オンライン座談会:日欧中のロボット技術とユーザーメリット
- 投稿日時
- 2024/03/22 10:01
- 更新日時
- 2024/03/22 10:47
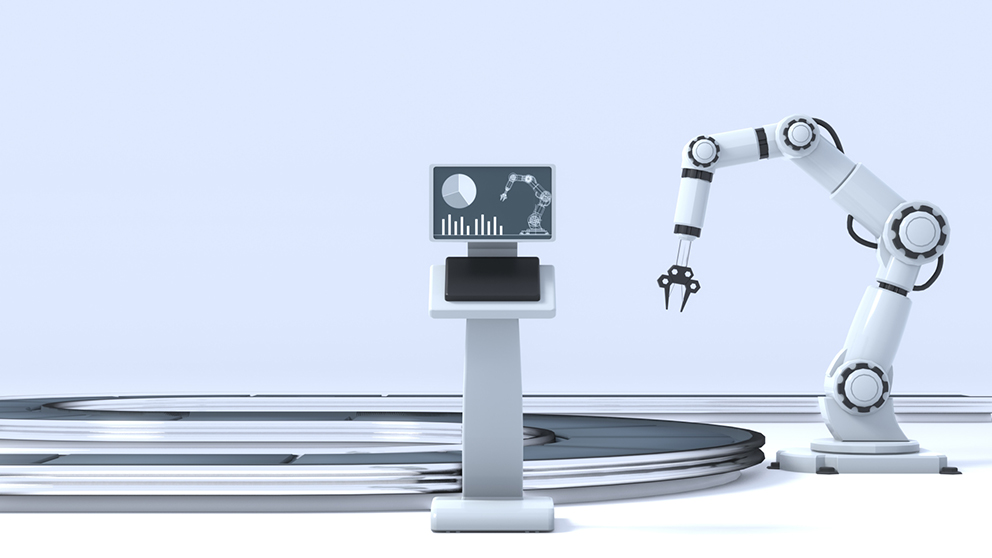
少子高齢化に伴う人手不足、なかなか改善しない労働生産性――。その解決に有力とされているのがロボット利用だ。技術は飛躍し扱いやすくなってきた。欧州やアジアのロボットメーカーが日本市場に参入し、競い合うかたちでこの動きはますます加速している。最近の実情やメーカーによる違い、導入メリットなどを探るべく、日欧中を代表するロボットメーカー、SIer、ユーザーにオンラインで集まってもらった。
自動車分野を軸に新領域開拓
建築、ラボ、教育、食品、化粧品分野も
――まずは各社さんが得意とする商材・産業分野や納入実績などをお話いただけますでしょうか。
岡久学(安川電機) 当社が得意とする製品は サーボモーター、インバーターといったドライブモーションや、私が所属する産業用ロボットです。社会システム向けのモーターが原点で、その応用を会社の社風としながら進め、今は産業用ロボットを中心にしながら世の中の工場の自動化への浸透を図っているところです。ロボットの納入実績は累積60万台を超えたところ。主力とする分野の半分は自動車産業で、足回りのアーク溶接、ボディーのスポット溶接、ボディーの塗装などが得意です。これらが産業用ロボットの3大アプリケーションです。昨今は少子高齢化からくる人手不足、労働力不足が社会課題になって一般産業需要も増えています。自動車産業はなくならないとは思いますが、そこでの進化と新たな領域を広げていくのが我々の方向性です。
浅利貴(ABB) 我々も得意とする商材は1つは自動車分野向けのマニピュレーターがあります。それ以外に協働ロボットの「YuMi」の利用も広がっています。一方で、ラボオートメーションという言い方もしていますが、研究室を自動化していこうという動きがあり、たとえば研究所や病院での薬品の照合など高度な技術を必要としない作業はロボットに任せようという取組みです。あと、建設業界の3Dプリンティングや教育の分野に新しく取り組もうとしています。が、それらが自動車という大きな産業をリプレースできるかというと当然そうではないのですが。
ABBの新しい6軸協働ロボット「GoFa」(可搬重量5kg、クラス最高レベルのモーションコントロールとGoFaのインテリジェントなトルクおよび位置センサーの組み合わせが特長)
易峰(DOBOT JAPAN) 我々は2015年、深圳で設立したスタートアップ企業です。協働ロボットの開発と生産のみに特化し、今のところ産業用ロボットを扱う計画はありません。従業員数は約650人、そのうち4割が技術担当です。4軸、6軸制御やスカラタイプを含め6種類の協働ロボットを生産し、軽量化しているため得意分野は半導体関係や エレクトロニクス、物流です。日本ではやはり自動車業界からの引き合いが年々増えています。出荷量は6割を占める教育分野を中心に2023年までの累計で7万5千台です。中国国内の協働ロボットメーカーの中で1番多いです。浜松町に事務所をもち、4月に名古屋オフィスも立ち上げます。中国の山東省にマザー工場をもち、フル稼働すれば年間10万台の生産能力があります。
瀬川裕史(スターテクノ) 我々の特徴は自動化の構想から機械設計、電気設計、部品製造、組立、ティーチングとすべてに専門部隊がいて、ほぼ内製しています。グループ会社に、射出成形機の上でハンドリングする直交座標型ロボットを製造するスター精機があり、昨今、この技術を活用して物流分野のパレタイズや工作機械のガントリー、それに軸単体での販売と新分野への展開もしています。そうは言っても我々1社でできることは限られるので、企業間の連携でビジネスが広がっています。最近はデジタルツインにも力を入れ、3Dの設計はもちろん、バーチャルでのモノづくり、検証も進めています。得意分野はやはり地域柄、自動車が圧倒的に多いです。で、どちらかというと柔らかいものを扱うのが得意で、自動車の中でもプラスチックやカーボンの新素材、こちらは航空機分野でも一部ありますが、これらの2次加工などの仕事を多く手がけています。
――自動車分野の中で切削加工も手がけられています。
瀬川 ロボット切削は難しいものもありますが、我々は小さな2軸の加工機をアームに搭載して加工しています。
田中陽一郎(フレアオリジナル) 当社は長野県にあり、私が27歳の時に 個人事業主として始めました。その後法人化して16年目になります。SIerとしてロボットを使った自動化設備を中心に取り扱い、ロボットの可搬質量は3㌔から200㌔グラムです。けっこう新しいもの好きで、2D、3Dのビジョンなどを使います。納入実績で多いのはパレタイジングなどの搬送系。アームにカメラを持たせたり、カメラのところに ワークを持っていっての検査だったり。組み立て、ねじ締め、溶接などの実績もあります。自動車部品分野の仕事が多く、樹脂、化粧品、食品なども扱います。設計は3Dで行い、VRを使っての提案もしています。
――扱うロボットは 日本製から中国製と多岐に渡り、DOBOTさんも好んでお使いとか。
田中 そうですね。まだ扱いのないABBさんも今度使ってみたいと思います。
長田展幸(SUS) 当社がメインで扱っている商材はアルミフレームです。鉄などに比べて押出し加工性が非常に優れており、複雑な断面を作れますので、アルミプロファイルとも呼ばれています。アルミ押出し機を2台保有しています。日本国内にアルミプロファイルを扱うメーカーさんはほかにもありますが、押出し機を持つのは当社だけで、低コスト、短納期はもちろん、他社では作れないような複雑な断面形状を製作することができます。大きく分けて四角いフレームと丸いフレームがあり、主な納入先は四角いフレームは半導体メーカーさんの装置などの機械装置の構造材として使われることが多く、丸いフレームは自動車関係の工場などの生産改善活動で使われることが多いです。
溶接・塗装から組立ニーズが増加
でも部品構造を変えないと……
――近年需要の高まる自動化アプリケーションとその背景、導入効果について教えてください。
岡久 自動車業界では溶接、塗装の自動化は当然ながらロボットなしでは語れないくらい浸透しています。導入効果よりも、もう自動化するのが当たり前の領域です。近年は人手不足、人件費の高騰を受けての自動化需要が多いので、組立や搬送に広がってきています。人が集められないところでは省人化は大きな効果があるでしょうし、一方で現場のDX化や生産性・品質向上を課題にしている企業にとっては、 自動化でデジタルデータが取れることになるので、それも1つの効果として捉えていただいています。
――最近増えてきた使い方はありますか。
岡久 組立は増えてきました。自動車業界が牽引するような形で広がっています。季節工的に人を集めていたところはもうかなりのお金を積まないと人が来ないようですし、やはり自動化ニーズは 着実に増えてきていると実感しています。
――以前は切削加工を自動化しようとすれば欧州ロボット特有の剛性が必要とされましたが、最近では安川電機さんをはじめ日本製ロボットにも剛性の高い機種が登場しています。
岡久 どこまでの剛性が必要なのかは用途によって違うと思いますが、 バネ定数を変える、センサー使って制御を入れるなどロボット自体の仕組みを変えるということですね。単純にモノを大きくして高剛性にするという話ではないと思います。
浅利 岡久さんがおっしゃった、自動車分野の組立仕事の増加は私も感じていました。上流のところはすでに自動化されソリューションも固まっていることもあって、比較的日本に当てはまるのでしょうけれど、組立は今まで人でやる方が流れ作業で効率が良かったのが、人手不足でニーズが顕在化してきているようです。あと新しいところではEVバッテリーやモーターの組立も自動化しようとする流れはあります。それ以外のところでは、もちろん協働ロボットによるアプリケーションもあります。当社の双腕YuMiは発売して約8年。組立や検査のほか様々なところで知見が得られ、新しいアプリケーションが出てきています。他方で、欧州では通常の産業用ロボットの安全性を確認した上で、たとえば極力柵を使わずに協働ロボットのような使い方にチャレンジされています。産業用ロボットの協働ロボット化です。このように対環境性というような新しいアプリケーションが出てきています。
――従来だと産業用ロボットには柵が必要で人との距離が遠かったのが、だんだん近づいてくるようなイメージですか。
浅利 そうですね。協働ロボットはどうしてもスピードが遅くタクトタイム的に難しい部分がありますが、産業用ロボットでもセンサーで人の出入りを確認して安全を確保して、かつ人がいる位置を見ながら作業スピードを調整できます。我々がやろうとしているダイナミックセーフティーがそれに当たります。これはビジネスチャンスになるでしょうし、お客様にとっては使い勝手の自由度が上がることになります。
易 当社の協働ロボットは可搬3㌔から20㌔グラムまでなので、組立用途といっても携帯電話の基盤や電子部品の組立、あと半導体関係の搬送、ピッキング作業が多いです。最近日本のお客様に納入が増えているのはねじ締め、検査工程。カメラを持たせての外観検査、不良検査です。 当社の方向性としては2つの考え方があり、1つはラインナップを増やすこと。可搬重量を今の20㌔から将来的には30㌔グラム以上の機種も出したい。そうすれば自動車業界で使ってもらいやすい。もう1つは、今年からどんどんチャレンジしているのですが、商業分野での利用。たとえば蕎麦屋さんの麺茹で器や調理器との組み合わせ、ビールサーバーといった用途です。
DOBOTの協働ロボットを紹介する易峰マネージャー
――ねじ締めの実績もあるそうです。締め終わるときにどうしても反力がかかり、ロボットが止まってしまいやすい。どう工夫されていますか。
易 ねじ締めが終わったところで一時的に衝突感知センサーをオフにし、その後オンにするような仕組みがあります。協働ロボットでのねじ締めは基本的に大きいねじやボルトでなく、M3やM4、大きくてもM6までなので、それほど大きな反力は働きません。
瀬川 岡久さん、浅利さんがおっしゃった組立のニーズはすごくあり、昨年当社では手組みラインのロボット化を実施したのですが、次々予定していた仕事が途中で終わってしまいました。やはり難しいですね。人間のように器用に進められない。また専用機でないので、そこにロボットを入れて汎用的に動かすことがどうしても難しい。我々の力のなさを感じました。自動車業界にはある程度ロボット導入が行き届いてしまっているので、 次のステップに行こうとすると非常にハードルの高い要求をされます。
――とりわけ難しい要求とは。
瀬川 ひと言で言えば、ワークは手組みを前提に設計されており、自動化ができるような設計になっていません。これは自動車メーカーさんもわかっているはずなのですが。今後ロボットを使っていくとするなら、部品の構造を変えないとうまくいかないと思います。なかなかすんなりいかないっていうのが1つありますね。一方で我々がやっている樹脂の加工などはかなりロボット化が進んでいます。従来は我々が専用機を作っていましたが、そのロボット化をすることによって汎用的に使えるようになったものがかなりあり、多くの自動車メーカーさんに採用いただいています。新分野では、先ほど浅利さんがおっしゃった建築業界の3Dプリンティングは当社も実施しています。皆さんおっしゃるとおり、人手不足はもう全ての業界共通で、ロボット導入が非常に注目されています。県レベルでも新分野でのロボット導入の検討会が盛んに行われています。
田中 協働ロボットの代理店を始めたこともあって、その引合いが多いです。が、協働ロボットは産業用ロボットと違い、量産用途というより補助的な使い方が多い。人を1人でなく0.5人削減するような形です。ただ、瀬川さんがおっしゃったように自動化するにはけっこう難易度が高い。人だったら簡単に組み立てられる作業でも。結局、そういうところの自動化が残っています。当社も社内で実験して新しい用途を開発したりはしているのですが。最近では先ほど易さんが話されたねじ締めについてM12(40N)をDOBOTさんの協働ロボットにナットランナーのようなものを持たせて反力を逃すことでほぼ確立しています。あと配線のコネクターの取り扱いニーズもあります。コネクターは形状が安定せず運んでいる最中に形が変わってしまうので最初にビジョンで見ただけでは補正しきれません。そんな難易度の高い自動化が残っていて、それを克服していかねばと感じています。
――形がどんどん変わってしまう配線コネクターはどう扱いますか。
田中 カメラで常に追い続けます。通常の撮像をしてそれを補正して……というやり方ではロボットが目をつぶっているのと同じ状態ですから。
長田 当社は静岡事業所にABBさんの双腕ロボット「YuMi」を5台導入し、生産性が2割アップしました。ボルトを置いてナットを締める作業は当社で作った自動機で行いますが、そこにセットする人が必要でした。そこを双腕ロボットとパーツフィーダーに置き換えました。月に70万個ほどつくる工程でうまくはまり、2年間での投資回収のめども立っています。
SUSの静岡事業所で働くABBの双腕協働ロボット「YuMi」
日欧中の違いでなく、会社の独自性
ウリは品揃え、タクトタイム、教示しやすさ
――日欧中のロボットの違いについて長所・短所ふくめてお聞きしたいと思います。大いに技術自慢をしてください。
岡久 技術自慢ということで話をしますと、安川電機のロボットは非常に多岐に渡ります。歴史もそうなのですが、先ほどの話にもあったように自動車向け溶接・塗装、液晶ハンドリング、半導体のロボットも展開していますし、ABBさんと同様に双腕ロボットなど様々なバリエーションがあることが当社の特徴だと思います。日欧中のロボットという見方ではなくて、当社ロボットは多様なお客様のところに入り込んでいます。お客様からの依頼で特殊な用途にあわせて一緒に開発したものもあれば、うまくいかなかったことや試作で終わったものもあります。何が言いたいかというと、モノを作って売るというよりも、お客様のどんな課題が当社のマニピュレーションで解決できるのかを考えながら歩んできたということです。これからもそのスタンスで続けていきたいと思います。昨年末には国際ロボット展で「MOTOMAN NEXT」を出品しました。従来のプログラムを書いてシーケンス通りにロボットを動かすという考え方から、不確定で形が異なるワークをカメラやセンサーで見て、どう判断をしたらいいのかをロボットコントローラー内蔵のAIが判断できる業界初のロボットです。自律性を高めたロボットという表現をしています。バラ積みされたワークをカメラで見て取るといったアプリケーションもありますが、我々が目指すのはお客様の作業の完結です。先ほど組立領域は難しいという話がありましたが、これにはいろんな要素が絡み合いシーケンス通りにいかないからだと思います。用途展開はこれからですが、それにはエンジニアリングが必要になり、当社のチャレンジになります。
安川電機の「MOTOMAN NEXT」による下膳作業
浅利 私も長所、短所を国・地域で分けるのは非常に難しいと思います。一般的に当社の長所として言わせてもらっていることは、軌跡精度の高さやサイクルタイムの短さ、加減速の速さ、高スピードです。日本のマーケットでは安川電機さんに比べると我々はまだまだ小さな存在です。ただ、大手さんにできない仕事が当社に流れてくることがあり、それを実現していくのが我々の付加価値になります。
――日本のロボットメーカーにできず、ABBさんにできるのはどんな作業ですか。
浅利 タクトタイムが1番わかりやすいかもしれません。それには加減速の速さなどが関わってきます。あるレベルまで一気に上がり、あるレベルまで一気に下がる。最高速が出る時間が一定時間の中で長いことはタクトが短くなることとイコールです。引いてはロボット台数が他社さんよりも少なくて済み、イニシャルもオペレーションにかかる費用も抑えられます。
易 中国企業のDOBOTは国内の競合メーカーと比べて大きな長所を打ち出しにくい。ただ、安全性や使いやすさについては中国系の協働ロボットと比べると少しだけ特長が出てくるかと思います。日本市場では当社は海外メーカーなのでお客様は「実績の多い安川電機さん、ABBさんと同等の製品を提供してください」と要望されます。コストパフォーマンスが高いという前提があり、その上で大手さんと同じ性能を求められます。当社は設立から8年で、同時期にできた中国メーカーさんが多い。その8年の経験で得たフィードバックを使って、かなり進化したと思います。ただ、日本の大手さんに比べるとまだ少し距離があると認識しており、どんどん追いかけていこうとしています。会社的にもかなり投資し、特に研究開発の投資には力を入れています。
――中国からのロボット輸出量ランキングでDOBOTさんは5年連続で首位とのことです。この大きな理由は何だと考えますか。
易 会社設立の翌年、2016年からすでに海外展開に力を注いできました。他のロボットメーカーさんはやはりまずは国内である程度の市場シェアを握ってから海外に目を向ける作戦ですが、DOBOTは逆パターンです。
――協働ロボットで日本の大手とまだ差があるとおっしゃいました。どのあたりが足りないと思われますか。
易 やはり安定性でしょうか。たとえば振動したり絶対精度が少し足りていなかったりです。
――SIerさんは日欧中のロボットを実際に扱われ、違いを感じていらっしゃるのでは。
瀬川 当社のラボにABBさんと安川電機さんの大型の可搬200㌔グラム近いロボットをお借りしてテストに使わせていただいています。日本と欧州というよりも、会社の違いがあるような気がします。たとえばABBさんは非常にアプリケーションが充実しており、先ほどの3Dプリンティングなどもそうですが、ある目的を遂行するための機能をソフトウェアを含めて提供していただける。そこにノウハウも含まれるのが特徴で、やはり目的にミートしたものだとシステムを非常に早く完成させられます。先ほどのタクトの話もそうで、非常に多くの知見をお持ちです。一方、安川電機さんの場合、非常に製品ラインナップが充実しており、国内の自動車メーカーおよび自動車部品メーカーさんから圧倒的な支持があり、常に指定が入るほどで、我々としてもカバーできない範囲がないというところです。中国ロボットについては、DOBOTさんもそうですが、とにかく開発のスピード感、成長のスピード感が早い。展示会などで少し触らせてもらうと、プログラミングが非常に優しくティーチングしやすい。子どもでもできるのではないかと思うほど、よく考えてあります。ここは日本のメーカーにも見習ってほしいと思います。
易 ありがとうございます。我々はどうすればお客様が簡単に使えるのかを考え、ソフトの設計の段階からよく検討して作っています。
田中 DOBOTさんのティーチングのしやすさは、やはり教育用のロボットを作っていらっしゃることが大きいのかもしれませんね。簡単に作れるプログラムだけでなく、ルア言語というテキストベースのプログラムでも組めるようになっています。けっこう凝ったことをするには言語で組んだ方がやりやすいこともあります。作ったプログラムをブロック化することもできて、そのブロックを組み合わせてとけっこう考えられているという印象を持っています。
――フレアオリジナルさんでは中国製ロボットとしてはDOBOTさんのみを取り扱っていらっしゃいますか。
田中 取扱代理店をしているのはDOBOTさんですが、ほかに台湾テックマン・ロボットさんもコストパフォーマンスの高い協働ロボットということで扱っています。先ほど振動の話が出ましたが、当社でもいろいろ検証したところ、多くの協働ロボットで振動はします。海外製だから振動が大きいという印象はもっていません。あとサポートについては、海外メーカーだから十分でないという話も聞きますが、DOBOTさんのサポートは良くて、チャット形式でグループを作りエンジニアと直接やり取りできたりします。日本メーカーとはこのあたりが違いますね。開発スピードが早いのもそこにあるのかもしれません。
フレアオリジナルは事前にシミュレーションをして全体のシステムを細部まで詰める。
――フレアオリジナルさんでは日欧中のロボットをどう使いわけていらっしゃいますか。
田中 産業用途は日本メーカーですね。安川電機さんは休日にもサポートしてもらえるのがすごくありがたいです。協働ロボットは価格が重要になるのでやはりアジア製になりがちです。
――SUSさんではABBさんの双腕以外にもロボットをお使いですか。
長田 YuMiを導入した静岡事業所の鋳造工場に取出しとトリミング用にファナックさんのロボットなどを計10台、そのほか箱詰め用にABBさんのパラレルリンクロボット1台もあります。メーカーさんにより導入の仕方や仕様が違いますが、ABBさんのロボットで良かったことはシミュレーション。導入前にリアルに近い姿を見て検討することができましたから、そのまま置くような形でスムーズに導入することができました。コスト削減もきちんと計算でき、効果としてもすごく見やすい形になりました。
ロボット導入できる段階でない現場も
カイゼン段階では時期尚早?
――最後にロボット業界の課題と企業間協業の可能性についてお聞きします。
岡久 皆さんが話しているようにロボットのポテンシャルはまだまだたくさんあると信じています。そのポテンシャルに対してどのようにアプローチしていくのかが課題になると思います。我々から見るとABBさんもDOBOTさんも競合と言えますが、労働力がまだまだ不足しており、多様化するモノづくりへの対応も必要です。いずれかのメーカーが突破口になり、別のメーカーがその後を追いかけながら、このポテンシャルをどんどん広げていくことがロボット業界では重要だと思います。その時にSIerさんの位置づけは非常に重要になります。我々メーカーにないきめ細かい実用化技術をお持ちですから。そのためにはSIerさんに利益を出していただく必要があります。これができればサステナブルな成長、進化はできると考えます。
浅利 先ほど岡久さんから話がありましたAIについては当社も取り組んでいるところです。ロボットが自立して作業を行うという方向になります。もう1つの課題はどうやってロボットを使いこなすのか。これ次第で大きく広がっていく可能性があります。今までのプログラムを前提にしたものだけでなく、若干アバウトな指示でロボットを動かせることが大事になってきています。あとは今まで使ってこられなかった分野にいかにして導入してもらうか。プログラミングの簡便性もそうですが、使い勝手の良さ、わかりやすさはDOBOTさんのお話がありましたように、大事な視点だと思います。
易 2人の大先輩のお話を聞いて共感しています。1番の課題は我々がどうやって生き残るか、どう成長していくか。先ほどお話がありましたように、AIを使ってロボット自身に判断させて仕事することが将来的にはおそらく可能になると思います。ただ、そこまでいくにはまだ長い道のりがあるとも思います。そこでまずマーケティングの規模を作らないといけない。産業用ロボットには長い歴史がありますが、協働ロボットはこれからです。ですからメーカー各社さんと連携しながら一緒に市場をつくっていきたいです。1つの動きとしては、当社を含め中国メーカーさん数社が手を組んで、新しいアプリケーションの開発などを進めており、またお客様の声を聞いて自社ロボットをどう進化させるかといったプロジェクトも進めています。
瀬川 人口減に対するロボットの重要性はこれからますます増していくので、ぜひともロボットメーカーさんには新しい技術をどんどん深掘りしていただきたい。AI、IoTに関してもどんどん突き進んでいただきたいです。その反面、我々が現場で自動化しようとする時に常々感じているのは、ロボットを入れる以前の段階がたくさんあることです。「前さばき」「地ならし」という言葉を最近よく使うようになったのですが、要はトヨタ流で言うカイゼン、もしくはその手前の段階にある企業が多いのです。その場合、ロボットを入れることが最良の策でないことがたくさんあり、自動化したいとおっしゃるが、その段階でない。自動車産業ではそんなことはあまりありませんが。これを受け来年度から経済産業省が枠組みを作って改善しようとしているようです。全体の効率が上がることによって初めてロボットを導入できる段階になると思います。
スターテクノが開発した段ボール箱組立ロボット
田中 人手不足は我々SIerにもおそらく当てはまり、エンジニアの人材確保と育成は喫緊の課題です。当社ではメンバーみんながメーカー各社のプログラムをトータルで扱えるように進めています。が、無理だと言って辞めてしまう人もいます。
――ご出席者に質問や要望はありますか。
田中 安川電機さんのAIはすごく気になるのでぜひ使わせていただきたいです。ABBさんのロボットは使ったことがないので、ぜひデモ機をお借りしたいです。
岡久 九州に来ていただけたら実機を見ながらお話もできると思います。
浅利 ぜひ一度、具体的なお話をさせていただきたいですね。ウチだけまだ使っていただけていないので(笑)。
長田 当社が最初に採り入れたパラレルリンクロボットは導入しやすいようにパッケージ化されていたのがきっかけです。ロボットおよび周辺機器、コントローラーが付いた形で標準化されていました。ロボットメーカーさんにはそうした標準化も進めてもらいたいと思います。標準化されたものを使えばSIerさんにとっては設計の手間が省けたり、納期を短縮できたりします。先ほどの人材確保の課題解決の一助になるかもしれません。
瀬川 田中社長がおっしゃったSIer人材の確保・育成に関連して少し触れさせてください。愛知県では3年前から「高校生ロボットSIリーグ」という、高校生にインテグレーションを授業で教えることに取り組んでいます。週に1回3時間くらいの枠で行い、12月にその成果発表会があります。今10校ほどの参加で、当初は愛知県だけだったのが全国から参加するようになりました。当社は3年連続でこの大会経験者に入社してもらっています。予想に反して即戦力になっています。職業に対するミスマッチもない。当社の高卒社員の離職率はいまゼロです。実務を体験していますから。ご興味があればぜひご参加ください。
田中 非常にいい取り組みですね、ありがとうございます。いいこと教わりました。ぜひ検討させてください。
(2024年3月25日号掲載)