とコストダウンのロードマップが共有できれば、具体的な調達計画が動き出すのではないかと思いますね。
――ここが本座談会の主題でもあるのでもう少し詳しくお聞きしたい。
寺 中国などは必ずしも日本よりすごい技術を持っているわけではなく、極論すればAMをたくさん並べて大量に作ることでコストをダウンしているわけです。これだけ作ればこれだけ安くなる、じゃあ頑張るぞ、とある意味、非常にピュアにがむしゃらにやっている。中国のやり方の是非や、日本で出来るのか、は置くとしてもたくさん並べるようなやり方がコストダウンの選択肢のひとつ。他にも高速化するなどの道がありますがメーカーさんは低コスト化にどう取り組んでいますか。ターゲット市場なども。
二井谷(ニデックマシンツール) DEDのコア技術は粉末を供給するレーザーヘッドですが、このユニットを内製化し、標準化を行うことでコストダウンを図っています。AMの投資促進について、通常工作機械を購入されるお客様は10年20年と長くお使いになられますので購入時は非常に慎重です。さらに、AMの場合は切削などと違い20年後どう変わっているかわからない。今のところ日本におけるAMの導入は、その会社の経営トップの意思にかかっていると思うことが多くあります。AM投資促進のためには、経営者同士のコミュニケーションが重要で、私が必要とあれば顧客に赴きたいと思っています。
松浦(松浦機械製作所) 我々はハイブリッド金属3Dプリンターでありターゲットにするのは金型がメインになります。マシニング、ワイヤー放電加工などの工程を如何に置き換えられるかに注目して機械の能力を設定しています。当社は大量生産して開発費を薄めていくという対応は取り辛く、コストと精度とスピードのバランスにフォーカスしています。同業他社の状況を見ながら、ちょうどいい位置取りをする戦略をとっています。
寺 日本のメーカーは海外メーカーと違いユーザーのいうことを聞いてくれるので、我々うるさいことをいう自動車産業としては、大変ありがたく思っています。
木場 AMに参入して、正直、日本の自動車産業のコストに対する要求は厳しいな、と。他社さんも似たようなお考えでしょうが、我々が機械の価格を設定する際には、ユーザーが3年程度でペイできるというのを基準にしています。例えば1個300万かかる部品を、当社のニアネットシェイプ工法を使えば100万円安く作れる。そういう仕事が50件あるとすれば、年間0・5億円の生産性改善です。2年で1億円、3年で1・5億円の生産性改善があれば、1億円投資しても効果がありますよね、という想定で機械の販売価格を考えていました。しかし航空、宇宙、エネルギーなどの産業と違い、自動車にはそんな高額な部品はありません、よね。ひとつひとつの部品で、数百円、数十円とコストダウンの努力を重ねている自動車産業にどう提案するか。半面、航空・宇宙・エネルギーなどの産業と違い自動車産業では桁違いの台数の購入が期待できます。寺さんが言われたように、台数とコストダウンという視点を持って我々も戦略の見直しが必要であると感じました。
寺 我々自動車産業側にとっての課題は、様々な部品やランニングチェンジに対応できるAMのフレキシブル性を取り入れるロジックがないんです。そういう意味で我々にこそマインドチェンジが求められているし、コスト算定方法に関してもサプライチェーン含めて見直していかないといけないのかもしれない。
AMでサービスパーツを
佐藤 昔は巨大なラインを作っていましたが、小さくしなさいという話で数万とか単位は変わってきていますよね。
西(マツダ) 完成車メーカーは大量生産をしていると思われがちですが、サービスパーツの少量生産も何万点とやっています。簡単なもの、難しいもの、量が多いもの、少ないもの、を如何に作っていくかという中で、AMには根底を覆す力があります。大量生産で金型に勝てるはずがないですが、数が少ないサービスパーツでも、現在は大量生産ラインで製造しなければなりません。生産数に合わせて金型かAMの選択はできると思います。ロータリーエンジンの部品は金型を少しずつAMへ置き換えていき、ずっと供給し続けようとしています。
前田(ジェービーエムエンジニアリング) AMの特性を生かし、機械自体を移動させるという運用の可能性もありますね。また現在Gコードで動いていますが、そこに付加価値をつけるような動きが出てくればユーザーの使い勝手も上がるのではないでしょうか。
――AMはモノづくりを根底から変えられる反面、従来工法の延長線で考えると「AMはまだまだ使えないな」「もう少し様子見だな」となりかねないですよね。しかしメーカーはどうしてもセールスを考えてその土俵に乗ってしまっているのではないですか。
前田 AMに面粗度を言われても困りますので、二次加工ありきで考えないといけない。日本の工作機械がさっと仕上げ加工をすればすごい面粗度が出ます。餅は餅屋にお任せすればいいわけで、AMに慎重な方は、モノづくりの前提が変わった時に、急いでご参加いただければいい。我々がすべきなのは、AMを先行してやりたいという企業さんのサポートをすることですよね。
寺 私は少しニュアンスが違ってマツダの西さんが自己紹介の時に示されたロードマップに、「図面を変えない」とのステップが書かれていますが、図面を変えずにAMで現行同等品を作るのは難しく、ドイツでもアメリカでも出来ていません。我々はここに挑戦しないとブレークスルーできません。AMは補給部品での活用が期待されていますが、今は「同じものが出来ないじゃないか」となっているわけです。「同じ土俵で勝負しない」というのはAM普及推進派の理論ですがやはり、同じものを作れますよ、というのが勝負どころではないかと。
佐藤 ユーザー側の参加者が大企業ばかりなので、議論が偏っている可能性もありますが、販売としてAMが大企業に売れていれば成立するのか、中小企業に普及していかないとビジネスとして難しいのか、いかがですか。
メーカー一同 富士山の裾野を広げていくように、中小含め数を取っていかないと難しいですね。
二井谷 メーカーの立場からすれば、来ていただいたユーザーのご要望には、区別なく応えていく義務があります。ありきたりですが、AMの長所を情報発信していくしかないわけです。大手から中小企業まで幅広くビジネスをしていますが、試作なしにいきなり受注というケースも結構あります。普及のためにテスト造形に力を入れていますが、結果としてテスト造形の時間と受注確率にあまり相関がありません。大企業とか中小企業の区別ではなく、挑戦したい経営者や、企業内のAM戦士をどうやって増やしていくか、にかかっていますよね。
設計が安心感を持って使えるように
大崎(大同特殊鋼) AMで部品を作るうえでは、設計部門の力が重要だと思うのですが、いかがですか。我々も、装置メーカーさんも接触が多いのは製品部門や研究開発部門、溶接や材料開発のカテゴリーで設計部門と会うことはほとんどない。すそ野を広げていくにはここが肝になってくるのかなと。国としても、例えば大学でDFAM(付加製造のための設計)の知識を広めていくなど後押しがあればありがたい。
西 個人的な考えになりますが、設計者の中に切削、研削、ここはAMというように、選択肢としてAMが入っていません。私は、先ほどワンボタンという極論を言いましたが、設計者の意識を変えるには、目の前に部品が出てこないといけない。データベースを使って設計者が自信をもって設計できるようにしていくのが近道では。鋳造だってそうやってすそ野を広げてきたじゃないですか、ということなんです。例えばエンジンは、切削などこれまでの加工をベースに確立された型があり、それを起点にアレンジなり進化なりをしていますが、AMは前提を根底から覆すわけですよね。自動車は部品が壊れたらいけないわけで、原理原則が分かってないと、設計者は安心して取り組めない。繰り返しになりますがユーザーとメーカーが一緒になって、設計者が安心して設計できる基礎データーを蓄積していきましょう、と思っています。
――AMが試作機から部品造形機へ、今、普及に向けての潮目が変わりつつあるのではないか。何か一言。
二井谷 AMにおけるコストと安定性という課題が解決すれば、それぞれの分野でどれほどのインパクトがあるかを考えなければいけないですね。それを実現した企業が現れたとき、先行者に追い付くのに何年かかり、どれだけの投資が必要になるか。それを総合的に判断して、どの段階で投資するかを決めていくことになるのでは。
松浦 AM戦士と呼ばれる先行者にリソースを投入して協働していこう、という議論が響きました。我々も似た考えで営業費を抑え、開発に注力しようとしています。発展途上の技術であり、ユーザーの要望を聞きつつ、我々の知見を投入して成功事例を作っていくという方針でやってきました。その中で、我慢比べの時期が訪れると思っており、最後まで立っていた企業が強い競争力をもつのではないかとこれまで考えていました。ただ、中国などの新興国の台頭を見ると、我慢比べをしているのがいいのかどうか。データベースを強固なものにするにも、富士山の裾野を広げる、マスを増やさなければいけない。日本の設備メーカー、日本の技術が世界で負けるなんて、たとえAM懐疑派の皆様でも嫌だと思うでしょう。我々の培った技術も知見も積極的に提供していくので、今こそ日本のモノづくりを、日本のAMを盛り上げるようにがんばりませんか。
木場(三菱電機) とても有意義な場となりました。今回は経営者を含めて会社の上層部の皆さんが集まりましたが、現場や設計部門にはまた違う課題やお困りごともあるでしょう。アメリカにはAMのキーマンが集まってご飯を食べながら話すイベントなどもあります。様々なレベルで、課題を共有できる場を作っていければ突破口が今よりたくさん生まれて来ると思いますね。
前田(ジェービーエムエンジニアリング) 今こそワンチームでやりませんか。マーケットが出来てないのに競争は出来ません。競争はすこしわきに置いてマーケットを作りましょう。再び世界のモノづくりをリードするための技術であるAMを、経産省さんにも頑張ってもらい日本全体を巻き込む大きなうねりにしていきましょう。簡単なものなら西さんが言うワンボタンが出来るような技術の開発に、当社も全力で挑んでいきます。
大崎(大同特殊鋼) 材料メーカーとして、装置メーカーと個別に話すことが多かったのですが今回の座談会や、自動車産業ユーザーからのご指摘も受け、装置メーカー同士が、企業の垣根を越えて連携できるところがあるのではないか。そうすれば我々材料メーカーも一社一社より、効率的にご協力できるいろいろな方法が出てくるのではないかと考えています。
寺(デンソー)当社はトヨタグループでありながら、マツダさんをはじめ全方位で顧客を持っており、その意味では自動車業界全体の意見を伺える立場にあります。その中で意見の集約も進めていきます。アルミダイカストを代替する補給部品を何とかAMで作れるように持っていきたいですね。
佐藤(豊田自動織機) AMの社会実装に向けて、我々がどんどんAMを活用していいところも、悪いところもオープンに発信していきたい。AMによってこれまで出来なかったことが出来るようになるのは本当に楽しいですよ。
西(マツダ) モノづくりのやり方を根底からひっくり返す一つの可能性がAMだと思っています。たまたま自動車という領域でやっていますが、共有できるところは共有してやっていければと思います。簡単なものから難しいものまで作ってみます。そして我々が得意なのは出来たものを検査することです。ここはおそらく設備メーカーさんのレベルを超えているはず。この検査データーをAMの発展のために共有することも吝かではございません。
星野(経済産業省)大事なのはユーザーの広がりですね。世界ではAMを使っていきます。今は、航空宇宙や医療などの分野で海外が先行している例もありますが、自動車含めあらゆる産業に広がっていくという観点では、日本も世界も横一線で、今よーいドン、と思います。これまで培ってきた高い技術を持つ装置メーカーや材料メーカーが日本には多くいます。様々なユーザーが、ここをAMでやりたいんだ、どうすればいい、と声を上げていくことが大事だと思います。また大企業だけでなく、中堅・中小企業にすそ野を広げていくことも大事ですね。皆さんから政府への期待もお聞きしました。オールジャパンチームで勝っていくためにも、その基本戦略やロードマップづくりの必要性を感じました。それとともに、各地域の拠点での活動も盛り上がってほしいですし、国際的な連携を進めることも重要だと思います。
〈謝辞〉
なお、この座談会は、ご参加いただいた皆様をはじめ、日本AM協会及びAM展示会「TCT Japan」(主催:JTBコミュニケーションデザイン)のご協力により開催出来ました。ここに明記し、心より御礼申し上げます。
(日本物流新聞2025年3月10日号掲載)