検証MECT2023
- 投稿日時
- 2023/11/10 10:26
- 更新日時
- 2024/08/19 13:20
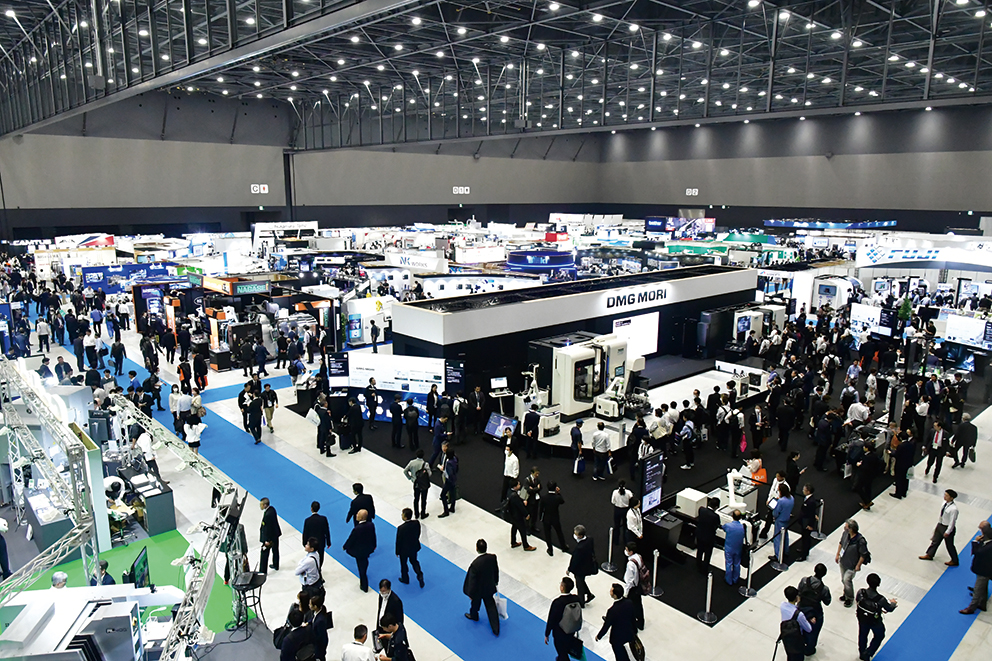
7万7000人が愛知に集結
自動化・工程集約は次なるフェーズへ
西暦奇数年では国内最大の工作機械見本市﹁メカトロテックジャパン2023(MECT)」が月日、4日間で7万7225人の来場者を集めて盛況裡に閉幕した。アフターコロナで顕在化した人手不足を背景に、各社のブースでは自動化・工程集約に資する提案がいっそう勢いづいた感がある。一方でカーボンニュートラルやDXという巨大な潮流は自社のコンセプトをPRする段階を過ぎ、より具体的な製品、あるいはサービスとして結実しつつあるようにも映った。とはいえMECTの中身はこれだけでは到底、語り尽くせない。今回展では何が披露されたのか。本紙記者の取材レポートで振り返る。
注目集める加工法
広がり見せるFSWやAM
まったく新しい加工法を見ることはなかったが、近年話題になったFSW(摩擦撹拌接合)やAM(Additive Manufacturing=積層造形加工)で進展が見られた。FSWに再び注目が高まった発端は、米テスラ製EVのバッテリーを解体するとあちこちにFSWが使われていたからだと大手工作機械メーカー幹部は漏らす。また「中国、東南アジアはFSWを使ったモーターケースなどの量産段階に入った」と話す複合加工機メーカーもあった。
芝浦機械はFSWによるワークを並べ曲面部や外周部、異種金属を接合できることを示した。
芝浦機械は自社製工作機械に機能付加するかたちでFSWを提案した。「10%ほどの価格アップになるが、門形でも立旋でも横中ぐりでも専用のヘッド周りと工具を付加することでFSW仕様になる。マシンに機械剛性があるからね。異種材接合で特に必要になる工具のノウハウなどを当社は持ち、熱がヘッド側に伝わらないような工夫も施している」(冨田佳一工作機械カンパニー長)と話す。同社は2007年から提案を始め、この4、5年は半導体や航空宇宙、化学プラント分野から受注が増加。FSW仕様機をこれまでに10台以上販売したという。
ヤマザキマザックのFSWは既存の3軸立形MC「VTC」「FJV」の機能付加のほか、昨年のJIMTOFで発表した専用機「FSW-460V」がある。前者は2014年から提案を始め半導体分野など向けに10台弱、後者は海外向けを中心に約10台の販売実績をもつ。利点として同社は「接合方式としては専用工具にプローブ(先端の凸部)とショルダー(外周部)を設けたことで力のかかる主軸を守ることができる。専用機はBT40番だが60番並みの主軸剛性をもつ。それでも銅の接合は厳しいが、VTC、FJVの機能付加なら銅接合も可能」(商品開発本部アプリケーション1グループ)と言う。
ヤマザキマザックが専用機「FSW-460V」で接合するようす
今展での実機出展はなかったがホーコスも複合加工機でFSWに取り組む(納入実績はまだないそうだが)。限りなくドライに近いセミドライ加工(iMQL)により、切削加工後のFSWを、乾燥工程を挟まずにスムーズに移行できるのがウリという。
■ドイツで使われるミネラルキャスティング
AMで少し変わった提案をしたのはドイツに本社を置く加工機・自動化・組み立て設備メーカー・GROB Japan。昨年度からAMに参入し、「GMP300」でアルミなどの金属ワイヤをポットで溶かして造形する。金属3Dプリンターは金属粉を使ったパウダーベッド方式が一般的だが、火災の危険や熱ひずみが起こりやすく専用のパウダー価格は高い。本製品はインクジェットプリンターで液体インクを紙に載せていくように積層するため、加工時間が比較的短く、量産に向く(写真のワークなら2時間40分で造形)。ワイヤも専用のものではなく、一般的に売られている溶接用のアルミワイヤに近い素材であれば積層できるため、試作品の製造も低コストで行える。同社の担当者は「小ロットのワークを造形するのであれば、鋳造の代わりに用いることもできるようになってきている」と話す。
GROBの液体金属プリンティング「GMP300」で造形した部品。大きさは約20cm角×高さ5cm
新素材として期待されるミネラルキャスティングの工作機械への適用の可能性がある。マンホールのふたで国内トップシェアを誇る日之出水道機器はこの素材を普及させようと、ドイツに本社を置くRAMPF Groupの日本法人と提携した。ミネラルキャスティングは骨材を樹脂で固めたポリマーコンクリートの一種。鋳鉄(FC300)と比べ約10倍もの減衰性能を持ち、びびりを抑えてミクロンオーダーを狙ったり機械の動作を早めるなどの目的でドイツなどではハイエンドな工作機械に使われているという。しかし鋳鉄と比べ重く剛性に劣るなどのデメリットもあり、国内で生産する工作機械では海外向けの一部の機種に採用される程度にとどまるのが現状だ。日之出水道機器は「ミネラルキャスティングには一長一短があるが、要は使い分けだと考えている。例えば重くなっても構わないベッドはミネラルキャスティングで、それ以外は鋳鉄にするなど。またトポロジー最適化の手法を取り入れ、鉄で組んだ力学的に理想形状のフレームの内部にミネラルキャスティングを充てんするハイブリッド方式も考えられる。これなら剛性も減衰性も高められる。価格は上がるのでハイエンドな機械向けにはなるが、国内でも需要はあるはず」とする。
自動化と工程集約
会場のいたるところに
会場のあちこちで見られたのはロボットを利用した自動化だった。DMG森精機は巨大ブースを目いっぱい使ってMX(マシニングトランスフォーメーション)のプレゼンテーションを繰り返した。森雅彦社長は「工程集約をテーマとし、展示機械を2台に絞った。複合加工機『NZ DUE』『NTX 1000 2nd Generation』は5台分の加工を1台で賄えるような生産性の高い機械」と自信をもって紹介。来年の正式発表を前に披露した新操作盤「ERGO line X」は大型のタッチパネルで直感的に操作でき、使用シーンによって必要なボタンを表示し、操作ミスを防ぐ。また実演ではNTX 1000 2nd Generationとフレキシブルな配置が可能なワークハンドリングシステム「MATRIS Light」により多品種少量生産の自動化をアピール(=写真左)。自動加工を妨げかねない切り屑やクーラント、オイルミストなどの処理の在り方も提示した。
DMG森精機は複合加工機「NTX 1000 2nd Generation」とワークハンドリングシステム「MATRIS Light」を組み合わせた。
利用する協働ロボットの可搬重量は高まっており、ヤマザキマザックは可搬重量30㌔の協働ロボットセル「EZ LOADER 30」と複合加工機を組み合わせて国内初披露。完成品と素材を一度に掴めるダブルハンドと重量物を掴めるシングルハンドを自動で柔軟に切り替えて見せた。可搬重量が上がったことで鉄系ワークにも対応。また従来はタブレット端末からワーク長やサイズなどを手動で入力する必要があったが、CNC装置とデータ連携することで90%の項目が入力不要になる。特にワーク重量の入力が要らなくなった恩恵が大きく、「重心はワークごとに違うがロボットの可搬重量には限りがあるため、今までは負荷設定を経験に基づいて入力する必要があった。これが不要になることでより使い手を選ばなくなった」と言う。
量産ラインを得意とする豊和工業は、30番の横形MC「HMP-350HC1」に協働ロボットとAMRを組み合わせた「止まらないマシン」を披露した。その真意をたずねると「機械室と加工室を完全に分けており切粉トラブルがない。また刃具寿命をMC側で管理しており、寿命が来ればAMRとロボットに指令を出してマガジンの工具を自動交換する」とのこと。一方、第3展示館ではSIerとしての顔も披露。ピンを押し込むだけで爪交換ができるチャックと立形MC向けのエアバイスを参考出品し、どちらも自社で教示したロボットを使って爪を交換してみせた。「従来はAJC対応のために爪のロック解除装置を取り付ける改造が必要で自動化のハードルが高かった。このチャックとエアバイスなら改造が不要。今のところ他社のチャックは爪交換に工具が必要なものが大半だと認識しており、開発を急ぎたい」と意欲を示した。
ロボットでピンを押し込むだけで爪交換ができる豊和工業のチャック
長尺ワーク用旋盤も自動化が進む。大日金属工業は人気の高いCNC旋盤「DL530」に、可搬20㌔の協働ロボットを組み合わせて参考出品した。ロット加工にも対応でき、「自動運転により夜間の無人運転や省人化、ロボットを退避させれば職人による手作業も可能。汎用旋盤、自動サイクル旋盤、CNC旋盤+ロボットなどいろんな役割を担え、様々な生産バリエーションにフレキシブルに対応する」と柔軟性をアピール。
大日金属工業が提案するCNC旋盤とロボットの組合せ。ロボットの着脱作業は15分で、スムーズに行える。
■ロボで穴あけ・バリ取り
ロボットのアプリケーションが充実してきた。トライエンジニアリングは200㌔可搬などの大型でなく、60㌔可搬のロボットで穴あけ(ヘリカル加工)やねじ切り(M6)ができることを実演して見せた。軌跡精度が高まった(±0.1㍉で真円が描ける)ファナック製多関節ロボット「M-800iA」を用い、穴あけにはイワタツール製工具を、ねじ切りにはスギノマシン製ヘッド(回転、送りを同期して制御)を利用した。
ファナックがY軸ストロークを500㎜に拡大した新型ロボドリルで実加工した700×「470」×184㎜のインバータケース
ロボット用バリ取りホルダはカトウ工機やムラキ(9面に囲み記事)が提案。カトウ工機の「SME40A-DBR7-1D」は「人間の手の動きに近づけるためフローティング機構がつきワークの形状にならっていく」と話す。寸法誤差を伸縮機構により吸収し、設定荷重はYELLOW=弱、GREEN=中、RED=強の3種類。シャンク径3~7㍉の刃物が取付け可能。「現在はマシニングセンタでのバリ取りの需要が多いが、ロボットに目が向いてきているのを実感している」と手ごたえを話す。
FUJIは「なんでもカメラ&なんでもハンド」なる自動化システムを参考出品。「ハンドに取り付けたクッション機構をエアの吸圧で固化させるため、どんな形のワークにもなじんで掴める。これとハンドに取り付けた3Dビジョンを組み合わせ、事前にワークの3Dデータを取り込むことなくあらゆるワークのハンドリングを自動化することを目指している」と言う。会場では自社製の多関節ロボを使い、旋盤へのワーク投入を自動化した。
■小型機で大物ワークを
小型機単体での工程集約も進む。エンシュウは主軸15番の立形MCの微細加工性能を高め(左下に囲み)、ファナックが今春の自社展でも披露した30番立形MC「ROBODRILL α-D28LiB5 ADV Plus Y500」は工具収容本数(従来21本→28本)、Y軸ストローク(400㍉→500㍉)が拡大し、「大物ワークの加工を工程集約できる。主軸回転数は毎分1万~2.4万から選べる」と自信を見せた。
昨年・今年と4機種ずつ新たな機械を投入するなど新製品ラッシュの最中にあるブラザー工業は、30本マガジンを搭載した30番MC「H550Xd1」を目立たせた。SPEEDIOシリーズで初の横形で「長尺ワークにも対応でき反応はかなり良い。コンパクトさとATCの速さに反響があり発売早々実機を見に来る人も多い。引き合いはすでに多く順調に受注につながるはず」と期待する。設置スペースは約4.7平方㍍と同ストロークの40番機と比べ20%減。特に機械幅は1557㍉とスリムに仕上げた。一方で治具エリアは直径600、高さ580㍉と広い。
■複合機で加工時間カット
2021年に複合加工機市場に参入したFUJIは、「複合加工機の主要市場に切り込むマシン」(同社)と位置づけるY軸付き2スピンドル複合旋盤「ACUFLEX」を国内初披露。1タレット仕様を今年12月、2タレット仕様を来春発売する。本来はサブである右主軸の剛性を高めたことで加工能率に優れる一方、左主軸で「クラス最大」という直径790㍉の振り回しを実現した。このサイズの複合旋盤は競合が多いが、担当者は「そのぶん市場も大きい」と前向き。差別化のためタレットにBMT45~60規格までの市販の回転工具を取り付けられる独自機構(特許出願済み)を搭載し、「手持ちの資産を最大限活用できる」とウリを話す。
FUJIの1タレット仕様のACUFLEX400S
中村留精密工業はマルチタレット型の対向2スピンドル複合旋盤「WY-100V」を国内初披露。油圧バルブ部品で加工時間を従来機種比30%カット(536秒→375秒)できたのは「クロノカット」なる新技術だ。アイドルタイムを削る15以上のソフト的機能の総称で、切削条件に影響を与えずユーザーからすると純粋にメリットとなる。たとえばC軸の割出し速度向上、ワークの受け渡し高速化などがその中身だ。一方、熱を逃がす構造を取り入れ8時間連続加工時の寸法変化を3ミクロンに抑える。ミーリングの回転数は毎分6千から1万に高速化しつつトルクもアップ。「つまりメカとソフト両面からのアプローチでサイクルタイムを縮めた。中村留の技術をかき集めて開発した」とする。
研削盤の工程集約を提案したのはジェイテクトマシンシステム。異なる直径が複数存在するシャフト研削は通常マシン3台ほどを使って工程分割する必要があるが、広幅円筒研削盤「C6040E」は1台で全面同時研削が可能。「台数削減によりライン長が約70%削減でき、圧倒的なスペース生産性をかなえる」とアピールした。直径4~120㍉、全長450㍉メートルのワークを一度で研削完了。高剛性の両持ち砥石軸の採用によりワークたわみの左右差を「理論上ゼロ」(同社)にし、工作物全長に渡ってテーパの発生を抑制する。
ジェイテクトマシンシステムは広幅円筒研削盤C6040の全面同時研削を実演した。
新たな市場ニーズへの対応
ギガキャスト、鋼材加工に新提案
テスラが先鞭をつけたギガキャスト。先般開かれたジャパンモビリティショーではトヨタ(レクサス)もデモカーに採用するなど、クルマ作りにも新たな加工ニーズが生まれている。
ドイツに本社を置くGROBはワークエリアφ3100㍉×2000㍉の加工エリアを持つG920Fを提案。機体上部からガントリーを使用したワーク投入やロボットを使用した正面からの投入が可能で、ギガキャスト部品や大型バッテリーケースなど大物ワーク加工を実現する。
「車体フレーム・シャシー部品の加工にも最適。MQL(微少量潤滑)によるセミドライ加工にも対応する」(同社)
スギノマシンは、大型型部品加工機「GIGAFEEDER(ギガフィーダ)」を展示。ドリリング・タッピングユニット「SELFEEDER(セルフィーダ)」をベースとした主軸を最大6本搭載可能。各軸ともX軸1850㍉Y軸1450㍉Z軸350㍉のストロークを持ち、大型部品の加工に十分なストロークを確保。X軸とY軸の送りにはラックアンドピニオン機構の採用で、ロングストロークを可能にし高速搬送・高加減速にも対応する。
「これ1台で穴あけやタップ加工だけでなく、カッタやエンドミルを用いたフライス加工まで行えるので、生産性の向上と設備投資費の抑制をまとめて実現する」(同社)
今後さらに拡大するEV向け加工機需要を確実にものにしようと、機械メーカー同士の協業も始まっている。MECT初日に展示会場付近で会見を開いたのはエンシュウとドイツのSchwabische Werkzeugmaschinen GmbH(SW社、グループで社員約1600人)。
シングルスピンドルに比べサイクルタイムを最大60%減らせるとするSW社の4スピンドル機
立・横形のシングルスピンドルの小型MCメーカーであるエンシュウと、2~4本のスピンドルをもつ横形大型MCメーカーのSW社が協業することで、「大きな変革期を迎えている自動車業界のお客様の要望に幅広く応えられる」(エンシュウ・鈴木敦士社長COO)と言う。
両社には四半世紀にわたり自動車部品加工向けに特化してきた共通点がある。SW社製MCの日本での納入実績はまだなく、協業によりまずはSW製機の日本での据付、サービス、パーツの供給をエンシュウが担うという。
素材価格の高騰や人手不足により、直近の需要が増加している鋼材加工。ヤマザキマザックは15kW発振器を搭載した高出力の二次元ファイバレーザ加工機「OPTIPLEX 3015 NEO」と、立形MC「VCN-460」を向かい合わせに展示した。
立形MC「VCN-460」と協働ロボットセル
「鋼材価格の高騰により、受託加工業でも鋼材の切断を内製化するために高価な二次元ファイバレーザ加工機を導入頂く例が増えてきている。切断した鋼材の二次加工には立形MCが使われるため、セットで展示している」という。
会場ではOPTIPLEX 3015 NEOで切断したワークをAGVでVCN-460のもとへ搬送し、ワークの搬入や完成品の取り出しを協働ロボットセルで自動化するというイメージの展示を行った。
「金属3Dプリンタで出力したワークの後加工」という珍しい切り口の展示を行ったのは津田駒工業。円テーブルやバイスのイメージが強い同社が今展で披露したのは、独自開発した小型加工機「MDP-0002」。本格普及が期待される積層造形の二次加工(穴あけや面加工)にターゲットを定め、従来の工作機械ユーザーとは異なる層の新規開拓を目指す。
MDP-0002は100V電源で稼働できる手軽さと約1㍍四方に収まる省スペース性が特長。駆動音も無負荷運転時に約50dBと静かで、極端な話オフィスにも置ける仕様ながら、主軸は最高毎分3万回転と本格的な加工能力を持つ。樹脂やアルミはもちろんSUSや耐熱合金の加工も可能。切削精度についても担当者は自信を見せる。
同機種が狙うのは、3Dプリンタで初めて加工の領域に足を踏み入れるユーザーだ。工作機械の知識を持たないことが想定されるが、津田駒工業が刃具選定や加工条件の設定などをサポートすることでスムーズな立ち上げを可能にする。
津田駒工業のMDP-0002
加工前後の3Dモデルからプログラム作成ができるなど操作も簡単。担当者は「従来の工作機械と喧嘩しない機械。大学などの研究機関や試作開発で需要があるのではないか」と期待する。すでにレーザ積層後の加工用途で実績もあるという。
脱炭素・省エネ提案
生産性向上と消費電力量削減の両立提案
自動車業界を中心に脱炭素化の要求が高まりを見せているようだ。このニーズに対し、各メーカーは生産効率を向上させることで、部品単位でのCO2排出量・電気使用量を減らす動きを活発化させている。加えて、アルミや樹脂など従来よりも加工負荷がかかりにくい素材が増えていることから、高付加価値ではなくジャストフィットな製品づくりも目立った。
SPEEDIOシリーズが10周年を迎えたブラザー工業は、40番機より省エネ性能が高い 30番のマシンを並べ、各機で切粉を派手に飛ばしながらビビらない加工性能を提案。同社の担当者は「40番機からの置き換えで従来比 80%消費電力を削減した例もある」と話す。機電一体の開発にも取り組む同社は制御技術によって同時5軸制御MC「U500Xd1-5AX」の工具交換時間をツールtoツールで0.7秒(28本マガジン)に短縮。非加工時間と消費電力を削減する。こうした時間・資源・エネルギー・設置スペースの無駄を削ぐことで環境負荷低減に貢献するSPEEDIOシリーズの技術を同社は新たに「Blue Technology」と命名。専用サイトを立ち上げ、WEB とリアル展の両面でPRした。
ブラザー工業初の横形MC「H550Xd1」
以前からサーモフレンドリーコンセプトを掲げ、高い省エネ性と生産性を両立してきたオークマは新世代のCNC「OSP-P500」を提案。これまで蓄積したノウハウを発展させ、加工による電気代の使用量やCO2排出量を可視化した。OSP-P500を搭載した立形MC「MB-46VⅡ」は従来機種に比べ生産性を16%向上するとともに、消費電力を15%削減できる。
高松機械工業は2スピンドル2タレットCNC旋盤「XWT-8」を展示会初出展。標準搭載の高速ガントリーによる生産性と省エネ性能を訴えた。平行2軸旋盤は一般に主軸のある機械の中心部に熱が集まりやすい。従来機は冷却水を循環させて対策していたが、XWT-8は空冷構造を用いた独自の熱変異補正システム「サーモニー」(特許出願済)を採用。温度が上がりにくい床付近の空気を取り込んで熱交換を行うことで、ポンプなしでも従来通りの冷却効果を発揮しつつ、アイドル時の消費電力を従来機比13・2%減らした。
■洗浄機や電磁弁も脱炭素化加速
スギノマシンは需要が高まっているEV部品向けに遠心乾燥機能付き部品洗浄機「JCC-MULTI」を初披露した。部品の一体化が進むe-Axleも十分に洗浄できる広い加工エリア(600×500×400㍉)を確保するともに、自動車業界でニーズが高まっている脱炭素化にも対応。洗浄工程ではワークの回転軸とノズルの駆動軸が同期して動く「スイング狙い撃ち洗浄」によって使用する圧力と流量を最小化することで、従来機種に比べてCO2排出量を75・1%削減。乾燥工程ではエアブローに代わり遠心力を利用して排水することで同じく52.2%削減できる。
スギノマシンの遠心乾燥機能付き部品洗浄機「JCC-MULTI」
ジェイテクト・グループのジェイテクトフルードパワーシステムは次世代電磁弁「HD1Eシリーズ 超低電力電磁切換弁」を初披露した。従来、油圧ユニットに搭載する電磁弁は、磁気回路を形成するソレノイドの部品間の隙間から電力損失が生じていた。磁場解析技術を活用して磁気回路の構成を見直すことで、消費電力を従来比で30%削減した。最高使用圧力は10MPa、最大流量は毎分4㍑。既設の電磁弁と取付や配線に互換性があるため、交換対応も簡単に行える。
AI・デジタル活用
人手不足で「非熟練化」に期待感
デジタル技術を活用した提案は今展でも活発だったが、「DX」のワードを耳する機会は以前よりやや減ったように感じた。各社の提案はここにきて、より具体的な製品・サービスとして実を結びつつある。一方、注目を浴びるAIをうまく活用した例も随所に見られた。
デジタル技術とAIで40年来の課題に答えを出したのはナガセインテグレックスだ。同社は「約40年前から同じ機械・砥石・ドレッサ・加工条件でもサブミクロン領域では加工結果が微妙にずれることが分かっていた」と言うが、当時は砥石表面を観察する術がなかった。しかしPCやカメラの進化により、今年3月に砥石の表面を見える化する「GRIDE EYE」を発売した。
砥石表面の微細な砥粒を観察するナガセインテグレックスの「GRIDE EYE」
砥石の表面をリアルタイムで定点観察することで、目詰まりを察知して加工不良を防げる。また再ドレスのタイミングはこれまで経験に頼っていたが、加工前後の砥石表面の画像と加工結果をもとに適切なドレスタイミングを導くことも可能だ。「加工前後の砥石表面の変化と加工結果を紐づけ、AIによる画像処理を行えば天気予報のように加工不良の起こりうる確率を予想することも考えられる」(同社)。治具を使えば平面研削盤以外の研削盤にも搭載できるという。
自動車部品大手・武蔵精密工業を親会社に持つMusashi AIは山善ブース内に出展。加工中に発生したギア歯面のキズ・打痕・研磨残りをAIを使って外観検査する装置を出品した。撮像データを蓄積し、アノテーション(意味づけした教師データの作成)を行い独自のアルゴリズムをつくる。「わずか数秒で0.3㍉の極小キズももれなく検出する」と言う。大手が手掛ける閾値を設定する方式は検査環境によって判定が難しくなる。AGVも製造するMusashi AIは、このAI外観検査装置を社内向けで使った後、外販することにした。トヨタ自動車に12台納入したほか、医療・食品業界向けで引合いがあるという。
オークマは新世代のCNC「OSP-P500」の利便性を訴求。「製造業の一番の課題は人手不足。初めて使う作業者もプログラムを作れることをコンセプトにした。対話式のガイドよりわかりやすく、スマホのタッチパネルのように作業できる」とする。一方、ガイドで作ったプログラムをGMコードに変換することも可能で、「生産性の高いプログラムを切り取って利用するなど、ユーザーの経験や知見で加工時間を短くできる」と効率化につなげる。
新素材・難加工材
航空産業復活で提案増加 半導体むけ脆弱材も
航空産業向けの難素材へのソリューションが多く見られたほか石英ガラスやセラミック、樹脂材などの脆性材も半導体・電子等の部品加工で増加。EVではモーターやバッテリーケースなどでアルミの使用が上がっており、「アルミの高速加工」を巡る技術競争が再燃していた。
「航空機の翼部分はもとより、EVシフトでさらにCFRPの加工ニーズが増加する可能性もあります」という平安コーポレーションは、CFRPなど新素材の加工ニーズに応える立形5軸マシニングセンタ「NC-131MC-1310T」を出品した。
平安コーポレーションの立形MC「NC-131MC-1310T」
「主軸を太くすることで剛性をもたせ、難削材も加工できます。木工加工から派生した弊社は吸着装置による材料固定を得意としています。材料の設置もカンタンに行え、加工しやすいといったメリットがあります。また、主軸部に集塵ブラシがついており切削粉をすぐに吸引。切削したそばから吸い上げる集塵ブラシは炭素繊維がどこかに入り込むことがなく安全性が高いです」(担当者)と説明した。
小径工具が広がるなか、対応する研削盤も登場した。牧野フライス精機が初披露した小径工具研削盤「DB1」は工具径0.03~4㍉を対象とする。同社として初めてリニアモーター駆動を採用。標準搭載の自動ワーク交換装置は最大520本(工具径3㍉の場合)のワークを収納でき、長時間の連続加工に対応する。小径エンドミルは超硬合金への鏡面仕上げやセラミックス、炭化珪素、石英ガラスなどへの高精度加工向け。同社は径0・03㍉工具を研削して見せた。
■治具にも新素材使用の動き
工具では住友電気工業が航空産業向け難削材高性能仕上げ加工用「スミボロンバインダレスエンドミル」を参考出品。インコネルやワスパロイなどを用いたエンジンのブレードの仕上げ加工などに対応。通常の超硬エンドミルに比べ、数倍の加工能率を実現した。軟質な結合材を一切なくした(バインダレス)CBN焼結体を刃先に使うことで高い耐摩耗性を実現した。
住友電気工業「スミボロンバインダレスエンドミル」(難削材高性能仕上げ加工用)
髪の毛幅に文字を入れるといった極小径工具で第一人者の日進工具は、径12㍉までの「そこそこ」太いアルミ加工用エンドミルを拡充して展示した。「(小径工具メーカーとして)径6㍉まででいいと思っていたが、ニーズがあるので作っています」とは同社の後藤弘治社長。長時間安定して高能率加工ができることをアピールした。
治具にも新素材の活用が広がる。東亜精機工業は特殊材料「フェルカーボ」を使用した治具を提案した。双葉電子工業が開発し、フェルト状の炭素繊維を用いた「フェルカーボ」はアルミの半分の重量で、熱膨張係数は鉄の半分程度となる。また引張強度はアルミ合金の1.3倍と優れる。
東亜精機工業「フェルカーボ」を使用した治具
「体の小さい女性が治具をセットするということも多く、重いと非常に大きな負担になっています。働く人の負担軽減が重要になっています」(担当者)と話していた。
MECT×新製品・注目製品
多軸旋盤から新型タップまで
ここまでは主に、MECT2023で披露された製品・技術を脱炭素や自動化といった大きな潮流に沿って紹介してきた。とはいえ今展ではその枠に収まらないユニークな展示も多く、実際にそれらが会場を賑わせていた。面取り加工機に多軸旋盤、歯車加工機、汎用旋盤、転造タップ、円テーブルや高圧クーラント装置まで。ここからは記者が取材した各ブースの見どころを、テーマにとらわれず振り返っていく。
工作機械
「時代がようやく追いついてきた」。武田機械の担当者はそう語り、初出品の面取り加工機「CFR310」をアピールした。切断したプレートの12辺すべてをワンチャックで自動面取りできる機械で、310×310×150㍉までの6面体に対応。面取り量も設定可能で、手作業より仕上がりのバラつきを抑えられる新製品だ。
実は同社は約10年前に500㍉角プレート対応の自動面取り機を発売している。しかし面取りはサービスの一環という認識が浸透しており、「専用の加工機を導入しようとするユーザーはほぼいなかった」(同社)そうだ。しかし近年はプレートにも見た目や面粗度など高い品質が求められつつある。「満を持してより小型のCFR310を開発した。時代に合う製品だと考えている」とする。
武田機械の面取り加工機「CFR310」は12辺すべてをワンチャックで自動面取りできる
嶋田鉄工所から社名変更したシマダマシンツールもユニークな製品を展示した。2主軸旋盤のフラッグシップ機と位置付ける、1タレットNC旋盤「2SI-8 Mk-Ⅱ」だ。もともと6主軸や8主軸の多軸旋盤を主力としていた同社は、近年は2主軸・4主軸の旋盤にも注力する。2SI-8 Mk-Ⅱもその流れを汲むもので「高能率という多軸旋盤の特長を残しつつ、Y軸付与やモータ内蔵主軸の採用などで一般的なNC旋盤の使い勝手を狙って開発した」という。
同機の2つの主軸はドラムと呼ばれる1つのテーブル上にあり、このドラムが回転することで加工室の内外を行き来する構造。加工中に片側の主軸でワーク着脱が可能なため「一般的なNC旋盤では着脱に7~10秒かかるが2SI-8 Mk-Ⅱは1.5~2秒しかかからない。能率はかなり高いと思う」と胸を張る。機上搭載型のロボット(オプション)が一方の主軸の加工中に計測やエアブローを行うなど自由に他の作業も並行できる。「他社と一線を画した構造と自負している。我々の多軸旋盤は1秒でもサイクルタイムを縮めたい量産ユーザーがメインだったが、それ以外のすべての旋盤ユーザーも2SI-8 Mk-Ⅱの恩恵を受けてほしい」
シマダマシンツールの「2SI-8 Mk-Ⅱ」は、多軸旋盤の生産性とNC旋盤の使い勝手の両立を目指した
内面研削盤における「国内トップクラスのシェア」(同社)を持つトーヨーエイテックは、リニューアルした横形内面研削盤「THG-10CA」の優位性を訴求した。主軸とドレスで冷却系統を個別化し、熱変位を抑制。フルクローズド制御も取り入れ「1日の経時寸法変化をテストワークで2㍈に抑えた」と精度と安定性に自信を見せる。今展では協働ロボットによる機外での自動段替えデモを見せたが、「今後はチャックの爪交換まで自動化し、24時間の無人加工を目指したい」と意欲的だ。
トーヨーエイテックは歯車研削の自動化ラインを提案。同一メーカーでラインを組むことによる高い保守性を訴える
一方で研削盤を手広く手掛ける同社ならではの提案も行った。歯車研削盤「TGG―26―2W」と立形複合研削盤をロボットで接続するイメージのモックアップ展示だ。複合研削盤で歯車の内・端面の基準を出し、そのまま歯面研削を行うことで歯車を高精度に仕上げる。「もちろん精度は高いがそれはある意味あたり前。TGG-26―2Wは2つのワークヘッドを持つため加工中に段替えができ、複合研削盤と合わせて導入いただければ保守性も高まる。このようにいかに人の手を減らすかを重視している」とする。
第1展示館にひときわ目を引くデザインの汎用旋盤があり、思わずブースに吸い寄せられた。「21世紀の汎用旋盤」をテーマにサイダ・UMSが開発した「VERSEC-neo」だ。造形作家・鯱丸邦生氏とのコラボで生まれたもので、重厚かつメカニカルな外観には「色気」とも言うべき独特の雰囲気がある。「デザインだけでなく操作性も画期的」(同社)といい、「インターロックによりチャックハンドルを付けたままでは主軸が動かせない機能や、主軸の回転中も加工条件を変更できる機能などを持たせた。熟練者も違和感なく使える一方で、教育用途にも向く」と言う。
造形作家とのコラボで誕生したサイダ・UMSの汎用旋盤「VERSEC-neo」
工具・周辺機器
切削工具では既存概念から離れ、刃先形状を独創的に変えることでソリューションにつなげる例が見られた。いわゆる「異形工具」が近年、市場に定着しだしたなか、工具の静かな変化が加工の高度化を促していた。
「3年間を丸々開発にかけた、その成果です」。胸を張ったのは不二越・工具事業部の干場俊洋技術部部長。出品物の目玉は今年12月21日発売のバリレス工具シリーズ(エンドミル、ドリル、タップ)だった。バリは従来の10分の1~ゼロにできるという。記者がバリレス工具は一部他社からも出ているが、と問うと「他社製品をネガティブに批判したくはないけど、レベルが違います」と自信たっぷりの回答。刃先の滑らかなコーナーRで切削抵抗を最小化する一方、シャープなエッジで貫通時のバリを切り捨てる(ドリルの場合)などしてバリを無くした。全社を挙げてPRするという。
日進工具はヘッドアップディスプレイなどの緩斜面を仕上げるエンドミルの新製品(12月発売予定)を出品した。最大のポイントは底刃が、レンズのように外側に向かって丸みを帯びながら横へワイドに広がる形状としたことだ。これにより曲面精密加工の能率を上げた。
新たな転造タップ「GREEN TAP」で新風を吹き込むのはオーエスジーだ。新製法で製造時のCO2排出量を約50%削減。クーラントのための油溝をなくし、材料力学でねじれに一番強いとされる真円を採用したことで従来製品よりも摩耗を抑制しつつ耐久性を高めた。
同社によると「ねじ山の角度はJIS規定で60度と定まっており、タップの角度も60度でなければならないのが、いわばこれまでの工具業界の常識だった」という。しかし研削砥石を使わない新たな製法を開発したことで、タップ形状を自由に作れるように。つまりGREEN TAPには60度のねじ山はないが、同タップで作るめねじのねじ山は60度になる。「従来の油溝をなくしたが、最も冷やすべきは刃先。従来形状だと油溝があっても刃先が邪魔だが、GREEN TAPは『刃先から山がすとんとおりたような形状』で効率的に冷却できる。コンピュータのシミュレーションが導き出したタップの理想形状。」と力を込める。
オーエスジーの「GREEN TAP」は環境性能と耐久性を強化した
北川鉄工所は小型・軽量で30番MCへ搭載できるNC円テーブル「RKT500」を出品。最大ワークφ500で、「バッテリーケースなどEV向け大型アルミワークに対応できる。ローラギヤカム機構方式でギヤ特有のズレやバックラッシがなく、傾斜の割出し速度も向上。加工時間短縮につながる」と紹介した。メンテナンスフリーで保守性にも優れる。「今年発売したばかりだが国内だけでなく海外からの引き合いも強い」と好調な滑り出しだ。
北川鉄工所の「RKT500」はバッテリーケースなど大型のアルミワークにも対応する
産業機械などの位置決め検出用のエンコーダを手掛けるマグネスケールは、工作機械の円テーブルや直動部品の状態診断や補正を機上で行えるエンコーダとアプリケーションによるシステムを提案。予知保全や計画保全の最適化、取付偏心のキャンセルに寄与し、メンテナンスや段取り替えに対する省力化ニーズの取り込みを狙う。円テーブルの精度を向上する「SICs(Signal Intensity Conversion System)」は、テーブルに取り付けた状態でも自己角度補正できるため、テーブルの乗せ換えなく精度を担保できる。エンコーダからの信号状態をCNC上でモニタリングできるリニアエンコーダ「ODF(Online Diagnostic Function System)」は、NC装置上で異常を検知し、急な機械のマシンダウンを未然に防ぐことが可能だ。現在は、シーメンス製のNC装置のみに対応するが、「MECTでの反応を見て今後は国内メーカーのNC装置にも対応していきたい」と話す。
ホーコスのブースには初出品の「チップイーター CE100」があった。金属加工時に発生する切りくずを自動で圧縮・ブリケット(固形)化するもので、従来より処理量を増やした大処理タイプだ。「従来機は1時間に18~20㌔(アルミ切りくずの場合)の処理量だが、1時間100㌔と処理量を5倍に増やした。大処理タイプには海外製が多いが、国内メーカーとして勝負する」(同社)
「刃先が熱で摩耗し効率が落ちる」「切屑が絡みワークが傷つく」「チョコ停が頻回し補正作業に追われる」。これら切削加工の課題を、トクピ製作所は高圧クーラント装置「HIPRECO」で解決しようとする。「クーラント液を高圧で刃物に直接当て、刃先の冷却効果を高めることにより刃物寿命を延ばせる。切りくずの分断は自動化・省人化にもつながる」と話す。特に1平方㍍の省スペースタイプのニーズが高まっており、「省スペースながら機能が集約しており、ユーザーに好評。自動車向けはEVシフトの様子見で工作機械の買い控えもあるが、後付け需要が増えている」とする。
(2023年11月10日号掲載)