INTERMOLD2024レポート
- 投稿日時
- 2024/04/26 09:23
- 更新日時
- 2024/04/26 09:32
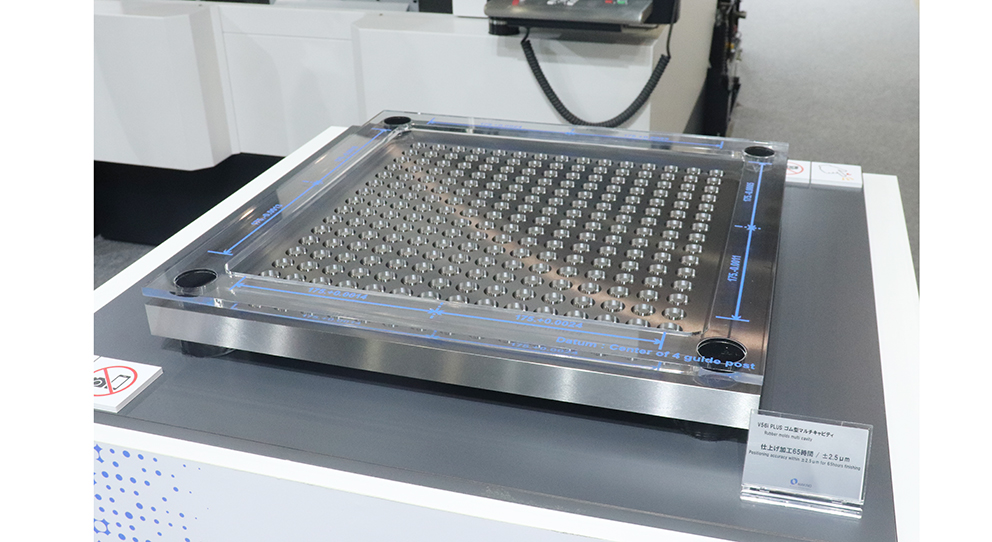
INTERMOLD2024(第35回金型加工技術展)/金型展2024/金属プレス加工技術展2024)が4月17日から19日にかけて、インテックス大阪(大阪市住之江区)で開催。合計3万7057人が訪れた。主催する日本金型工業会の小出悟会長は開会式で「100年に一度の大変革の時代、と言いながらコロナ禍も含め5年たっている。もう情勢が変化し終えたかと言えばそうではない。しかし今出展社の中に、こう変わるべきだという方向性を示すものが多くある」とあいさつした。その方向性の一端を伝えるべく、会場を取材した。
牧野フライス製作所は長時間加工を可能にするテーブル温度安定機能を搭載した、立形マシニングセンタ「V56i PLUS」を展示。「金型加工は長時間におよびがち。従来機はZ方向の熱変異が理論的には起こり得る構造だったが、テーブル内部に管を通し温調したクーラントを常に循環させることで長時間加工してもZ方向のずれを極限まで抑えられる」と利点を訴求した。加工時間が105時間に及ぶサンプルワークも展示し、Z軸方向の位置誤差を±2・4㍈に抑えていることを示した。
ワークの大型化に対応
5軸マシニングセンタ「MU-6300V-L」を用いたダイカスト金型の加工を提案したのはオークマ。3軸であれば上部から工具をアプローチして加工することが多いがワークが深いと工具が長くなり、ビビりを抑えるため加工条件を上げられない。5軸であれば工具長短縮が叶い、加工条件向上による時間短縮が出来るとアピール。「当社の機械は剛性が高いので荒加工から仕上げ加工まで出来る。今回は荒加工の効率化を提案している」(担当者)とした。「C&GシステムズのCAM-TOOLに新たに実装された機能を活用しており、従来だと5方向から金型を加工しようとすると作業者がどの方向から適切に加工するか考えてプログラムを作る必要があったが、ボタン一つでパスを作ってくれる」(同)とした。
オークマの5軸マシニングセンタ「MU-6300V-L」を用いたダイカスト金型
ファナックは小型切削加工機「ROBODRILL α-D28LiB5ADV Plus Y500」をメインにPR。Y軸ストロークが500㍉に延長され大型ワークに対応。EVの部品加工のニーズを狙う。
金属AM×切削のハイブリッド機「LUMEX」によるサンプルワークを並べてみせたのは松浦機械製作所。冷却水管を三次元かつ自由に造形できるのが特長で、金型温度を一定に保てるため射出成形時のサイクルを早められる。成形品の反りや変形が少なくなるメリットもある。「大阪開催のインターモールドへの参加は10数年ぶり。我々も研究でこの機械の可能な加工をより深く見極められるようになっており、今いちど金型市場の反応を見るのが目的だ。例えば昔は射出成形のダイカスト金型しか造形できないと言われていたが、アルミダイカスト金型にも我々のAM機が活用でき始めている」とする。
放電加工でもワークの大型化に対応を迫られる。三菱電機は、2月のプライベートショーでお披露目した中大型形彫放電加工機「SG70」を今展を皮切りに発売する。スタンダード機のSGシリーズのラインナップに追加。軸移動量はX軸1000㍉、Y軸700㍉、Z軸500㍉となった。自動車向け金型の大型化により、大きなワークを加工できる大型機の需要が増えている。また、ガスタービンブレードや航空向けの部品もメインターゲットとする。独自AIによる「Maisart」を標準搭載。加工状況をAIが自己判断し、加工形状や面積によってジャンプアップ量を調節、制御を最適化し安定した加工が行える。
初お披露目となる三菱電機の中大型形彫放電加工機「SG70」
西部電機もモーターコアなどの大型化などに対応するため800㍉×600㍉のストロークを有する超精密・大型ワイヤ放電加工機「SuperMM80B」を提案。会場では自動結線のデモンストレーションを実施。担当者は「自動結線が100%入っていくと夜中に加工が止まって工程が崩れるなどがない」(担当者)とし、一日目の取材時は供給回数が400回を超えていたが失敗は0だった。「会期中ずっと回しており会期終了時には2000回近くまでいく。確率論として、それで0であれば、成功率はほぼほぼ100%だと感じてもらえる」(同)とした。
スギノマシンは元々、洗浄用途で原発業界などへ提案していたウォータージェットピーニング加工機「CWJP」を、金型業界へ提案した。高圧水をワークにぶつけて微細な気泡を発生させ、泡が破裂する衝撃で金属の表面を「叩く」もの。「従来の研磨剤を使うショットピーニングでも金型の表層に応力を付加できるが、深度が足りない。CWJPのほうが深く打撃できるため金型の疲労強度をより向上でき寿命を延ばせる」という。ダイカスト金型の寿命を9500ショットから1万2000ショット(1.4倍)に延ばせた実績や、精密金型の寿命を7万ショットから21万ショットへ向上できた例もある。研磨剤の除去も必要ないので洗浄も兼ねられる一石二鳥の設備だ。
アマダマシナリーはデジタルプロファイル研削盤「DPG-150」とロボットを組み合わせたデモを披露した。特長は搭載したデジタルプロジェクター。最大400倍の高倍ルーペで見たい箇所を指先ひとつで拡大・縮小可能。ワークのエッジを検出し、CADデータとの誤差を瞬時に自動計測して自動補正加工もできる。砥石・ワーク計測の自動化とチャート作画の簡略化により従来比で工数を27%減らせるという。「プロファイル研削は長らく職人の手と目によるアナログ作業だったが、誰でも高精度な測定と加工ができる。一方で自動化しかできないわけではなくハンドルで従来通りの汎用的な使い方も可能。つまり誰でも使えるマシンだ」とする。
東洋研磨材工業は鏡面ショットマシン「SMAP」を提案。「職人磨きを装置化し、研磨工程を効率化した。4月に開発した『SDメディア』は母材がゴム質でダイヤモンドをまぶした粗磨き用研磨材で、従来品よりスピーディーに研磨できる」(大内達平代表取締役)とする。
富士機工はNC位置決め装置「ボール盤NCβ2軸」をアピール。NCによる位置決めでケガキやポンチ作業が不要で、寸法合わせがカンタンにできるボール盤だ。
精密や深彫を追求
微細領域に強みを持つ日進工具は1月発売のレンズ型エンドミル「MLFH330」を提案した。ボールでもスクエアでもラジアスでもない、先端がレンズのように緩いR形状を描く工具。「φ1から取り揃えている。径の太い工具でこの形状のエンドミルはあったが、小径工具で実現したのが我々ならでは」という。例えばφ6のボールエンドミルの底刃は通常R3だが、MLFH330はφ6でR8のため加工効率が向上。「矛盾するようだが微細加工を高能率化できる。金型業界では精度を上げつつ加工時間は縮めたいという相反する要求が増えている。形状は曲面に限るが、はまる加工ではかなり効率が上がる」という。
日進工具の先端が緩やかなRを描くMLFH330
MOLDINOは新製品「EPDBPE-ATH」が目玉。フリーネックタイプの深彫り加工用ボールエンドミルだ。大物ダイカスト金型、鋳造金型、プラスチック金型全般の深部加工に向く。金型の大型化により深彫りが増えているが、一般的な工具ではシャンク部と首下の部分に段差があるため、ワークの深さに合わせた工具選定や交換が必要になる。「フリーネックタイプは干渉フリーで、突き出し量を加工部の深さに合わせて調整可能。1本で調整できるため工具集約もかなえる」(担当者)とする。今回24アイテム追加、ラインナップを大きく拡充した。
MOLDINOのフリーネックタイプの深彫り加工用ボールエンドミル
MSTコーポレーションは「焼ばめホルダ スリムライン」と、交換式工具が取付けできる「超硬アーバ」を組み合わせたボーリング加工用焼ばめホルダ「ミルボア」を訴求。金型ガイド穴なども含め、ボーリングヘッドで行っている穴加工をヘリカル加工で行なうことで、スキルレス化などの利点がある。「ボーリングだと寸法調整が必要のためスキルが必要だがボーリング加工だとNCのほうが対応するので、金型業界のベテラン不足に貢献できる」(担当者)とした。自動化が進む中、マシントラブルにつながる「つながった切りくず」の対策が求められるが、その点でもミルボアの優位性をPRしていた。
ZOLLER Japanはユーザーの工具室をイメージした展示を行った。外向きに展示品を配置するのではなく、中に入ると「自社の工具室に何があれば便利かイメージしやすい趣向」(担当者)と話す。測定精度2ミクロンを保証するツールプリセッター「venturion」を用いれば、金型の仕上げ加工における取残が事前に把握できるので最小化で効率アップを図れる。またすそ野を広げるため廉価版の「smile」を初出展。やや精度は落ちるが上位機種に比べると4割ほど安価となる。
ブルーム−ノボテストは4月1日にリリースした金型計測プロセスの自動化提案「フォームコントロール X」を紹介。従来の工作機械の加工終了後、ワークを取り外し測定室に運搬し、測定を実施。測定結果がNGの場合は再加工といった測定プロセスを工作機械に集約して自動で測定を行うもの。タッチプローブとの組み合わせで機上計測を行うパソコン用のソフトウェアだ。NG品に関しても機上にて追加工が実施できるメリットがある。
C&Gシステムズは5軸マシニングセンタ対応のCAD/CAMシステム「CAM-TOOL」の新バージョン「V20.1」を出品。新切削モードと5軸工程集約で荒加工の効率化、そしてAI搭載による自動化・省力化を推進する。新加工モードの「負荷一定駆け上がり加工」は、傾斜切り込み時の回転数をコントロールし、工具の負荷と破損を抑制。工具寿命の改善と加工時間短縮を叶える。
(2024年4月25日号掲載)