座談会:高剛性・高精度に応える自動化アプリケーション
- 投稿日時
- 2023/09/29 09:20
- 更新日時
- 2023/09/29 09:35
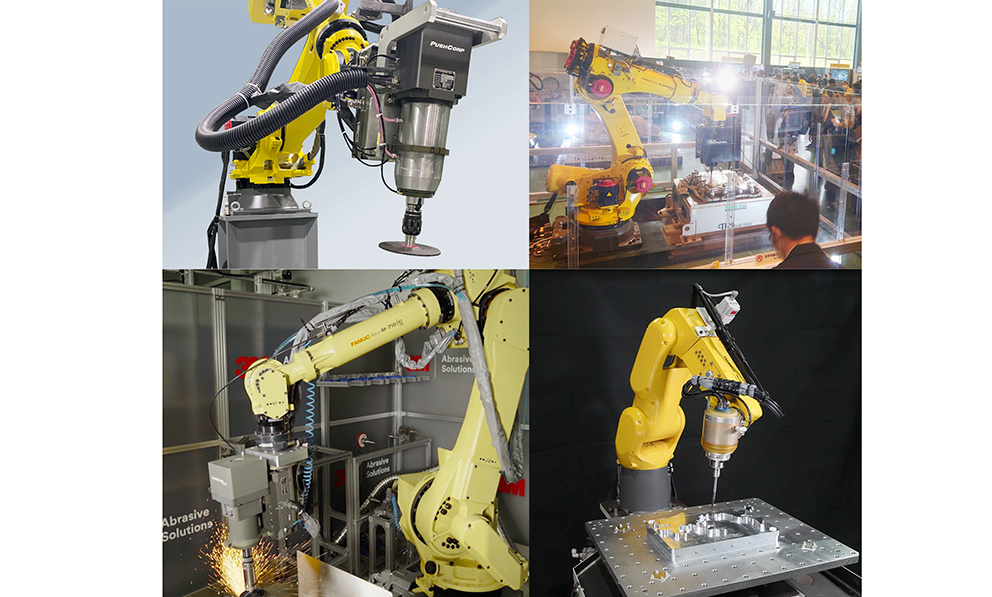
ロボットでできることが広がっている。従来はピッキングや組み立て、溶接、塗装など対象物からの反力を受けない用途が中心だったが、切削加工、バリ取り、グラインディングなどを可能とする高剛性・高精度の自動化アプリケーションが充実してきた。その現状や課題、可能性を探るべくロボットメーカー、SIer、エンジニアリング商社にオンラインで集まってもらった。
熟練者不足を自動化で補う
±0・1㍉の精度ならロボット切削で
――まずは各社さんの強みや導入実績、営業戦略をお話ください。
稲葉清典(ファナック) コロナ禍を経て自動化の位置づけがずいぶん変わってきました。以前は品質向上やコスト削減が主でしたが、熟練者不足や3密回避、製造の継続が前提になるケースが増えてきたと感じます。それに伴いロボットを導入される産業分野、活用アプリケーションも広がっています。当社の開発の基本方針は信頼性。壊れない、壊れる前に知らせる、壊れてもすぐ直せる、を掲げています。信頼性がライン全体の稼働率向上につながると考えております(「ゼロダウンタイム」という商品も)。もう一つの基本方針としてサービスファースト、その中でお客様が商品をお使いいただく限り保守を行う生涯保守を謳っています。国内での設計・製造にこだわり、出荷実績としては産業用・協働ロボットをあわせて累計100万台に達しました。これからも信頼性の高い商品群とパートナー様との連携を更に深めてゆきたいと思います。ロボットのラインナップは0・5㌔グラムから2・3㌧可搬までの200種類以上あります。戦略としては3点あります。一つ目は信頼性の確保は前提としながら、使いやすさに力を入れています。初めてでも簡単に立ち上げ、操作できる商品の充実を進めています。二つ目はお客様の現場の声を迅速に保守、開発に取り入れる機能の充実です。故障診断や予知、リモート診断の強化の他に、新しい機能をウェブサイトからダウンロードしてアップデートできる「ローリングリリース」を一部機種にて始めました。そして、最後は環境。たとえば機構部の軽量化、メンテナンスフリー化のほか、動作の加減速を滑らかにすることによる消費電力の削減など、今後も機能の充実を進めます。
廣田潔(愛知産業) 当社は昭和5(1930)年、溶接棒をベルギーから輸入して販売することから始まり、溶接に関連する商品の販売に注力してきたことで成長してきた会社です。近年ではその商品に付加価値をつけて自動化・省力化システムをお客様に提供しています。30年ほど前にお客様からの要望で、溶接の後工程として溶接ビードを研削するAKグラインダーを自社で設計・製造。研削ロボット、レール走行しながら研削する台車タイプと合わせて500台の導入実績があります。阪神淡路大震災ではAKグラインダー(走行タイプ)は橋梁補修などで活躍し社会貢献できたと当社の会長、社長も誇らしく思っています。最近ではスライダにスピンドルを取り付けてロボットで研削する「プッシュコープ」を販売。コロナの影響もあって出足は鈍かったのですが、ここ1、2年はかなりの引合いをいただいています。粉塵などの職場環境を改善したい、労働力不足を補いたい、熟練工の高齢化に対応したいという要望が大手から中小企業さんまであります。当社は工作機械と同じBTシャンクを持ち、様々なツールを付けた工具を自動交換しながら研削でき、エンドミルでも削れることをアピールしています。戦略としては協働ロボットのセルパッケージの販売を強化しています。と同時にお客様が求めるものをよく把握し、実際のロボットシステムに落とし込んでいくことを製販一体となって進めています。
愛知産業によるロボット研磨システム「プッシュコープ」
岡田充彦(スリーエムジャパン) 当社はアメリカ・ミネソタ州にある3Mの日本法人で、世界各国にある子会社の1社です。文具からテープ、接着剤、電子部品関係、フィルムなど非常にたくさんの事業があります。3Mは鉱石の採掘事業を5人くらいで始め、失敗を経て最初に成功したビジネスが研磨紙(サンドペーパー)でした。私の所属する研磨材製品事業部は最も古くからある部署で、自動車・鉄鋼・電子部品・電気関係などの製造工程で使われる多種多様な研磨材を製造、販売しています。工具の先端につける砥石、ディスクや研磨紙など。自動機に取り付けるホイール状、ベルト状の製品もあります。モノをつくる過程で削る、磨くがないものはおそらくほとんどありません。この10年ほどは自動化の相談をいただくことが多く、SIerさんやロボットメーカーさんと一緒に提案をさせていただいています。当社は相模原に研磨の技術部があり、そこにロボット2台を置いてお客様のワークを研磨したり、基礎データを取ったりしています。
――研磨材の種類は相当多そうです。
岡田 数えたことはありません(笑)。寸法が違うものものも含めると1千を超えるでしょう。砥粒は80番、320番、800番と数字が大きくなると細かくなります。また製品の形状も多種多様で、これをかけ算すると相当な数になります。これだけの種類を揃えるメーカーは世界でも当社を含めて数社といったところです。
岡丈晴(トライエンジニアリング) 当社は来年2月、創業50年になります。一貫して自動車の生産設備や治具をつくり、30年くらい前からはロボットヘミングシステムという自動車のドア・ボンネットの外周部分のかしめ加工を自動化する装置を独自開発して商売を広げてきました。システムとしては今までに400を超える販売で、採用された製品数としては1千を超えます。ほぼすべての日本の自動車メーカーさんに採用され、近年は東南アジアなどでも採用されています。当社はロボットの用途としては対象物に接触し、負荷のかかる動かし方の技術をずっと培ってきました。その中でコア技術はサーボモーターのトルク制御、加圧制御によって接触物に対し均一な力を加えながらロボットアームを移動させること。近年はこのコア技術をさらに生かすべく、ロボットの先端に加工用の主軸モーターを持たせたロボットマシニングやロボットポリッシング、FSW(摩擦撹拌接合)といったシステムのアプリケーションを開発しています。販売実績はマシニングシステムで30台を超え、ポリッシング、FSWはそれぞれ15台を超えます。今後、ますます拡大すると見込んでいます。
――切削やFSWが本当にロボットでできるの?という声もあります。
岡 マシニングシステムを開発した10年ちょっと前、切削加工業界の方からできるわけないと言われましたね。当初は振動しまくって加工機として成り立つようなものではありませんでした。ただその後、振動の仕組みなどを解析して開発した結果、ロボットでもそこそこの加工ができるようになりました。NC加工機に比べると加工精度やスピードは劣ります。でもその代わりロボットならではメリットがたくさんあります。鋳物やFRP(繊維強化プラスチック)のカット・トリミングに有効で、多くの需要があり納入実績も増えています。
――ロボット切削の加工精度はどれくらいですか。
岡 加工するものによりますが、かなり良い条件であれば±0・1㍉の加工が可能です。それ以上の精度を求めるのなら、やはりNC加工機になります。1㍍以上のワークで比較的高い精度が求められないものは案外あります。端部への穴あけ、鋼材表面の黒皮の除去など。大型ワークで5軸制御でないとできない加工は今後、すべてロボットが担えるのではないかと思っています。
成瀬雅輝(豊電子工業) 当社は1964年に創業した約60年の企業です。1980年からは約40年にわたりロボットSIer事業を生業としており、世界に2万5千システムの導入実績があります。グローバルな活動に特徴があり、アメリカ、中国、タイに製造拠点、インドネシア、メキシコ、ポーランドにサービス拠点を展開しています。アプリケーション開発に関しては切削加工全般を担う加工開発室をもち、高周波加熱やレーザー、加熱蒸気、物流関連の設備を開発する部署や、画像処理・形状測定・位置決め関連のセンサーを取り扱う新技術検証室もあります。また航空宇宙関連の開発にも取り組んでおり、トータルインテグレーションカンパニーを目指しています。
――導入された2万5千システムの主な用途は。
成瀬 当社がロボットシステムを始めた頃から素形材分野に強みをもっており、たとえばガラスや陶器、熱いもの、重いもののハンドリングから始まり、特にアルミ鋳造に強く大型ダイカスト用の設備は国内で7割以上の販売シェアがあります。切断やバリ取りも行い、直近では重切削の要求も受けています。
ギガキャストで部品が大型化
大型ロボット、FSWの需要も拡大
――近年需要の高まってきた自動化アプリケーションとその背景について教えてください。
稲葉 EV化についてはギガキャストに代表される一部品当たりの大型化に伴い、大型ロボットの需要が増えています。一方で軽量化の流れも強く、その中で異材・異形状の接合ニーズも増えています。従来のスポット溶接に代わり片側から接合できるFSW、FDS(Flow Drilling Screw)などへの期待が高まり、反力に耐えられる高剛性ロボットのニーズも増えています。併せて、絶対精度を上げていくことも求められています。個体差をキャリブレーションにより吸収することができるオプションも提供しています。当社はNC事業からスタートし、高い動作精度を実現する制御にも強みがあります。軽量化の流れの中でハイテン鋼などの硬い材料の採用が増え、レーザー溶接・切断といった精度が重視されるアプリケーションが増えてきました。専用機と一般汎用機では専用機の方が当然性能はいいのですが、ロボットの柔軟性を評価いただくことも増えてきています。最近ではアームの先端に付けたガルバノスキャンヘッドの活用も増えています。弊社のガルバノスキャナとロボット軸の9つのモーターが同期できるので、高精度、簡単な教示が出来ることが特徴です。
――職人技をロボットが代替できるようになってきています。
稲葉 ロボットを動かしてその作業をそのままダイレクトにプログラムに落とし込む機能を開発しました。プログラムは他のロボットでも再現することができるので、技術移転が容易になります。スキルトランスファーというと大げさですが、その入り口の技術だと思っています。
――先ほど岡さんからロボット切削で加工精度±0・1㍉が可能という話がありました。ファナックさんはどこを目指されますか。
稲葉 目指すところは我々が決めるというより、お客様、市場が求めているのことを理解しながら、そこに合わせたものを迅速に供給できるように常に準備しておきたいと考えています。
廣田 あまり知識のないお客様はロボットで簡単にツライチまで研削できると思われます。加圧や反力を制御するのに力学センサー使ったりすることになります。1回削ってみて、その後センシングして高さを見る。それに合わせて……と、そうしたプログラムをお客様と一緒に作っていくことで初めて実現します。お客様のなかには加工精度±0・1を求める方もいらっしゃり、それには画像やセンサーを使うなど様々な要素が加わり価格が上がります。当社はそのあたりの費用対効果をトータルで提案していかなければいけません。需要が高まっているものにオフラインティーチングがあります。ロボット研削や切削、溶接など多岐にわたっています。
――オフラインティーチングのニーズが高まる理由は。
廣田 ワーク形状の複雑化でしょうね。工作機械と一緒です。現場でのティーチングだと大変な作業になりますから。
岡田 ロボットに研磨をさせる場合、研磨材に求められる重要な性能が3つあります。1つ目はなるべく長持ちすること。研磨材はワークを削りながら自分自身も摩耗します。摩耗が進むと研磨材の機能が低下するため新品と交換しますが、交換中は何も産出しないので、長持ちする研磨材ほど生産性が高くなります。2つ目は安定性。研磨した後のワークの仕上がりにバラツキが少ないことです。これは長持ちと重なる部分がありますが、たとえば1枚の砥石をずっと使い続けた時に、最初と最後で性能変化ができるだけ少ないものが求められます。3つ目は研磨力の高さ。当たり前ですが、同じ作業だと早く終わった方がいい。研磨材メーカーとしてはお客様の要望に合わせ、この3つのバランスを考えて製品を提供しています。その1つに独自開発した精密成形砥粒を使用したキュービトロンⅡ研磨材があります。長年販売させていただき、重要な3つの性能を満たすものです。もう1つ特徴的な製品として不織布に砥粒を塗布した研磨材「スコッチ・ブライト」があり、切削・研削でできた目を消したり、バリ取りなどに使用できます。これをディスクやベルト形状にして自動機で使っていただくケースもあります。
岡 熟練作業者とその後継者不足に伴うニーズは切削、トリミング、穴あけなどの切削加工もあれば、研磨も多くありますね。お客様は作業者が今後不足することはわかっていましたが、呼ばれて訪問すると、当初は熟練作業者から敵視されました。ところが最近は自動化に対してけっこう前向きです。自動化で大事なことはカメラやセンサーを組み合わせてセンシングした結果に基づいて、ロボットの動作にフィードバックをかけて加工する技術です。当社は自動車分野の仕事が多く、EV化の流れでニーズが拡大しています。たとえばバッテリーケースやダイカスト部品。モノが大きくなるので加工機でやろうとすると超大型機を導入しなければいけない。それならロボット切削を導入したいという要求が急速に広がっています。当社内でテスト・トライアルを実施していない週はないほどです。NC加工機と比べて加工精度はどうかという話になるので、それに応えるための様々なアプリケーション開発を進めているところです。バッテリーケースは各自動車メーカーさんで作り方が変わりますが、アルミが増えることで異種金属材料の接合のニーズが多くなりました。その流れでFSWのニーズも増えてきたように感じます。
――異種金属の接合にFSWが有効ということですが、トライエンジニアリングさんのようにそれをロボットで行うSIerさんは他にもありますか。
岡 SIerさんではあまり聞かないですね。どちらかというと当社のFSWのライバルは複合加工機メーカーさんです。近年は高剛性ロボットの開発によって、NC加工機に匹敵するような加工品質が出せるようになってきたのでロボットが有利になってきたと感じます。
成瀬 当社は鋳造、ダイカストに関わる自動化システムの販売シェアが高いものですから、それに伴う後工程の仕上げの注文もいただきます。電池ケース、ストラクチャーパーツ、外板などがそうです。このあたりの自動化アプリケーションは今後、最も注目されると思います。大物ダイカスト部品の加工やバリ取り、表面処理もありますが、やはり異種金属接合に高精度・高剛性の要求は高まると思います。ギガキャストとはいえ、一発で成形できる大きさには限界があります。アルミとハイテン材、金属と樹脂の接合などのニーズは必ず高まります。FSWの話も出ましたね、我々も今後やっていかねばなりません。
豊電子工業の高速バリ取りシステム
熟練ワザをロボットの動きに変換
精度保証するキャリブレーションが必須に
――今乗り越えようとしているハードルや欠けているピースはありますか。
稲葉 加工精度とともに切削速度や研削速度を上げて作業効率を高めていくことに対して、ロボットがどれだけ追従していけるか。加工精度と速度はトレードオフの関係にあり、引き続き課題だと思います。またスキルトランスファーの技術については現時点では出来ることが限られています。入口に立ったばかりですが、将来的にはその適用範囲を広げてロボットの使いやすさを向上してゆけるように努めます。
廣田 研磨材の角度やエンドミルの方向、加工の角度を、干渉も考慮しながら変えるオペレーターさんの動きをどうやって、ロボットの動きに変換するのかはやはり課題です。我々は人の動きを見て、どれくらいの力がかかっているのかまでを含めて詳しく見ないと失敗するということを学びました。稲葉さんがおっしゃった「スキルトランスファー」に期待しつつ、新情報はぜひ教えていただきたいと思います。研磨材の交換の話がありましたが、幸い当社が取り扱うスピンドルにはBTシャンクがあるので、研磨ツールも荒加工・中仕上げ・仕上げ用とストックしておいて工作機械のように自動交換できる仕様になっています。
岡田 成瀬さん、岡さんから話がありましたように、EV化が進んで部品が大型化し、バリ取りなどの研磨の自動化も進んでいくと思います。それに対して長持ちする、品質が安定する研磨材を当社としては引き続き開発を進めていきます。一方、プロセスとして構築できないとお客様はメリットを感じていただけない。どの製品を選び、どんな使い方をするのが効率的かを示すことも必要ということです。ロボットに適した研磨材は何か。倣い加工をするときにどんな荷重、位置制御が必要かといったことをSIerさん、ロボットメーカーさん、ツールメーカーさんと一緒に考えていきたいです。
スリーエムジャパンのロボット研磨ラボでの加工のようす
――将来、開発したい研磨材はありますか。
岡田 開発の中身は社外秘なのでお話できませんが、自動化を進めるのと同時に作業環境の改善にも取り組んでいます。研磨作業には必ず粉塵が発生します。どうすれば粉塵を発生しにくくできるか、集塵しやすくなるかといった観点で開発した研磨ディスクもあります。現時点ではロボット専用の研磨材はありませんが、将来的には高精度を狙った専用の製品が必要になるかもしれませんね。
岡 切削加工ではロボット専用の切削工具を工具メーカーさんと一緒に開発しています。ロボットは切削抵抗を受けやすいので抵抗がより少なく、かつ切れ味がいいという、ちょっと矛盾した性能です。あとロボットならではの利点があります。人間だとそんな力じゃ押せない、そんな作業は危ない、欠けたら大変、といった作業がロボットだと安全を確保できるのである程度、無理ができます。当社としてはやはりロボットでどこまで加工精度を出せるのかが課題として1番大きい。稲葉さんから話があった、ロボットの個体差を吸収するための、あるいは絶対的な精度を保証するためのツールキャリブレーションは今すごく求められています。
成瀬 刃物については当社もツールメーカーさんと開発しています。すでにリリースしたものですと、オーエスジーさんと協業した高速バリ取り用の刃物があります。今後はロボット本体の高剛性化などの性能アップに非常に期待したい。具体的に言えば岡さんもおっしゃいましたが、やはり振動対策。仕上がりの面粗度までを求められると振動しないことが重要になります。あとワークが大型化すると追従性、空間精度も重要になりますね。当社はバックグラウンドが機械装置のインテグレーションで、その要素としてはメカ、電気制御、ロボットをいかにお客様の要望に沿う形、品質に仕上げて供給するかをこれまで脈々とやってきました。でも今後はデジタル制御、サイバーフィジカルの領域を含めてソフトウェアのインテグレーションもできないと、トータルで問題を解決することは難しい。ちょっとしたミドルウェアくらいは作れないといけないと思います。
ロボット本体の高剛性化に期待
製造ラインをチームジャパンとして供給
――業界が発展するための課題や企業間連携の可能性についてはいかがですか。出席者への要望もあればぜひ。先ほど成瀬さんからロボットの高剛性化に期待したいという発言がありましたね。
稲葉 本座談会であらためて感じたのは求められる要素技術は用途によって大きく異なるということでした。成瀬さんがおっしゃっていたインテグレーションの技術、合わせ込みの際にロボットとして求められるものをメーカーとしてしっかりと理解することが大事だと思います。そのためにもパートナーの方々との連携を持ちながら、常にアプリケーションの方向性、要素技術の情報共有を密に行ってゆきたいと思います。扱いやすいロボット、ロボットが自動化のインフラの一つとなることを目指して努めてゆきたいと思います。
成瀬 ファナックさんが続々とリリースしている高剛性・高精度ロボット、いろんな分野で使わせていただいています。我々は現場に1番近い立場として様々な情報が入ってきます。それを正確に捉えて、昨今ですとデータも添えてロボットメーカーさんにフィードバックしていきたい。SIerさん同士と交流もしながらいい製造ラインをチームジャパンとして供給していくことが肝要だと思います。
――トライエンジニアリングさんはFSWで先行していますが、先ほど成瀬さんから協力の希望がありましたね。
岡 自動化システムにはセンサーやカメラが必要になり、自社だけですべてを構築することはできず、いろんな企業さんとのコラボレーションが必要です。ですから必要な技術を最適なところから取り寄せて、それをきちんとまとめ上げる技術がSIerに求められます。当社としてはどこでも扱うような汎用的な技術に取り組むのではなく、自社の得意分野を生かした突出した技術を究極まで突き詰める。他社さんから欲しいと思っていただけるように、また同業者から協業の申し出をいただけるようにならねばと思っています。汎用的な技術では世界で生き残っていけません。
廣田 当社もお客様のニーズに沿った形でより良いものを提供していきたいと思います。昨今話題のアディティブマニュファクチャリングについては当社としても溶接機を応用してロボット積層造形に取り組んでいます。当社にはSIer機能もありますが歴史は浅くそれほど規模も大きくありません。エンジニアリング商社として皆さんと様々な情報交換をさせてもらえたらと思います。
岡田 皆さんおっしゃられたようにお客様が何を求めているのかを把握し、そのニーズに合わせた商品を提供し、有効活用されることが一番だと思います。そのためにツールメーカーさん、インテグレーターさん、ロボットメーカーさんと情報交換をしながら協力していきたいですね。本来であれば汎用の仕組みがあって、それをすべてのお客様が利用してくれれば話は簡単ですが、それができないから研磨の自動化には各社の協力が欠かせないのだと思います。
(2023年9月30日号掲載)