【タイ発】健闘する日本企業
- 投稿日時
- 2024/11/13 14:59
- 更新日時
- 2024/11/25 17:59
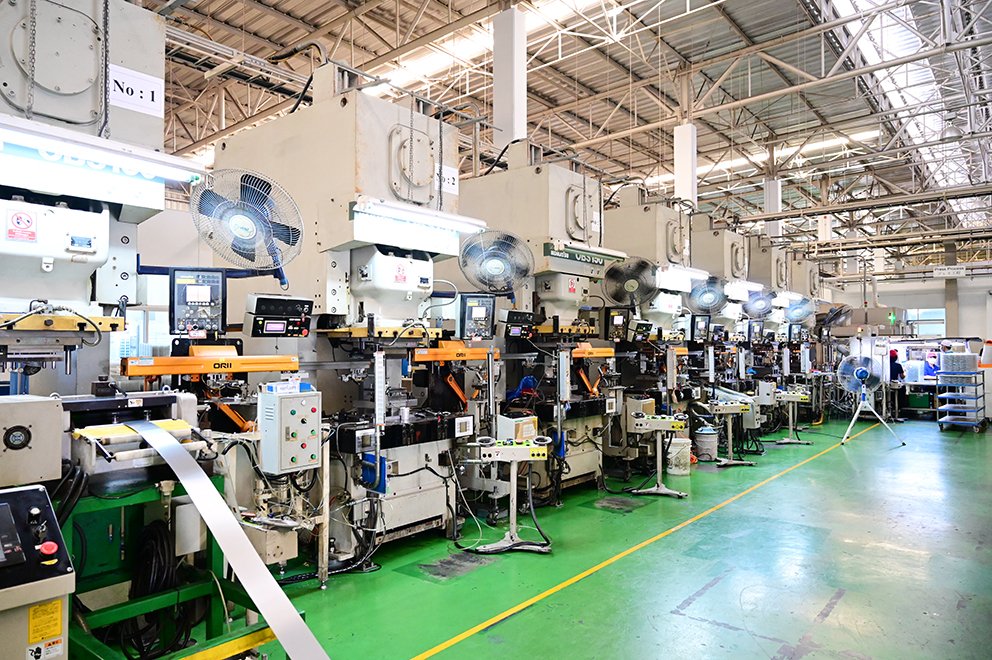
経済の停滞感を経て自動車産業の先行きは不透明だが、市場安定性に「一周回ってタイ」と再評価が進むタイ。米中摩擦が激化する中、新たな輸出基地として中国企業の活発な進出状況が続く中、変化対応に迫られる日本企業の取り組みなどを日本物流新聞記者が現地取材した。
ゼニヤタイランド、中国からの生産移管の風
捉えたプレス・切削・アルマイトの三拍子
「最近、タイの日系製造業で明るい話はほとんど聞きませんね」取材中何度も聞いた言葉だ。自動車の販売・生産の減少もあって製造業は全体的に軟調だ。その上、進出を加速する中国系企業との競争も激化し日系企業は厳しい戦いを強いられている。しかし、技術力と柔軟な営業力で逆風を順風に変え、飛躍する企業もある。
「ゼロコロナ政策」による都市機能不全の経験や米中対立を見据え、サプライチェーンの分散によるリスクヘッジで、中国からタイに生産移管が起こっている。金属プレス、異形切削からカラーアルマイトまで1拠点で一気通貫に行える技術力で、その風を捉えたのがゼニヤタイランドだ。
とはいえ、松尾文昭工場長は「中国の現行品を見た時『中国はここまでできるようになっているのか』と驚いた。それだけ中国のレベルは高い。中国は製造業の中心として多くの経験を積んできている。そことコストも含めて勝負しなくてはならない」と話す。
ゼニヤタイランドは、アルミの金属プレス加工を中心にステンレスやチタンの加工を手掛ける錢屋アルミニウム製作所(大阪府池田市)のグループ会社。錢屋アルミニウム製作所は近年米国大手客先向けの音楽プレーヤーやスマートフォンのケースなどの部品を手掛けるようになり、弱電筐体業界では名の通った存在になった。
右から松尾文昭工場長、廣田佳弘MD、藤原上之GM
ゼニヤタイランドはコンパクトデジカメの外装筐体の生産を受注したことで2011年に設立された。しかし、リーマンショックやコンパクトデジカメからスマートフォンへの移行により、当初計画していた生産がままならず、スマートフォンの部品の一部などを作りながらノウハウや技術力を高め、現在日系の一流カメラメーカーなどの新たな受注を獲得している。
例えばカメラのトップカバーだが「アルミの板をプレスして、表面を切削してアルマイト着色。最後に印刷もしている。1カ所ですべてできるところは東南アジアでは少ない。アルミ外装の難しい形を、歪まず破れず一貫で後工程まで量産できる点で東南アジアトップクラスと評価頂いている客先もある」(藤原上之GM)と自負する。
同社の技術力が一目でわかるカメラトップカバー
「ポイントは金型の技術だ。絞り加工で1㍉の板を成形するが、大阪で築きあげ、その後長年かけて培ったプレスの技術をタイでも引き継いだおかげ」と松尾工場長が補足した。
日本の技術をタイで再現するのは一苦労だった。「技術を持っているタイ人をスタッフに迎え入れているが、なかなか積極的になってくれない。師弟関係の様にずっと我慢強く側について教えていった」(松尾工場長)。
人材育成にはもう一つ大切な面がある。一流の「カメラや車載の部品をやっている」という製品の求心力のほか「22年の売上に比べて、23年の売上は1.8倍、今年24年は2.5倍となりそうだ。そういう成長の中で実戦の数をこなしていけることが技術者のレベルアップにつながっている」(松尾工場長)とし、企業が成長することがスタッフの成長を促していると分析する。
正社員だけではなく、一般的に離職率が高く技術が定着しにくい派遣社員も「ある派遣会社から『ゼニヤさんの派遣社員は物を見る目が正社員以上ですね』と言われた」(藤原GM)というのが自慢だ。
■タイ進出の中国加工企業との競争激化
ゼニヤタイランドは自動車部品の製造もしていたがあまり強くなかった。自動車以外を伸ばす必要性に駆られ、鉄ではなく得意なアルミ加工に集中した。これがカメラメーカーなどの所謂「脱中国化」によるタイへの生産移管の風を捉えた。生産移管の流れは続いておりカメラ以外の製品にもアプローチを強めている。
「ここ数年は中国からの生産移管による仕事を受注してきた。しかし中国のメーカーや部品加工業者がタイやベトナムにどんどん進出している。東南アジア内で中国系企業との競争になっていく」(藤原GM)と話すように、今度はタイ国内で日中の競争が激化しそうだ。
ブラザー工業の工作機械も多く並んでいた
「実際に加工するのはタイのスタッフ。設備だけ揃えてもすぐに日本の様に製造できない」とし「タイのスタッフを育ててきた実績と、さまざまな加工の要素を組み合わせることで差別化していく。あるいは他の日系メーカーとのコラボも考えている」(藤原GM)とする。
また松尾工場長も「中国の技術は高いが、総合的にすべて強いわけではないし、さまざまな技術を組み合わせるのは日本人が得意とするところ」と補強する。
廣田佳弘代表(MD)は「価格のみで勝負する気はない。技術力を売りにした差別化戦略が錢屋だ」と強調し「75年培ったゼニヤのプレス加工、特に絞り加工の技術は相当の重みがある。社員も誇りを持っている。既存の技術の棚卸をしつつ、新しい技法にもチャレンジしていく」と力を込めた。
【ブイの代名詞「ゼニライト」】
錢屋グループには、航路標識の世界的販売会社であるゼニライトブイ社があり、その受託生産として、岡山工場とゼニヤタイランドで製作を行っている。
航路標識を始めたきっかけは、港湾建設現場の従来の建設作業表示が竹竿の先に赤い布切れをつけたもので、日本国内である行政当局から夜間標識が無くて困っていると声をかけられたのが起点。「創業者社長が耐食性に優れているアルミパイプの先に灯器を付ければいいのでは、と思いついて製造した」(松尾工場長)。
ゼニライトというブランド名で、日本国内のシェアは8割、地方の漁師の間ではブイや航路標識を「ゼニライト」と呼び普通名称化しているという。また世界でもトップブランドであり、各国に供給している。
ホーコス マニュファクチャリング(タイランド)、中国EVメーカーの進出加速も日系部品メーカーへの波及無し
ディーゼルエンジンで培った重切削、農機 二輪 エアコン開拓へ
ホーコスは約9割の顧客が自動車関連だ。自動車産業の低迷が続くタイ市場でホーコス マニュファクチャリング(タイランド)も影響を受けており、農機、2輪車、コンプレッサー(エアコン)、ブレーキ部品などの加工へアプローチを強めている。
後藤壮一郎ディレクターは「自動車に関しては中国メーカーの投資は件数としてはたくさんあるが、日系の自動車関連企業では新しいラインを引くとか、設備を増強して増産するとかの動きはほぼ止まっている。EVシフトに伴う様子見で内燃機関のラインは当面しないでしょうし、特にタイではピックアップトラックの割合が大きいが、生産・販売とも落ち込んでいる。ピックアップトラックが動き出さないと当社の従来の仕事は増えてこないでしょう」。また「タイに中国系EVメーカーが進出しているが、組立メインのところが大多数で、タイ国内に加工の仕事がそれほど出てきていない。打診はあるようだが、実際に受注したという日系の部品加工企業の話は聞かない」と話す。
後藤壮一郎ディレクター
一方、自動車ではブレーキ関係が例外的に仕事は多くある。自動車の生産台数は変わらなくても、従来のブレーキと構造が異なる自動パーキングブレーキ搭載車の割合が増えているためだ。
■ベッドレスで省スペース化
タイ国内で製造するのは立形マシニングセンタ「NS70A(40番)」「NJ50A(30番)」、横形マシニングセンタ「Tシリーズ」、クランクシャフトなど軸物加工に向く「MBE80A」だ。
「NS70A」「NJ50A」の特徴はベッドレス構造による省スペース化で、ライン設置面積が従来の2分の1以下に収まる。「タイはまだまだ自動化が進んでいない。オペレーターの移動距離が少なくて済むので効率的だ」とする。また摺動部が機械上部にあるため、切りくずが直下に落ち、機外に排出されるのも、ユーザーに好感されている。
製造途中の立形マシニングセンタNSシリーズ
横形のTシリーズはディーゼルエンジンの製造ラインで実績があり「40番でもかなりの重切削に対応できる。タイの従来の市場は、ディーゼルエンジン車が中核。シリンダーブロックやクランクシャフトは鋳物のワークで、こうした機械の需要が高い」という。
微少量の切削剤(油性及び水溶性)と圧縮空気を主軸内先端部に設けたミキシング装置で混合し、生成されたオイルミストを切削刃具先端より噴射して加工を行うiMQLシステム。環境負荷が少なく切くずが機内に残りにくい水溶性iMQLは日本国内で大手自動車会社に採用されており、今後タイでの展開も視野に入る。
重切削が可能な40番級マシニングセンタをタイ製造しているのが同社の矜持で「ディーゼルエンジンを中核に据えた従来のタイの自動車産業で当社の成長モデルを描きたい」との思いはあるが現状では市場の動向は不透明でもある。
比較的好調なブレーキ部品や、タイへ生産移管が起こっている農機や普及価格帯の二輪車などへのアプローチ強化に加え、コンプレッサー(エアコン)の加工での受注を増やす戦略だ。「タイはエアコンメーカーの工場が多い。エアコンのコンプレッサーのコア部品には鉄が使われており、他社の30番ではやや難しい部分がある。またマグネシウムなどアルミや鉄以外の加工をされている工場もあり、こちらも特殊な切削技術が求められる」とし「車産業だけに目を向けていたら気づかなかった市場が見えてきた」と話す。他にもホーコスはインドに駐在事務所を開設しており、連携しながらインドへの輸出なども視野に入る。ピンチはチャンスと、新たな市場獲得へ鼻息が荒い。
OEI YAMANAKA、売上高の減少 手作りの半自動化とセンシングで克服
からくり改善による自動化装置 タイ人が試行錯誤
OEI YAMANAKAは「ファーストコールカンパニー」を旗印にするヤマナカゴーキンの技術ノウハウを完全移管して生まれた。タイ国内では製造できるところが限られる閉塞鍛造など、高い技術力を武器に自動車関連で高い評価を受ける。
しかしコロナ禍や自動車産業の低迷を受け売上高は2021年以降急激な減少傾向が続いている。さらにタイ人の最低賃金は操業開始時点(2012年)から23%増、会社登記時点(2010年)から言えば68%増、これを円換算すれば2倍から2・6倍になっており労務費増が追い打ちをかけた。
そこで同社が取り組んだのは高いスキルがいらない作業領域での「作業が簡単になる型設計」「自動化(半自動搬送)」「簡単な監視センサー」による効率化。「定常作業」領域で工数が低減し生産性の低下を防いだ。
ヤマナカゴーキンが金型の製造をしているため鍛造を手掛けるのはタイと中国の海外グループ企業のみ。「金型の顧客と競合しないように慎重な営業戦略が必要になってくる」(上野完治ディレクター)。機械加工を得意とするローカル企業「O.E.I PARTS」の合弁会社で同社が鍛造したワークを「O.E.I PARTS」が加工して完成品を出荷する。設備は主要部分にはコマツ産機のプレス機や東京精密の3次元測定機など高性能な日系メーカーを使用しつつ、台湾製やローカル製も活用してメリハリをつける。「特に測定の設備は高性能なものを揃えている。また測定治具をヤマナカゴーキンの金型技術で作っており、不良品率は日本の冷間鍛造企業の10分の1程度」(上野氏)と話す。
上野完治ディレクター(右)と八木哲司シニアテクニカルアドバイザー
ステアリングや等速ジョイント、デファレンシャルギヤなどEV化でも残る部品を戦略的に狙って営業しているほか、バイクのジェネレーター、コンピューター用の冷却関連部品などに広がっている。等速ジョイント、デファレンシャルギヤなどは閉塞鍛造という高度な技術が必要で、タイ国内で対応できるところが限られる。
■第二工場建設直後コロナ襲う
設立2年目に黒字化し、社長をタイ人に任せ自律的な成長軌道に乗った。満を持して2019年に第二工場を拡張するが、直後にコロナ禍が襲い「コロナ前に描いた拡張計画は白紙に戻り、コロナ禍が明けた後も中国系企業との競争激化で厳しい戦いを強いられている」(上野氏)とする。19年をピークに売上高も、出荷数も下降線をたどることになった。
そこで効率化に取り組み、手作業かつ定常繰返し作業をまず効率化。「予算が限られ、ロボットなどは入れられないのでからくり改善による手作りの半自動化装置をつくったり、簡単な監視センサーにより人を減らし、もうすこし高度な『要スキル作業』は警報付き監視センサーや条件制御センサーなどで効率化を進めた。品質と金型寿命をうまくコントロールするには職人的な経験が必要だがセンサーで誰でもできる作業にした」(上野氏)。
プレス機による鍛造の様子
八木哲司シニアテクニカルアドバイザーは「自動化・半自動化というと機械の前に協働ロボットを置いたりAGVが走り回ったりというイメージだが、当社では簡単な装置を手作りしている。作業者をサポートし負担を軽減する、というところに特化すればコストをかけてロボットを入れなくても一定程度はできる」とする。言葉で説明しにくいが「ピタゴ〇スイッチ」や「からくり屋敷」を髣髴とする、手作り感あふれるものだ。こうした取り組みで90人いた人員を61人まで省人化。日本人も立ち上げ当時は4人いたが、実質は1人で運営できるようになっており利益率が高まっている。
上野氏は「からくり改善による自動化は日本人が指示して作らせているわけではなく、タイ人から『ここはこういう装置があれば人を少なくできる』などの積極的な提案もあり、タイ人自らが試行錯誤して作っている」。八木氏は「楽しそうに作っている。今はバージョンファイブぐらいだ。バージョンワンは拙かったが、今はシステムインテグレーター並みのものを作っている」と両者、嬉しそうに話していた。
KENMIN FOODS(THAILAND)、自動化で60人を削減
「ケンミンの焼ビーフン」でお馴染みの即席焼ビーフンはタイ工場(KENMIN FOODS THAILAND)で作られている。ケンミン食品がタイに進出した理由は、ここまで取材してきた金属加工関連企業とは少し異なる。もともと戦後アジアから引き揚げてきた人や、アジア諸国からの移住者が「もう一度ビーフンを食べたい」という要望を受け、創業者の高村健民氏が、食糧難のため輸入されていたインディカ米を原材料に作り始めた。
ところが戦後の食糧難は過ぎ去り米余りになったことか69年に外国米の輸入が禁止された。日本米(ジャポニカ米)は柔らかくめん同士がくっつくのでビーフンには向かない。そこでビーフンに適したタイ米(インディカ米)を求めて89年にタイで第一工場を竣工した。そして2020年に人手に頼っていた工程を大幅に自動化した第三工場を稼働した。今回はこの第三工場を中心に取材を試みた。
インスタントラーメンの事業者は多いので、製造装置も汎用化が進んでいるが、ビーフンを量産している企業は日系では同社のみ。ビーフンは押し出し製法で製造されるが、製造装置はほとんど同社専用機となる。押し出しの装置も中国製を輸入して参考にしながら、独自に図面を引きタイのローカル企業に製造してもらった。
第三工場の乾燥機も完全オーダーメイドで失敗も経験した。当初導入した1段式乾燥装置では十分乾燥せず、2段にし、熱量も調整し完成に至った。「日本だと問題があればメーカーが駆けつけてくれるが、タイではメンテナンスはある程度自社でやらなければならない」(福村圭史マネージングディレクター)として、こうしたメンテナンス部門が機械の図面も引く。
工程を説明する福村圭史マネージングディレクター
同社のビーフンはタイのローカルビーフンメーカーでは行われていない2回目の蒸しと熟成が行われており、麺線がしっかりしている。これにより大量調理や、冷凍食品への加工で優位性がある。
第三工場は自動化に注力しており、最大のポイントは人手に頼っていた麺の計量部分。日系のコンピュータースケール企業と共同で、ビーフンライン専用のカスタムを施してもらい、30人の省人化を果たした。
また検査工程でもビーフン独自の問題を解決した。ビーフンはインスタントラーメンより麺線が細く割れやすい。細かい麺がパッケージの接着部分に噛みこんでしまう。
Ⅹ線検査装置で噛みこみを検査することは本来ないが、噛みこみ検査用としてラインに適用した。すべての工程で60人ほどの削減に成功し、現在30人で運営している。
■ロボット導入後、人手に戻った工程も
うまくいかなかった部分もある。焼ビーフンの箱詰めに協働ロボットを導入し吸引式のハンドを用いた。しかし麺が袋を突き破る事例が発生し、箱詰めは人手に戻った。
同社は欧米への輸出へアプローチを強化している。グルテンフリーの人気が高まっており、小麦由来のグルテンを含まないビーフンに新たな市場が広がった。
グルテンフリーは、セリアック病患者の食事として生まれた食事療法で、世界的に有名なテニスプレーヤーが、血液検査などを通して小麦や乳製品などが体質に合わないと診断されたことを機に、「グルテンフリーの食事にしたことで体の調子が良くなった」と著書を出版したことで注目された。
セリアック病患者に限らず、セレブの健康法として広がり、欧米では市場が確立しているという。
同社はグルテンフリー認証マーク「GFCO」の取得や、輸出しやすいように規制が強い畜肉系エキスを取り除き、小麦を含まないしょうゆを使った商品をタイからアメリカ向けに輸出している。
ビーフンの充填工程
(日本物流新聞11月10日号掲載)