連載
扉の先92/新光機器、ナット・ボルト溶接の下部電極 コスト3分の1に
- 投稿日時
- 2025/04/14 13:11
- 更新日時
- 2025/04/14 13:15
ティーチング補正いらず生産性UP
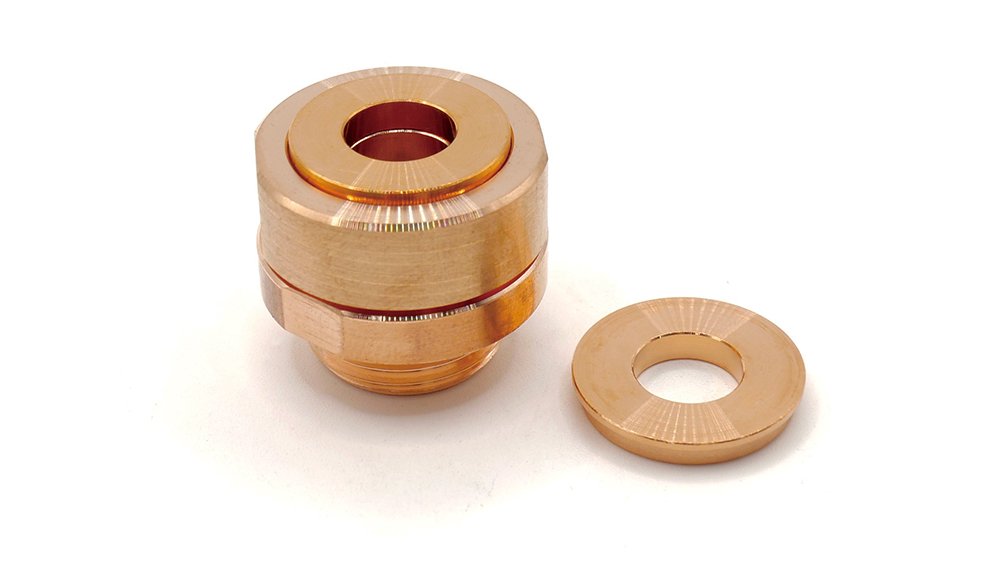
ナット・ボルト溶接の下部電極「段付きワッシャUFO」。消耗時は右のワッシャチップのみの交換で済むためコスト削減と省資源に
ナット・ボルト溶接は上部電極と下部電極でワークを挟み、電流を流して行う。下部電極は一体式で、ワークの当たる部分が消耗したら研磨して使い、丸ごと交換するのが従来の考えだった。
抵抗溶接をメインに各種溶接用電極と周辺機器を手がける新光機器(愛知県名古屋市西区・田中英樹社長)は、下部電極をチップホルダー・段付きワッシャチップとチップボディの3部品に分割した「段付きワッシャチップUFO」を開発。先端部となるワッシャチップのみの交換で済み、ランニングコストを約3分の1程度におさえられ省資源を実現した。
従来一体型の下部電極を3つの部品に分割。分割した分、電気が上手く流れるよう、当たる面の平面度が重要になる
「自動化に取り組まれるお客さんが増え、ロボット溶接の需要が伸びた。スポット溶接では電極面が傷んでくると研磨して使うが、高さが変わるため、その度にロボットのティーチングを補正しなければならず、非常に手間。高さが変わらないよう、かつコストを抑えられるようにユーザーの悩みをもとに開発した」と田中社長は話す。
めっき処理を施した鉄板に含まれる亜鉛と、下部電極の銅は溶接回数が増えると合金層が生じ、溶接の不具合の原因になる。導電性に影響するため、研磨で銅の面を出す必要があるが、ワッシャチップUFOなら3㍉メートルほどの部品の交換のみで済み、従来200~300ワークごとに必要だった再研磨とティーチング作業の手間やコストを省ける。
段付ワッシャチップを組み付けると打点面がチップホルダーより少し上に出る。また溶接時に加圧がかからないところをねじ部とし、緩みを防ぐ。分割した部品の面に隙間ができないよう、平面度にも気を払い高精度に仕上げていることもポイントだ。
2009年の発売以来、売上は右肩上がりで、過去最高の販売数となった23年を昨年は超える見込み。累計枚数は200万枚を突破した売れ筋製品となっている。
海外にも展開しており「無人化工場などロボット導入が進んでいる米国での売れ行きは特に好調」と言う。上部電極の対応製品についても近々発表予定と話す。
■耐久性40倍のコンタクトチップも
もう一つ売上が急激に伸びているのは3年前に開発したアーク溶接のトーチ先端に取り付ける「ZMコンタクトチップ」。消耗品として短期間で廃棄されていたコンタクトチップが、特殊金属により従来の約40倍、条件によっては96倍の耐久性を持つ。
ここ数年で増えている低スラグワイヤーはチップの摩耗が特に激しく、従来のチップだとすぐに摩耗し交換しなければならないが、ZMチップなら高い耐久性を発揮。交換の手間を大幅に省き、自動化をより加速させる。
売上は3年で18倍に伸び、「米国での売上伸張は目を瞠るほど」と勢いを語る。
田中英樹取締役社長
(日本物流新聞2025年4月10日号掲載)