拡大する自動化需要
- 投稿日時
- 2021/12/08 15:54
- 更新日時
- 2024/08/19 13:20
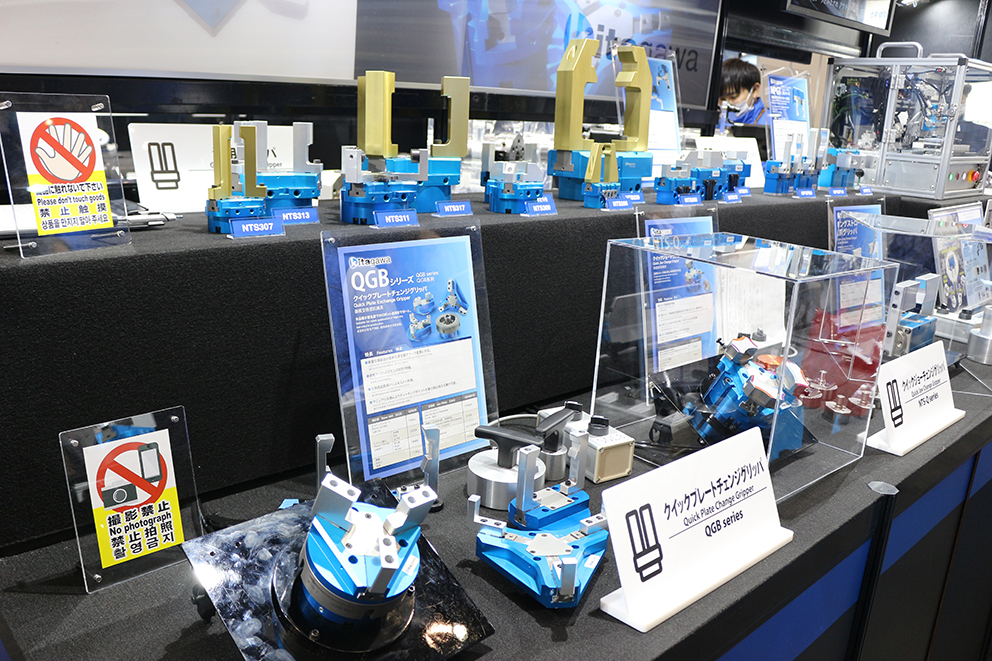
ロボット関連ツール動向
少子高齢化が懸念される日本にとって、ヒトの時間を最大限活用するうえでも、工程の見直しは避けられない。繰り返し作業に限らず、経験と勘が必要だった作業も、以前に比べてロボットへの代替が容易になった。搬送、接合、検査、バリ取り、研磨など、モノと数に最適なツールが増えたことは、自動化需要が拡大していることの証だろう。選択肢が広がった分、いかに用途に合ったツールを選ぶかが、自動化を定着させるうえでもポイントになる。そういった動きを踏まえて、ロボット関連ツールの提案動向を追った。
「省段取り」に勝機
ハンド交換の手間少なく
「ロボットで自動化する」と言っても、人の介在を完全になくすことはできない。量産、多品種少量生産のいずれであっても、段取り作業は不可欠。ワークのサイズ・形状・材質に合わせて、アーム先端に装着するハンドの交換もそうだ。ツールホルダーや治具と同じように、確実かつ高精度に、しかも短時間でセッティングする仕様が好まれる。
北川鉄工所は、ロボットハンドメーカーとして後発ながら、「省段取り」をキーワードに勝機を見出そうとしている。ロックナットの締め付けだけでハンドを交換できるようにしたり、爪(ジョー)の固定にピンを使用してボルト締めの手間をなくしたりといった提案だ。
2019年に新設した自動化システムチームで責任者を務める中本幸之介氏は、「ハンドの自動交換は技術的にも確立され、すでに普及している。ただ、搬送などの用途に絞った自動化を望まれる現場にとって、段取りの完全自動化はイニシャルコストが高い」と話す。
ハンドチェンジャーは継手や配管などを使用する構造上重く、導入するロボットも「可搬重量を1段階大きくしなければならない可能性がある」からだ。北川鉄工所は、あえて手動によるハンド交換を前提とした構造にすることで本体重量を抑えた。
省段取りを象徴する製品として、中本氏はクイックプレートチェンジグリッパ「QGBシリーズ」を挙げた。ロボットとの接続部分に「ベース」を装着した後、ワークに応じてハンドにあたる「面盤」(2爪・3爪)を交換する構造だ。
駆動源であるピストンをベース(固定部側)に設けることで、面盤(交換部)を軽量・コンパクト化した。交換方法は面盤をベースに挿入し、約60度回転させた後、ベース外周のロックナットを締め付けるというもの。ハンドを軽量化することによるロボット動作のスピードアップ、ストッカの省スペース化もメリットに挙げる。
中本氏は、そのほかの利点として「固定部側にエア配管を接続するため、面盤との間にシールはいらず、取り付けミスによる破損の危険性がない。さらにリードスイッチ取り付け溝を6カ所設けることで、プログラム上で使用するセンサを使い分けられる」と説明した。
動画で「NTS—Q」の爪交換速度をアピールする
■爪を数秒で交換
爪交換の手間を省く提案も展開している。クイックジョーチェンジグリッパ「NTS―Q」は、本体側面のノブを引き、爪底面の軸部で固定することで、爪1個の交換時間を数秒で完了させる。トルク値の管理が必要なボルト締めに比べて、「固定の確認がしやすく、慣れていない人でも扱える」点を売りにする。
ハードジョーは90度ごとに異なるR部を4カ所設けることで、φ23~79㍉の把握径に対応する仕様に設計した。「回転させて固定するだけで、複数種の把持径を兼用できる。チャックの生爪と同様、ワークのサイズと形状に合わせてカスタマイズできるソフトジョーも用意した」という。
中本氏は、ロボットの導入台数が増えている現場にも提案したいという。
「ミスがないように限られた人で段取り作業をしていたものの、台数が増えたことで運用が難しくなるケースもある。段取りや管理を平準化できれば、対応できる人を増やせる」
今秋開かれた「メカトロテックジャパン2021」の提案内容を、11月からバーチャルショールームとして公開。動画も合わせて見られるようにした。
治具の観点から提案
セットアップ時間短縮
加工の前後搬送が自動化されれば、オペレータの負担が少なくなる。モノを運ぶだけでなく、治具のクランプを含めた精度確保という意味も含まれる。だからこそ、工作機械とロボットの連携において、教示作業のしやすさ、位置決め精度の高さがアピールポイントになるわけだ。
オーケイエスは、治具の観点からロボット導入を提案する。使用するのは「ベビーカンガルーシステム」と呼ばれる製品。テーブル上に「マザーベース」を装着し、その上に治具を取り付けた「ベビープレート」を組み合わせることで、段取り作業を簡略化できる。
2面拘束クランプ方式を採用。繰り返し位置決め精度3ミクロン以内を維持することで、経験が必要なセットアップ時間を減らせる。ベースを共通化すれば、機械、ライン、工場が違っても、新しい治具とプレートを追加するだけで横展開が容易になるわけ。プレートの搬送方法は、台車だったり、レーンだったりと、現場によって異なるものの、自動化需要の高まりから選択肢の一つとしてロボットを加えた格好だ。
パッケージとして製品化した「BKS―ROBO Kit」は、ベース、プレート、ワークストッカで構成する。交換プレートの標準サイズに250㍉角と300㍉角を用意。シンプルな組み合わせながら、大神田佐敏社長は「専用治具メーカーとしての相乗効果を生み出せる提案」と語る。
これまで手がけてきた治具は4千種類以上。治具の構成要素を区分けしデータベース化することで、治具設計を「通常1週間から2週間で完成できる」体制を整えている。その迅速さを武器に、多品種生産の自動化に対応する考えだ。
工作機械、ベビーカンガルーシステム、ロボットのレイアウトを3Dモデル化して提案している(「BKS—ROBO Kit」
■協働ロボ対応も
多品種対応の一環として、年内にも小型30番マシニングセンタと協働ロボットの組み合わせを想定したセットアップキットを発売する。安全柵なしで稼働できる協働ロボットの利点を活かし、オペレータによる外段取りをしやすくした。
大神田社長は、「コロナ禍で密を避けたり、人との間隔をあけたりしなければならない状況にも対応できる。それにEVシフトで多品種生産、『マスカスタマイゼーション』の流れは加速するだろう。そういった意味でも、協働ロボットの需要は増える」と見る。
オーケイエスは工作機械を中心としたシステムインテグレーションも手がける。治具だけでなく、ワークの自動搬出入、バージョンアップを想定したライン設計も提案する。
ロボットも含めた自動化と省段取りを提案するうえで、売りにしているのは3Dデータによる構想案の提出。フィリピンの現地法人が設計し、「最短1週間で設計できる」という。
「人材育成とデータベース化の結果だ。設計の手順を言語化することで、工程の短縮を図っている。お客様が書いたポンチ絵から構想を起こし、モデル化することもできる」
データを活用した新たな取り組みとして、本社に3Dプリンターを導入。ワークや治具に合った特注ハンドの設計・製作も今後展開する計画だ。
半自動溶接と同じ感覚で
協働ロボの利点生かす
アークの細かな変化を確認しながら、条件変更ができる
搬送とともに、多関節ロボットが長年主戦場としている溶接は、自動車に代表される量産分野で活躍してきた。車体を挟むように複数台で溶接するイメージどおり、ロボットの導入には大規模な設備と広いスペースが必要だ。予算だけでなく、ライン変更、プログラム作成などの工数も考えれば、導入に中々踏み切れないのが現実だ。
そこでダイヘンはロボットを初めて導入する溶接現場向けに、協働ロボットシステム「Welbee Co―R」の販売を開始した。安全柵が不要な協働ロボットの利点を生かし、アークの細かな変化を近くで見ながら、半自動溶接とほぼ同じ感覚で条件変更ができるようにした。
導入のネックとなる教示作業は、アームを直接手でつかみ、動かして軌道を覚えさせる「ダイレクトティーチング」を活用。教示ハンドルにロック解除ボタンを設けることで、操作性を高め、細かな狙い位置の調整を可能にした。
溶接・接合事業部企画部の瀬戸口淳二課長は、「溶接品質を左右するトーチの角度を感覚的に設定できるので、半自動溶接に慣れている人にも扱いやすい。協働ロボットから半自動機にトーチを付け替えれば、使用状況に合わせて溶接電源を使い分けられる」と話す。
ロボットと半自動溶接のいいとこ取りはほかにもある。ダイヤルで電流と電圧を調整するモバイルリモコンだ。アークから目を離さずに変更できるため、条件設定の時間を縮められる。
瀬戸口課長は、「ベテランになるほど、アークを出しながら調整する方法に慣れている。半自動ならではの操作方法であり、条件変更しながらアークの変化が見られるので、技能伝授ツールとして応用できる」と自信を見せた。
ティーチペンダントには、初心者でも分かりやすい説明が表示される
■初心者でも設定しやすく
溶接条件を設定する画面は、必要な機能を集約した。ティーチペンダントにある「Welbee Co―R」ボタンをクリックするだけで、溶接プログラムの基礎となる10個のコマンド(溶接開始指示、溶接開始・終了位置など)が表示され、初心者でも説明書なしでプログラムの作成ができるようにした。
システム構成の一つとして緻密な波形制御が可能な溶接電源「Welbeeシリーズ」が使用できるのもポイント。軟鋼、アルミ、ステンレスなど、材料に応じたモード選択で、欠陥のない美麗なビードに仕上げられる。薄板から厚板まで適用できることから、「板金加工部品から産業機械部品までさまざまな溶接現場の需要を見込んでいる」という。
セットアップのしやすさも特長に挙げる。接続キットに付属するPLCBOXをロボットの制御装置に取り付けた後、BOXと溶接電源をLANケーブルでつなげば完了する。
瀬戸口課長は「限られたスペースに設置できる分、初期費用を抑えられる」として、中小の溶接現場を中心に提案する考えを語った。
自動化含めた締結の最適化へ
負担軽減とポカヨケ防止
協働ロボット、多関節ロボットの実演にも力を入れる。オートリベットフィーダー(写真中央)のデザインも一新した
リベッティングに慣れた人でも、1日に打てるのは1000~2000本。打ち続けていれば手首や腕への負担も相当なものだ。リベッターの軽量化と能力向上が進んでも、心身の負担を完全になくすことはできない。ロブテックスの提案は多関節ロボットも含めた締結の最適化。「自動化ありき」ではなく、作業頻度、現場環境、コストなどを総合的に判断して提案する取り組みだ。
商品企画チームの竹村和洋リーダーは、「短時間ならベテランの方が打つ方が断然早いし、ライン上ではエア、移動頻度が多い現場はコードレスと、リベッターのすみ分けはある程度されている。ただ長時間になれば話は変わる。身体的負担が増すだけでなく、打ち忘れなどのポカミスが発生する可能性も高くなるからだ」と指摘する。
ロブテックスは20年以上前から「オートリベッティングユニット」として自動化提案を展開。直交ロボット、専用機などで実績を重ねてきた。2010年以降、需要の高まりを受けて、メニューを拡大。多関節ロボットに組み込むヘッドユニット「ARU211M」のほか、協働ロボットに縦型エアリベッターを装着させたり、さらにポカヨケ防止機能を追加させたりしている。
ARU211Mを使った場合、最大で1日1万本は打てるそう。ブラインドリベットはフィーダーから自動供給する。昨年、ユニットの構造を見直して動力一体型に変更。「制御機器(PLC)をロボット側に委ねることで、ダイレクトに接続できる」(竹村氏)という。
さらに、可動域の制約となっていた油圧ホースを不要にし、ロボットに取り付けやすくした。販売にあたって、リベッティングの向きやスピード、リベットの供給ルートなど、周辺環境に応じてカスタマイズが必要な場合もあるという。
「システムインテグレータに納品して完結する商品ではない。打ち合わせから仕様決定まで時間はかかるものの、この手間こそ『ファスニングツールメーカーとしてこだわり』と考えている」
昨年発売した動力一体型ヘッドユニット「ARU211M」。可動域の制約となっていた油圧ホースを不要にした
■接合・締結市場にも
想定するユーザーは自動車産業に代表される組立ライン。リベッティングだけでなく、溶接などの金属接合・締結分野に間口を広げた展開も描く。
モノづくり事業本部の田邉浩樹副本部長は、「確かにリベッティングはニッチな分野。ただ工程改善という切り口で捉えれば、接合・締結市場に提案できる余地は十分にある。最近も産業機器の組立向けに、協働ロボットとの組み合わせで採用が決まった」と話す。
接着・接合EXPOやロボデックスなどの展示会にも出品し、「反響を得ている」という。田邉副本部長は「自動化は究極のカタチ」としながらも、「最善の手法とは限らない」と答えた。
「商談展示会ではエアリベッターがよく売れている。作業に慣れているということもあるし、生産ラインを変えられないのかもしれない。自動化、半自動化、手動の見極めは難しい。そういった意味でも『自動化ありき』ではなく、『リベッティングのことなら何でも相談してください』と伝えるようにしている」
(2021年12月10日号掲載)