AIで変わるモノづくり【後編】
- 投稿日時
- 2023/09/28 09:37
- 更新日時
- 2024/08/19 13:21
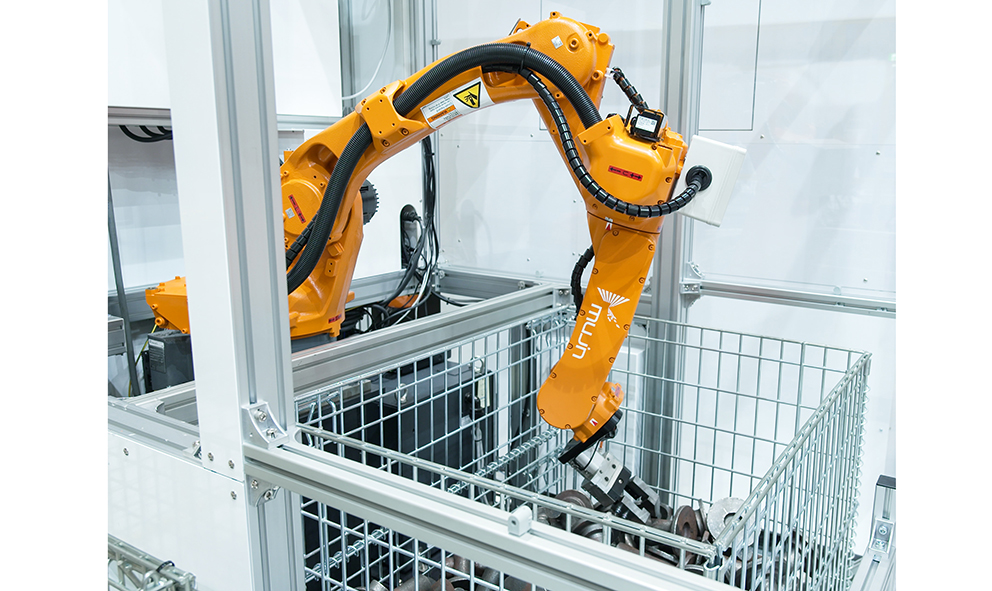
ロボットはAIでよりスマートに
2023年は「第4次AIブーム」の幕開けとも評される。ドライバー役は間違いなく生成AIで、実際、我々の暮らしとAIの距離は短期間のうちにかつてないまでに縮まった。もちろん、ビジネスシーンもこの動きと無関係ではいられない。むしろこれだけAIが浸透した世の中にあっては、その賢い利活用が企業の競争力を左右するともいえる。本紙では2号連続でAI活用の可能性を探り、前号では特に生成AIの活用に焦点を当ててきた。今号では生成AIに限らず、AIを積極的に使う企業の実例を、ロボット・ホルダ・部品調達など多角的な視点で取り上げる。
AI×ロボット
Mujin、独自の機械知能で自動化の旗手に
機械のための知能、すなわち「MI(Machine Intelligence)」。Mujinは自社のコア技術を、機械学習に代表される従来のAIと区別するためにそう呼称する。ヒトの思考回路を模すAIに対し、MIはある領域下で100%論理的な計算に基づきタスクを実行する。同社はこのMIを駆使し、他社が匙を投げる高難度の案件で教示レスの自動化を実現させてきた。
無造作にカゴに入れられた部品を、ひとつひとつ高速で取り出す。あるいは山になった様々な種類の段ボール箱を、事前のマスター登録なしでデパレタイズしていく。
本来ならロボット導入の難しいこれらのシーンを、Mujinは独自技術で数多く自動化してきた。鍵は「MujinMI」と呼ばれる機械知能だ。同社はこれをロボットコントローラに搭載。アルゴリズムに基づく最適な動作計画を自動生成し、しかも障害物を避けながら動くティーチング不要のロボットシステムをFA・物流業界へ提供する。
同社の言うMIとは、「ある一定の範囲内で論理的な計算に基づいてタスクを実行する機械のための知能」を指している。MIが導くすべての行動がロジックに基づくため、不測の事態が起きても要因を掴みやすい。ここがヒトの脳を模したAIとの違いで、例えば深層学習ではAIは学習で導いたルールをもとに『推論』で行動するため、ヒトと同じく必ずしも論理的な行動を取るという保証はない。思考もブラックボックス的で、異常時の原因追及も難航しがちだった。
Mujinは「深層学習と我々のMIにはそれぞれ得意な領域がある」と言う。「例えばSNSでタグを自動生成するなら深層学習が、失敗が許されない分野ならMIが適すると考えている。そして今のところ、失敗できない=稼働が止められない現場はFA業界と物流業界だ」
■MIを支える様々な技術
Mujinの技術を少し詳しく見たい。独自の動作制御を可能にしているのがビジョンシステムとMujinMI、そしてMIに組み込まれた2つの技術、逆運動学とモーションプランニングだ。
MujinMIを組み込んだロボットコントローラと一般的なロボットシステムの違い
まず同社のロボットシステムは常にワークと周辺環境を認識しているが、これを可能にするのが3次元カメラを用いた3Dビジョンシステム。そしてカメラで撮像したワークを起点に、MujinMIは逆運動学と呼ばれる技術で「ワークを掴むためにロボットの関節をどう動かせばよいか」を瞬時に計算する。また障害物や特異点(関節が伸びるなどそれ以上動かない状態)を考慮した柔軟な動作は、モーションプランニングという技術で実現。これは自動運転にも使われるもので、周辺環境をセンシングしながら目的地まで最適な経路で自走するクルマをイメージするとわかりやすいだろう。
認識して、動作を計画し、環境が変われば動作を変える。こうした一連の流れを、MujinMIはコンマ数秒の世界で繰り返しているのだ。同社は2023年3月に協和紙工(愛媛県四国中央市)へマスターレスかつマルチピック(可能なら複数のワークを同時に掴む)対応の混載デパレタイジングシステム導入を発表した。ロボット能力は1000ケース/h以上。高能力・高難度のこうしたロボットシステムは、MujinMIとそれを支える技術で実現したものと言える。
すべてのAIが人間の思考回路を模す必要はなく、機械には機械の、人には人の得意な領域がある。我々はMujinMIでFA・物流業界へ価値を提供する」
マスターレスのマルチピックデパレタイズを実現した協和紙工での例
デザイン×AI
生成AI 活用でカーデザインを1カ月半で遂行
完全自動運転車両の開発・販売に取り組むTuringが3月に公表したのが「完全自動運転EV」のコンセプトカー。モビリティデザインの実績を多数持つ日南と共同で製作したもので、デザイン・設計過程の随所に画像生成AI「Stable Diffusion」を活用した。
Turingと日南が生成AIを使って製作した「完全自動運転EV」のコンセプトカー
将棋AI「Ponanza」の開発者である山本一成氏と自動運転研究者の青木俊介氏が創業したTuringだからこそ、AIで自動運転車をデザインするという本プロジェクトは必然の流れ。計画の初期段階から生成AIが活用された。様々なバリエーションのイメージを大量に作ることができる生成AIの特長を生かし、通常の乗用車とは異なる要素(バス、クルーザー、電車など)をプロンプトに入れながら、2万枚以上の画像を生成させた。その中から核となる画像データを抽出し、それを教師データにして追い込んだ。日南・取締役の猿渡義市デザイン本部長は「素早くデザインの方向性を決めるには生成AIはかなり機能する。一方で、言葉だけで完璧な画像を出したり、一度で決め打つことは難しい。適切なタイミングで人間が介入する必要がある」と振り返る。
AIで生成した2Dデザインイメージから、最終的に3DCADデータ、CGレンダリング、走行アニメーション、フルカラー3Dプリントスケールモデル、VR/ARコンテンツを作成したが、この膨大な仕事量を約1カ月半で行った。猿渡氏は「デザイナーの描くものはあいまいな部分がたくさんあるため、次工程の作業者が困ってしまい仕事が進まないことがあった。AIは細部まで詳細に描かせることができる。明確なゴールがあったからこそ、短期間で様々な成果物を作り込むことができた」とし、「AIがデザイン開発に革命的な進化をもたらしている」と実感を持って話した。
環境対応×AI
工場のエネ消費ゼロ目指しZEF提案
日本政府はCO2排出を大幅に減らそうとゼロエネ建築物の普及を促進している。3月にZEB・ZEH︱M委員会が公表した調査では、累積のZEB・ZEH-M建物はそれぞれ644件と1406件に達するなど年々増加傾向にある。
2014年に業界に先駆けて「ZEB実証棟」を完成させた大成建設は、2021年にグリーンZEF(Net Zero Energy Factory)を打ち出し、工場のゼロエネ化にも乗り出している。ZEBでは工場のエネルギー消費の大部分を占める生産エリアの空調・換気・照明機器などが評価の対象外となっている。そのため、消費エネルギー削減量を正しく評価できず、工場のゼロエネ化の取り組みが進まない一因となっている。同社が新たに掲げるZEFは生産設備を除くすべての設備を評価対象とし、より工場全域に近い領域を評価できるようになった。同社の担当者は「ビルなど一般的な建物と違い、工場は基準となる標準モデルを作りにくいのが難点。ZEFによりエネルギー削減の目標設定を可能にすることで、工場のネットゼロ化を促進したい」とする。
ZEF化を支えるのが生産稼働状況に応じた環境自動最適制御「T︱Factory Next」だ。人の在室状況や生産装置の稼働状況に応じて照明・空調の運転モードを自動最適化することにより無駄を抑える(同社の調査では約20%の省エネに)。新たに追加したAIを活用した運用タイプは、気象データや生産設備の稼働スケジュール、過去の実績値などをAIで判断し、工場の負荷情報などを予測し、電源、熱源の最適な運転を自動で行う。継続運用によって一層の省エネ化を図れる。同社は「IoTにより幅広く備蓄されたデータを処理・活用するにはAI技術が重要となる」とみて、IoT化が進む工場のゼロエネ化をAI活用で一段と後押ししたい考えだ。
類似図面検索×AI
適切なサプライヤー選定で原価ブレ抑える
半導体の製造工程で使われるドライ真空ポンプの製造が「国内シェア1位」の樫山工業。コロナ禍で半導体需要が増え、生産効率化を目的にキャディの図面データ活用クラウド「CADDi DRAWER」を導入した。
図面の形状類似に関する独自のアルゴリズムで画像を自動解析して抽出、材質や文字情報とともにクラウドに登録し検索できる同ソフト。特徴は「AIが立体的な完成形を想定して、類似図面を探せる」(DRAWER事業部長の白井陽祐氏)点だ。
生産統括本部調達部の原京平主任は、最も大きい導入メリットを「類似図面の検索による原価低減」と挙げる。
「似たような部品でもサプライヤーによっては得手不得手があり、その選定を間違えると原価上昇に繋がる。AIが見つけてくる類似形状の図面には過去の発注実績も紐づいているので、適正なサプライヤーに発注できるようになった」と言う。
さらに、図面を検索すれば誰でも適正なサプライヤーを選べるため購買スキルの平準化、脱属人化にもつながった。
類似図面を検索するようす
当初は調達部門のみで活用していたが、今では設計・品質保証・製造・生産技術の5部門で合計50人が利用している。「図面の品番を知らない部門でも、キーワード検索でカンタンに辿り着ける。新図を作る前に検索し、重複図面を抑制したり似たような部品なら図面を共通化したり図面枚数を減らせた」。
当初の導入目的や部署を超えて、社内から活用の幅を拡げた様子がうかがえるが、一番の課題は利用の定着だという。
「利用促進のチームを社内で揃え、キャディ側のサポートと毎週打合せや、利用率の低い社員へヒアリングを行った。1~2週間で定着できるかどうかがポイントだろう」
生産計画作成×AI
ロボット、デジタルツインを総菜加工へ
(一社)日本惣菜協会は「"ロボフレ"による惣菜産業革命で人手不足解消」を目指すとともに、デジタルツインとAIを用いた工程の最適化や量子コンピュータを活用した人員配置の最適化にも取り組む。
同協会の荻野武氏は「人間の手の機微な動きをロボットに置き換える困難さはもちろん、中小事業者が多い食品業界ゆえに大きな投資もできない」と話す。
ベンダーらと協力し「惣菜盛付ロボットシステム」などを開発した同協会。荻野氏は「比較的安価なスカラロボットを用いた。ハンド部分にはロードセルを組み込み、重さをフィードバックして定量に保持する。また現場に技術者はいないのでティーチングレスにこだわり、惣菜の種類をリストから選ぶだけの簡素な操作で運営できる」。
コンピュータ上に仮想の工場ラインを構築するデジタルツインも食品業界での活用は遅れている。同協会にはデジタルツインの積極活用を推進する6社がある。その1社、魚宗フーズ(惣菜製造業)では、これまでオーダー情報と現場の制約(出勤状態やシフト、個々人のスキル、アレルゲン)を、熟練管理者の経験と勘で調整し生産計画を作っていた。ところがデジタルツインを用い数千・数万もの生産計画を作り最も適したものをAI(遺伝的アルゴリズム)で瞬時に選び出すことで生産計画作成の作成時間を80%短縮、必要作業者は8%削減できるなど効果が表れている。ただしシステムは構築できても、中小企業は必要なデータをとっていないことが多く「特にスキル情報などが不足している。今後は簡単なフォーマットを作りデータ化を推進する」(荻野氏)とする。
量子コンピュータを活用して人とロボットの最適なシフト計画を自動作成する取り組みも始まっておりマックスバリュ東海などが参加。KPIを明確にした従業員スキルアップ、全体最適シフトによる生産性向上に期待を寄せる。
生産効率化×AI
「うちに合った」曲げ提案で稼働率向上
「デジタルが得意な領域はソフトに任せて、従業員が製造現場に集中できる環境を作りたい」と語るのは、大阪府堺市でプレス加工・精密板金業を営むオシタニプレスの押谷義樹代表。
主に空調機器の部品製造を手がけ、少量多品種生産にも対応する。従業員7人でデジタル化を積極的に取り入れている。
プレスブレーキと同時に導入した、アマダのプログラム作成機能「ベンドCAM」。各パーツの曲げ加工が可能か検証でき、曲げ順序や使う金型と金型の配置・突き当て位置などを自動で決定する。作成したプログラムはマシンへ転送できる。人が考えていたこれらに要する時間が必要なくなり、マシンの稼働率向上に寄与する。
ベンドCAMで作成したプログラムで、曲げ加工を行う様子
「曲げる順序というのは、実は会社によってさまざま。データを蓄積させていくと、うちの会社の曲げ方の『くせ』を覚えてくれ、類似品を曲げる時にうちに合った曲げ順を提案してくれるんです」と押谷代表は面白そうに語る。「何種類も手掛ける品物の中で、板厚ごとに作業を分けてくれたり、複雑な加工では試し曲げで干渉を考慮に入れたシミュレーションも行えます。失敗による材料のロスを防げるのは大きい」と説明する。
とはいえ「あくまで曲げ工数の改善案として参考にした上で、作業者の知見で判断し、よりうちに合ったやり方をカスタマイズしています」と話す。それだけでも曲げの工数の改善効果は大きく、「段取り時間が削減できるので作業効率は上がっている」と言う。
「AIができないという加工も、人間の手による微妙な調整でできたりする。それは数々の困難をくぐりぬけてきた熟練社員のなせる業。残すべき知見や経験を受け継ぐためにも、デジタルシステムは適切に取り入れていく」と、AI活用がもたらす効果と培ってきた技術や工夫がうまくかかわりあう環境を構築していく。
工具・ホルダのIoT化×AI
加工現象を見える化
山本金属製作所のMULTI INTELLIGENCE(MI)は切削加工やFSW(摩擦撹拌接合)時などの温度・振動・力をモニタリングできるIoTデバイスだ。MIで得られた加工時のデータをAIが学習することで、摩耗した工具の自動交換などができる。
MULTI INTELLIGENCE
同社自らが切削加工事業を展開する中で、職人の五感に頼るやり方に限界を感じ「経験と勘を数値化しよう」と立ち上げた。市販のセンサでは工作機械の内部で高速回転する工具から熱と振動を捉えることが困難だった。そこでツールホルダ内部に温度、加速度、力センサを搭載し、得られた情報を無線で送受信できるMIの開発を目指した。振れ精度・剛性、大きさが従来のホルダと同程度でなければ実際の加工現場では使えない。通常のホルダのように一体型ではこの技術的課題をクリアできず、非常識ともいわれた分割型形状を採用した。
これまではベテラン職人の研ぎ澄まされた五感により工具異常や温度上昇を見極めていた。MIが加工現象を数値化することで人手不足、ベテラン不足の解消に貢献できる。
また加工状態のデータをAI(機械学習)に分析させるソフトウェアも自社で開発し、機械加工現場の自動化を実現。AIに正常な値を学ばせ、工具やワークに異常が起きれば停止させたり、工具を交換させるなど工作機械をコントロールする。「多くの自動化ソリューションでは、工具の異常検知と交換はまだ人の手が必要なことが多い。当社はそこの自動化に強みがある」(松田亮課長)という。
ある現場では工具寿命を3000個に設定していた。もちろん安全を見ての個数である。MIの振動計測機能をよりコンパクトにした
b-lexを用い、加速度から工具の摩耗度合いを判断した結果、平均3500個まで工具を使用することができ、コスト削減につながった。
(2023年9月30日号掲載)