特別企画:聖和精機、精度にこだわり続けた半世紀
- 投稿日時
- 2022/10/07 09:34
- 更新日時
- 2024/08/19 13:19
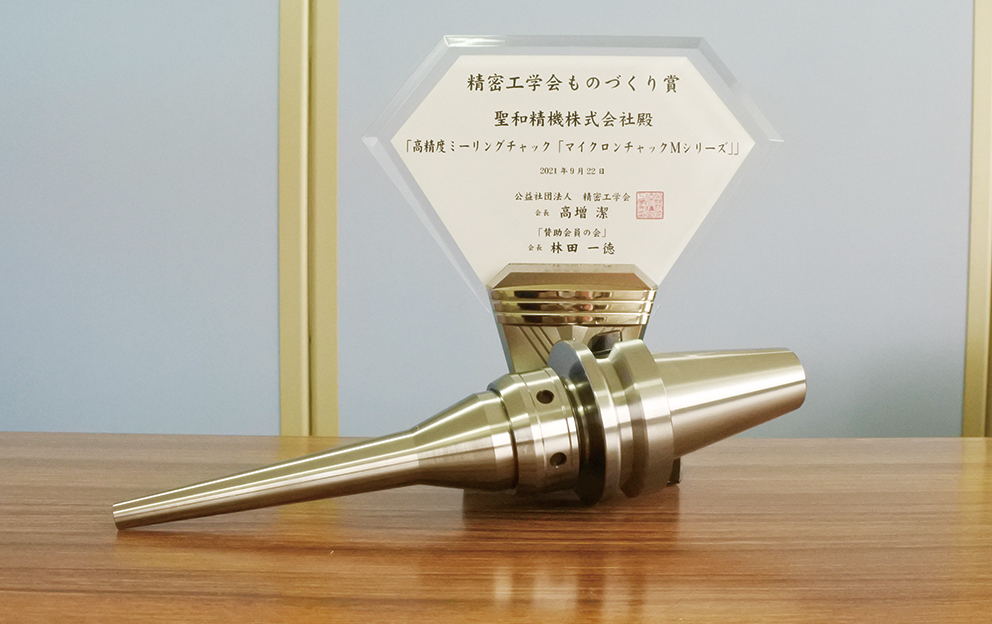
本年、創業50周年を迎えるツーリングメーカー・聖和精機(鳥取市・泉谷佳子社長)。工作機械と切削工具の持つ最大のポテンシャルを引き出し、なおかつ安定した加工を実現する同社のツーリングは、数あるメーカーの中でも大きな存在感を放っている。そんな同社の歴史と精度へのこだわりを探った。
鳥取市内の聖和精機本社工場
為替レートが固定相場制から、変動相場制に移行した1973年、聖和精機は大阪府豊中市で産声を上げた。創業者・廣海隆昌は「ユーザーに満足してもらえるツーリング」を追い求め社を興した。当時、たった4人でのスタートだったという。
優れた技術とアイデア、それを具現化する腕利きの職人が作り上げた同社のチャックは、実際に切削加工を行う現場から高い支持を得て、右肩上がりでシェアを伸ばしていく。
一方、著しい需要増とそれにともなう会社の成長によって、豊中の生産拠点に限界が訪れたのは1980代台初頭のことだった。そして1984年、企業誘致を進めていた鳥取県への移転を決意する。
同社の創業メンバーで現在は生産本部の特別顧問を勤める山口重盛氏は当時を述懐する。
「移転は大きな決断でした。当時はすでに社員も30人以上に増えていましたが、当然、鳥取には行けないから辞める、という社員もいました。ですので、移転の前から鳥取県で人材を確保しなければなりませんでした」
聖和精機・山口重盛特別顧問
団塊の世代ジュニアが社会に出ていた時期と重なり、採用にはさほど苦労はしなかったという。だが、即戦力として現場で働くには知識や技術が必要となる。ユーザーからの受注に応えながらの移転計画は、同社にとっての一大事業となった。
「大阪から鳥取へ来てくれた社員は半数ほどでしたので、新たに20名ほどの採用に踏み切りました。新工場が出来たらすぐに稼動できるよう、鳥取で採用した20名を1年間、豊中の工場で研修を行いました。現在、彼らがわが社を支える屋台骨になってくれています」(山口顧問)
時を前後して、同社にとっての看板商品であり現在も多くの加工現場において高い支持を得ている「マイクロンチャック」が誕生する。独自の機構により、ハイドロチャック並みの把握力と、焼きばめホルダ並みの安定性を両立する同製品は、振れ精度口元1ミクロンを保証している。自動車や航空機、医療機器、半導体など、高精度加工を必要とされる加工現場に相次いで導入されており、その市場は日本だけにとどまらず海外市場でも高い評価を受けている。
■工作機械に育まれた技術力
半世紀にわたり、モノづくりの現場に必要とされるツーリングを開発してきた聖和精機。その技術力の源泉を紐解くと、工作機械との密接な関係性が浮かび上がる。黎明期から開発現場に携わってきた山口顧問はこう語る。
「大阪の時代から、7割はツーリング、3割は工作機械に使われるスピンドルをはじめとした様々なパーツを委託されて生産していました。当社の技術力は、大手工作機械メーカーさんの厳しい基準をクリアすることで培われてきたものだと感じています」
スピンドルは芯ブレ、円筒度、真円度などを含む複合的な高精度が求められるゆえ、どこでも簡単に出来るようなものではない。同社には、創業まもないころから工作機械のキーパーツを委託され、生産できる技術ベースがあり、なおかつ工作機械の進歩とともに技術力もアップデートされていったことが容易に窺える。山口顧問はこう続ける。
「創業当時はNC機なんてありませんでしたから、汎用機での手作業がメインで職人の腕がすべてでしたが、当社のモノづくりも時代に合わせて変化しています。しかし、精度へのこだわりは、いつの時代も変わらず受け継がれています」
そんな山口顧問に、50年間の苦労話を伺ったところ「創業者はそれなりに苦労してきたと思います。バブルやリーマンショックなど、何度も荒波が来ましたから。でもそういった素振りは一切見せませんでしたね。仕事での苦労はさておき、創業から現在に至るまで、従業員は誰一人として不安に晒されるようなことは全く無かったです」と笑顔で語ってくれた。
究極の精度追求と次世代加工への対応
発売からすでに30年以上になるベストセラー「マイクロンチャック」。競合製品に勝るとも劣らない把持力と圧倒的な振れ精度はどのように生み出されたのか。同社生産本部の北村正吾本部長(兼・技術部長)に本社工場を案内してもらいつつ、解説していただいた。
「(マイクロンチャックの)原型となったトライチャックをベースに、先代社長が『もっと精度のよいミーリングチャックを作れないか』という鶴の一声でスタートし、当時は相当開発に苦労したと聞いています。すでに30年以上前の製品ですが、実はいま現在も細かいところでマイナーチェンジしているんです」
生産本部・北村正吾本部長
初期の製品からすでに10回以上の変更を行い、いまなお進化し続けるマイクロンチャック。高精度からさらに上へ。その原動力となっているのは、ユーザーによる声だという。
「当社はお客様の用途に応じてオーダーメイド品をお納めする機会も多いのですが、そういった中からヒントを頂いて実際の製品にフィードバックするケースも多々あります。マイクロンチャックの高精度は、お客様に育んで頂いている面も多分にあります」
製品をブラッシュアップし、具現化する生産設備は、様々な自動化が進められている。その一方で、「職人の技術」が必要な作業も少なくないという。
「研削の工程で、特にミクロン台の作業が要求されるパーツにおいてはやはり自動化は難しいですね。CNC任せには出来ません。当社には研削盤が多数ありますが、約半分は汎用の研削盤で、実際に人が手作業でパーツを削りだしています」
このミクロン台の研削に携わる技術者の年代は20代から50代と幅広い。技能継承がもっとも難しいとされる作業だが、若手技術者も意欲的に技能習得に取り組んでいるという。また、同社のモノづくりはひとつの工程に同じ技術者がずっと居続けるのではなく、一定期間を経て配置転換を行い、「多能工化」する取り組みも進めている。
ミクロン台の加工を技術者が手作業で行う
■積み重ねた知見を製品に活用
自社製品への自信の表れとも言える「精度保証」。それを実現しているのが、測定・計測部門だ。マイクロンチャックをはじめとする同社ツーリング製品は一本一本、出荷前に厳密なチェックが行われる。
「工作機械のスピンドル並みの自社製の測定装置を使用して振れ精度の測定を行っています。これは、実際のマシニングセンタの主軸にチャックを油圧で取り付けた状態を再現しています。また、各パーツの組み合わせでも精度がガラリと変わるので、組み立てにおいても細心の注意を払っています」
また工場内には自前の熱処理炉も備える。この熱処理も精度を維持する上で重要なファクターである。ツーリングの形状や処理炉内部の温度分布による熱の入り方の違いなどが膨大なデータとして蓄積されており、それら活用して細かなアップデートを行っている。
これら数々のこだわりが新たな製品、ツーリングソリューションとして、11月8日からのJIMTOF2022で出展される。北村本部長が自ら開発に携わったという防振アーバ「パワーサイレントアーバ」もそのひとつだ。
「上市したのは3年前ですが、コロナ禍もありまだあまり周知されていませんが、徐々に売れ行きも上がってきているようです。当社は防振に関しては20年以上前から大学と共同研究をしていますので、様々なノウハウを持っています」
この他にも「マイクロンチャック」の上位版である「ハイデュアルチャック」の荒加工特化型バージョンなどをお披露目するとしている。
厳密なチェックを経て出荷される
現場目線のツーリング提案
お客様に「稼げるホルダ」を
「私の切削に関する知識はすべてお客様に教えてもらったもので、お客様の加工現場で育てていただいたようなものです」。こう語るのは、入社以来32年に渡り、営業畑を歩んできた同社営業本部長の漆原正和取締役だ。
「私が入った頃の当社の強みは、供給力と価格面でした。大手メーカーさんに勝てるポイントで勝負する、というスタイルでセールスしていましたが、加工方法の変化や自社製品のラインナップにマイクロンチャックが加わってから売り方が変わりました」
取締役営業本部長 漆原正和氏
従来製品とは違い、明らかに性能面で優れているのがマイクロンチャック。それをあえてディスカウントして売る必要は無い。
「マイクロンチャックは振れ精度に優れているので、刃物の持ちがよく加工能率も上がります。結果、お客様のコストダウンに大きく貢献できます。それでも『チャックなんて安ければ良い』というお客様もいますし、従来からご愛顧頂いているお客様には多少の融通は利かせるようにはしていますが(笑)」
また昨今では、省力・省人化や自動化を見据えた「コレットレス提案」も行っているという。
「私の感覚では、加工現場で使われているツーリングの約7割はコレットチャックです。コレットチャックはコレットを変えれば様々なサイズの刃物を使えますが、実際の現場でわざわざコレットを交換して使用する現場が少なくなっています。生産性向上が重視される中、コレットの交換に時間をかける無駄を省くほうが、生産性は確実に上がりますし、ミス防止にも繋がります。こういった側面から、コレットレスのマイクロンチャックを提案しています」
近年、多くの工作機械に搭載されているオートツールチェンジャー(ATC)。マイクロンチャックはこうした自動化機器との親和性も高い。イニシャルコストはかかるが、トータルコストで見れば確実にコストダウンと生産性向上に繋げられる。すでにホンダをはじめとする大手自動車メーカーを中心にマイクロンチャックは続々と採用されている。
最後に現在も営業の最前線で活躍している漆原取締役に、昨今顕著なユーザーニーズを伺うと、意外な答えが返ってきた。
「昨今、多くのお客様とお話しているなかで、チャックにもデザイン性が求められていることを痛感します。精度や機能性はもちろんですが、見た目も良い製品を開発陣にお願いしていますので、今後さらにバリエーションに富んだラインナップをご提案できるようになると思います」
不可能を可能にする「聖和ホルダ」への信頼感
井沢鉄工所(兵庫県)
非鉄・耐熱合金の加工に強みを持つ井沢鉄工所。1968年の設立で、創業者の井澤季雄氏は東芝機械(現・芝浦機械)で部長職を務めていたといい、当初は三菱電機姫路製作所向けに特注の工作機械を製作していたという歴史を持つ。現在はガスタービン向けなどのエネルギー関連の部品加工をメインとしている同社が、切削加工において全幅の信頼を置いているのが聖和精機のホルダだ。
同社の工場内はとにかく清掃が行き届いている。海が近いということもあるのだろうが、ビニールカバーで覆われたツールラックに置かれたホルダは一本一本、ビニールで個別に包装されているなど、様々な道具が大事に扱われ、こだわりを持って使用されているのが見て取れる。
同社の井澤竜一社長は「清掃もツーリングの管理も私が指示したわけではなく、ありがたいことに全て社員が自発的にやってくれています。聖和精機さんのホルダも、現場が主導して導入を進めました」と語る。
井澤竜一社長
実際に導入に携わった同社第6工場の甘中良紀工場長と小野泰正班長が導入当初の経緯を説明してくれた。
「2000年頃からマシニングを使った加工が増え、それに応じて機械の台数も増えていきました。当時φ25、刃長110㍉のソリッドエンドミルを使用した加工を行っていましたが、従来のホルダでは振れ出しに苦労していました。そんな時に聖和精機さんの担当者さんが当社に来られて『一度マイクロンチャックを使ってみて下さい』とデモ機を貸して頂いたんです」(甘中工場長)
実際に使ってみると、想像以上の効果が出たという。
「ビビりやすいワークで切削条件を落とさなければ加工できなかったものが、マイクロンチャックに変更したところ、ビビりが収まっただけではなく、さらに切削条件を上げて加工できました。また、従来のホルダではチャッキングするオペレータによって振れ精度にバラつきが生じてしまいましたが、マイクロンチャックは誰がチャッキングしても均一の振れ精度に収まります」(小野班長)
ホルダひとつで劇的に生産性が上がり、手戻りも少なくなったという同社。井澤社長は「長期間の使用でも振れ精度の変化がなく、特注生産にも迅速に対応してもらっていますので、今後も当社では聖和精機さんのホルダを使い続けます」と力強く語ってくれた。
甘中良紀工場長(右)と小野泰正班長
(2022年10月10日号掲載)