インタビュー
芝浦機械 取締役 専務執行役員 成形機カンパニー長 小池 純 氏
- 投稿日時
- 2025/05/14 15:37
- 更新日時
- 2025/05/14 15:41
グローバル市場を見据えたギガキャスト対応の超大型ダイカストマシン開発
優れたダイカストマシンで世界のクルマ作りを支えてきた芝浦機械。この4月には満を持して型締力1万2000㌧クラスのギガキャスト対応の超大型ダイカストマシン「DC12000GS」の受注を発表した。このジャンルでは中国、欧州、日系の各社が鎬を削る中、同社はこれまで培った技術のフィードバックと将来を見据えたエポックメイキングな機種の開発を視野に入れており、後発ながらメインプレイヤーの座を虎視眈々と窺っている。
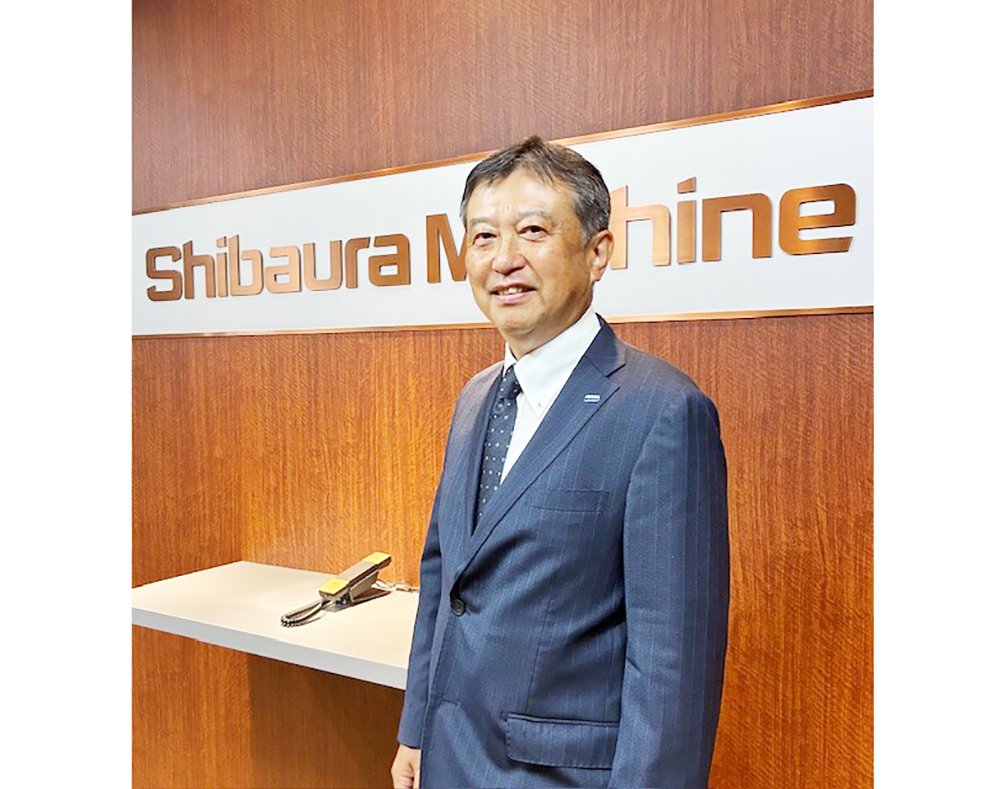
——ギガキャスト対応の超大型ダイカストマシンの開発に踏み切った理由をお教えください。
数年前の国内自動車メーカー各社の動向は、EVかハイブリッドか、内燃機関車なのか、また車体を構成する素材も鉄なのかアルミなのか、いったい何が主流になるのかが見通しづらい状況でした。実際に超大型ダイカストマシンを製造するとなると、生産設備や物流などクリアしなければならない問題が多々あります。
とはいえ、中長期的にはEVシフトが進行していくと考えていますし、それに伴い超大型ダイカストマシンのマーケットも今後さらに拡大すると見て開発に着手しました。
——すでに国内外のメーカーが超大型ダイカストマシンを出していますが、貴社製品の優位性は。
ダイカストで特に重要なのは射出性能です。特に超高速技術という部分についてはユーザーからも高い評価を得ています。これがギガキャストになると、当然サイズの大きい薄肉の成形品になります。
無論、厚みのある所もありますが、エンジンブロックなどに比べて溶湯の流動長が長く、薄くなります。こうした成形品における射出性能が評価されて、自動車業界の皆様から支持されてきました。その流れを踏襲した超大型ダイカストマシンに仕上げることが、引き続き当社の強みであるのではないかと認識しています。
——超大型ダイカストマシンを製造するにあたって、新たなラインを立ち上げたのでしょうか。
当社相模工場の3500㌧クラスを製造しているラインで製造します。こちらでは射出装置と制御装置を作り、現地に運んで組み付けます。型締装置は国外の協力企業から供給してもらう予定です。
——1万2000㌧ともなると、射出装置だけでも運搬は容易ではありませんね。
一般的に超大型ダイカストマシンは型締力6000㌧クラスのもので全体重量が約500㌧、射出装置だけでも約70㌧ほどになります。今回の1万2000㌧モデルですと、射出装置は80㌧を超えてきます。ですので、ある程度部品を分割して運ぶことになります。運搬に関しては設計段階から考慮に入れておりますので、道交法に抵触しない範囲内でデリバリーできると考えております。
——超大型ダイカストマシン運搬は通常のコンテナ船では対応できないとも聞きます。
射出装置と制御装置に関しては、チャーター船を使わずとも通常便で行けるという前提ですので、コスト的な不利が生じることはありません。
■機械の小型化を視野に
——運搬の問題がある程度クリアできれば、国内ユーザーへの導入も進むのでは。
EV生産で先行しているテスラや中国メーカーは後発ゆえ、様々なプラットフォームでの製造を視野に入れることができ、積極的にギガキャストをラインに導入してきました。一方、日本は各メーカーが優れた生産方式を確立し、グローバル競争を勝ち抜いてきた背景があります。
それゆえ、国内での急速な普及は少し難しいでしょうが、グローバル市場においてはまだまだこれからが勝負と考えています。国内外とも、今後は技術面とコストの部分がトレードオフして、最終的にどちらが有利になるかという判断になっていくのではないかと思います。そこに対して私共は最適な生産設備をしっかり提供していきたいと考えています。
——今後は貴社が開発中の低圧鋳造技術も超大型ダイカストマシンに取り入れていくのでしょうか。
型締力6000㌧の製品を3500㌧クラスで作る、という目標を立てて取り組んでいます。当社のテクニカルセンターですでに検証中で、例えば通常、型締力1650㌧の成形品を800㌧で鋳造し、成形品もバリが少なく、仕上がり良好という結果も出ています。今後さらに技術的な推進を図り、いずれは超大型ダイカストマシンにも取り入れていきたいです。
——機械のダウンサイジングとなると、貴社の優位性がさらに高まりますね。
この点は他社との大きな差別化の1つになると考えています。遠い未来の話ではなく、来年とか再来年とか、そういう時間軸で開発するよう取り組んでいきます。また、私共には既存の顧客も数多くあり、これらのお客様も小さな機械で大きく打ちたいとう根源的な要求もありますので、そうしたニーズも視野に入れていきたいですね。
一方でマシンの性能を極端に上げたところで、お客様の作りたいモノに合うかという問題もありますので、今後はお客様としっかり連携し、開発を進めていくことが重要だと考えています。