特別対談:3M×TAFLINK
- 投稿日時
- 2023/09/28 13:30
- 更新日時
- 2024/08/19 13:20
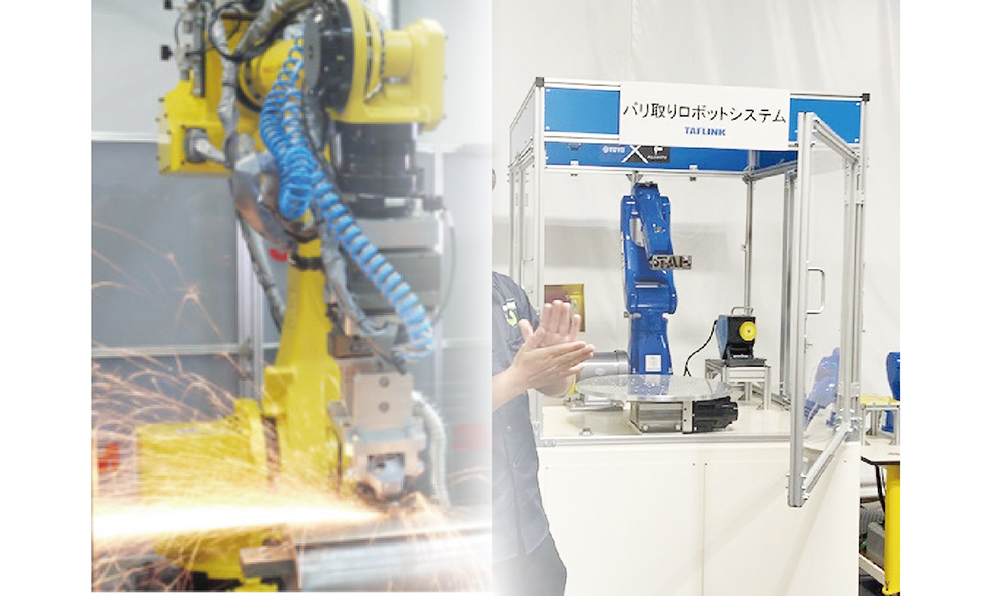
研磨材とロボ活用が変えるニッポンの「バリ取り」未来図
モノづくりにおける「QCD」を左右するバリ取り、研磨工程。しかしワークのサイズ、形状、素材などによって最適解が異なるため自動化が難しく、人に頼らざるを得ない現場も少なくない。こうした現場に対し、バリ取りに特化したロボットSier「TAFLINK」と多彩な研磨材と研磨ソリューションを有する化学メーカー「3M」は、大手から中小企業に至るまで最適な自動化ソリューションを提案している。
Chapter.1
バリ取り・研磨現場の課題
――製造業全体が深刻な人手不足に陥る中、バリ取りや研磨といった品質を左右する後工程がボトルネックとなりつつあります。
北村 人が集まらないゆえに廃業に追い込まれたり、事業を縮小せざるを得ない磨き屋さんやバリ取り専業メーカーさんが急増しています。これまで外注していたメーカーの内製化や、事業存続のための自動化など、TAFLINKとしてご相談を受ける機会も増えています。
佐藤 労働環境や賃金的な待遇面からも、若い人が入ってきてもなかなか定着しない、いま居る人材は高齢化でどんどん辞めていくが後継者がいない、という悪循環に陥りつつありますね。
だからこそ自動化を進めていくべきなのでしょうが、バリ取りや研磨はハンドリングプロセスのあいまいさから、二の足を踏んでいる装置メーカーやロボットSIerも少なくないと思います。
安藤 人手不足に加えて、火花が散り粉塵が舞う環境に人を置きづらいという労働安全面からも自動化需要は増えていますね。当社はTAFLINKさんのようなロボットSIerさんと連携して、お客様がどういう工程をやっているのかを見極めた上で、自動化に最適な研磨材を提案しています。
作業時間の短縮、工程集約、研磨コストの削減など現場によっては大幅なカイゼンに繋がるケースも多々あります。
荒木 かなり自動化を進めている現場でも、バリ取りだけは手作業に依存しているところもまだまだ多い。しかも、単純作業なのでみんなやりたがらないんです。
こうした「やりたくないが重要な仕事」の価値が製造業では低く見られがちな傾向にあると感じています。このあたりのマインドが雇用から設備投資にまで影響している側面もあると思います。
石野 いまだにバリ取り自体が根本的に人のやる作業、信頼度も人の手に勝るものはない、と考えているところも少なくありませんね。
TAFLINKのバリ取りロボットシステム「バリトリガー」
藤本 ロボットを扱う以上に人の管理やノウハウを共有するほうがはるかに難しいと思います。にもかかわらず、大手のメーカーさんでも、バリ取りの仕事は属人化しちゃっているんですよね。だからこそバリ取りは「触りづらい工程」で、その価値をはっきりと認識していないところも多いんです。
それゆえ、自動化するにあたり「そこまでお金はかけられない」となってしまうんです。採用や雇用の継続といった人材活用の煩雑さや投資対効果を考えれば、自動化は生き残る上で最良の選択肢だと思います。
松井 最近、色々なバリ取りの自動化やカイゼンの案件に携わらせて頂いていますが、北村社長が仰ったように、やはり廃業していくバリ取り屋さんもすごく多く、生き残っているところには想像を絶するような負荷がかかっています。そういった現場のお役に立てる自動化提案を行っていかなければと考えています。
Chapter.2
バリ取り自動化普及のカギ
――大手によるバリ取りの内製化、といった話もありましたが、中小メーカーは大手以上に危機的な状況に直面しているところも少なくありません。企業規模の大小にかかわらず、バリ取りの自動化を実現していくにはどうすれば良いでしょうか。
安藤 お客様は「ロボットシステムを導入し、ボタンを押せば全部やってくれる」と思われているのですが、それだと実はうまくいかないケースが多いのかなと感じています。よく「ロボットはあくまでも道具であり、ツールである」と荒木社長が仰っているのですが、それを前提にすると、ロボットは使いこなしていくことで真価を発揮するものです。
お客様にもこのマインドセットが広がってくると、もっとロボットの普及率が上がっていくのではないかでしょうか。
北村 ロボットを「魔法の杖」と思っている方はいまだに多いですが、実際にロボットは出来ないことのほうが多いくらいですからね。人間にもOJTがあるように、ロボットにも様々なティーチングを行ってアップグレードしていくことが、継続的な運用に繋がります。
松井 大手さんでよくありがちなのが、高性能のロボットを導入してみたが上手くいかない、というケースです。現場がロボットの使い勝手を十分に理解せずに運用しているところからは「改造したい」とか「新しいロボットに変えたい」といった声がよく聞かれます。
そうした現場では、改造しようが新しいものを入れても、同じことがまた起こってしまいます。
石野 バリ取りはノウハウや技術が必要な部分も多く、ベテランの職人さんですと要求される水準が非常に高いんです。実際にロボットを導入して頂いた企業でも、要求品質は確保できていても、現場の方からは「ロボットはこの程度なのか」とか「もっと品質上げられないの?」といった声が聞こえてきます。
実は我々もロボット導入した当初は同じような状況で、現場で少しづつ改善し使いこなしていくことで品質の向上に繋げていった経緯があります。ですから、導入現場への教育も非常に重要だと思います。TAFLINKでは導入前後の現場教育にも注力しています。
藤本 お客様でバリ取り内製化のためにロボットを導入したにもかかわらず、結局外注にお願いする、というパターンがありました。対象製品のバリの変化に現場と品質がついていけなかったんでしょうね。そういった意味でも導入後もロボットを柔軟に動かせる体制づくりが必要になってきます。
無論、完全自動化が実現できれば良いのですが、それには大きな投資が伴いますし、投資対効果が見込めるかにも疑問符が付きます。
荒木 昨今、センシング技術も発達していますので、お金さえかければかなりの部分まで自動化できると思いますが、継続的な運用にはさらに費用もかかります。そもそもバリ取りの自動化が難しいのは、対象ワークのばらつきが大きく、それを人の感覚からロボットに置き換えるのが困難だからです。TAFLINKはそれをなんとか自動化していこうということで、ばらつきに対して様々な機能やノウハウをロボットシステムに落とし込んでいます。
佐藤 当社も2019年に「ロボット研磨ラボ」を立ち上げて、様々な自動化検証を行っていますが、その中では、バリ取りや研磨の現場ではセンサで得た情報をフィードバックするハイエンドなシステムの考え方もありますが、今の段階では、フィードバックシステムを構築するよりも、自分たちでバラツキや品質を落とし込める、シンプルなシステムの方が運用しやすいと考えています。
スリーエム ジャパンの「ロボット研磨ラボ」
Chapter.3
バリ取り・研磨の未来図
――業界全体が抱える自動化への課題は「バリ取りの価値観」や「費用対効果の検証が不十分」、「継続的な運用が出来る人材育成」といった点が上がりました。
安藤 まず費用対効果の点ですが、実は当社の研磨材は自動化やロボットは、製品そのものの価値を認めてもらいやすいアプリケーションだと考えています。同じ研磨材でもAさんは5個、Bさんは7個削れたなど、人による運用は差異が生じますが、ロボットでは一定の動作で運用されるので、ばらつきが少なく研磨材そのものの実力がはっきり可視化されます。
佐藤 当社の製品は市場一般品と比較して価格が高いことが多いのですが、研磨できる数や面積が数倍以上という製品が多くあります。ですから、ロボットで使用頂く場合、研磨材の交換頻度が大幅に減らすことができるので、ダウンタイムや研磨材交換による品質変化の削減に繋がり、最終的には大幅なコストダウンに結び付きます。
こうしたデータやノウハウをベースとした費用対効果が見える提案もできますし、TAFLINKさんをはじめとしたSIerとの連携でさらなるメリットを生み出したいと思っています。
松井 実際に3Mさんの製品ラインナップは、本業のバリ取り屋である私たちも知らないようなスグレモノが多く、「こんないいものあったんだ」となることもしばしばです。加えて、膨大な研磨データをお持ちですので、私たちのバリ取りロボットシステムと組み合わせた上で、現場に最善の提案が出来る体制が構築されつつあると感じています。
安藤 TAFLINKさんにお伺いしたいのですが、現状、費用対効果による自動化と、人手不足に起因した自動化ですと、どちらが多いのでしょうか。
北村 そこは企業規模にもよると思います。私のイメージですと人手不足による自動化はやはり大手が多く、中小は費用対効果を重視しているように感じます。中小でロボットを入れて生産性が落ちたとなると死活問題に発展しますから。
荒木 規模感がそこまで大きくないところだと、その先のコスト改善だったり、生産性改善の戦略としての設備投資というような意味合いも含まれますね。藤本工業さんがいい例なんですが、投資対効果に不安はあるものの、実際にロボットを1台入れてみたらすごい効果があったと。それならば2台、3台入れていこうとなりますよね。藤本さんだけではなく、ロボットを導入し、活用出来ている現場からはリピートもありますし、TAFLINKのシステムを「安い」と感じて頂いています。
佐藤 藤本さんのところはどのような効果を実感したのでしょうか。
藤本 自動化したことによって5人でやっていたラインが、3人と1台で回せるようになったり、4人のラインで1時間100個のものが、ロボット1台と1人で、40個できるようになりました。実際に時間あたりの出来高としてはっきりとお金を生んでくれています。
ウチがロボットを導入したきっかけは「何かを変えていかなければならない」という思いが根底にあったからです。ですから、いちばんの導入効果は、社内にロボットを扱える、自動化を任せられる人材が育ったことや、荒木さん、北村さんとの出会いによるTAFLINKへの参画、3Mさんのような大手メーカーさんとの連携など、会社に新たなイノベーションが起こったことなのではないかと感じています。
■3M(スリーエム ジャパン)
1902年米ミネソタ州で創業。自動車塗装に革新をもたらしたマスキングテープやセロハンテープやメンディングテープ、簡単に貼って剝がせる付箋・ポストイットなど日常生活に欠かせない製品群を有する世界的化学メーカー。なかでも研磨材部門は最初の事業であり、サンドペーパーや耐水研磨材を開発・上市するなど、同社の中で100年以上の歴史と膨大なノウハウ、5000種類を超える豊富なラインナップを持つ。スリーエム ジャパンは1960年にアジア初の3M海外現地法人として誕生。以来、日用品からBtoB向け製品まで、日本のモノづくりを幅広く下支えしている。
■TAFLINK(タフリンク)
工作機械製造で培った技術をベースにロボティクス事業を手掛ける東洋鐵工所、中小企業への産業用ロボットの普及や技術支援を行うロボットSIerアラキエンジニアリング、アルミダイカスト部品のバリ取り・バフ研磨など仕上げ加工のエキスパート藤本工業の3社が連携し設立されたバリ取り特化型ロボットSIer。バリ取り・研削・研磨などを行う『バリ取りロボットシステム』の開発からロボット活用教育、バリ取り工程のコンサルまで、モノづくりのまち浜松から「世界一のバリ取り問題解決チーム」を目指して活動している。
(2023年9月30日号掲載)