連載
扉の先90/前畑精機、まだまだ広がるパーツフィーダーの可能性
- 投稿日時
- 2024/12/11 13:05
- 更新日時
- 2024/12/11 13:13
広い視野で市場と新製法を切り拓く
パーツフィーダーは、こと製造業では馴染み深い装置だ。例えば製造装置や検査装置の前後。大量の小さな何かを任意の向きで整列させて高速で供給したい場合には、まずこの装置にお呼びがかかる。特にオートメーション化が著しい自動車業界ではかなりの数が稼働しているが、一方で「あたりまえ」の存在すぎてその奥深さにまではなかなか目が至らないのではないか。回転と振動というシンプルな物理法則を駆使して最低限の動力で仕事をするパーツフィーダーはその実、ロボットより安いコスト、高いスループットで自動化ラインにおける関節軟骨のような重要な働きをしている。前畑精機(名古屋市南区、1982年設立)はパーツフィーダーの可能性を突き詰め、その価値を最大化すべく製作方法の変革にも挑む。
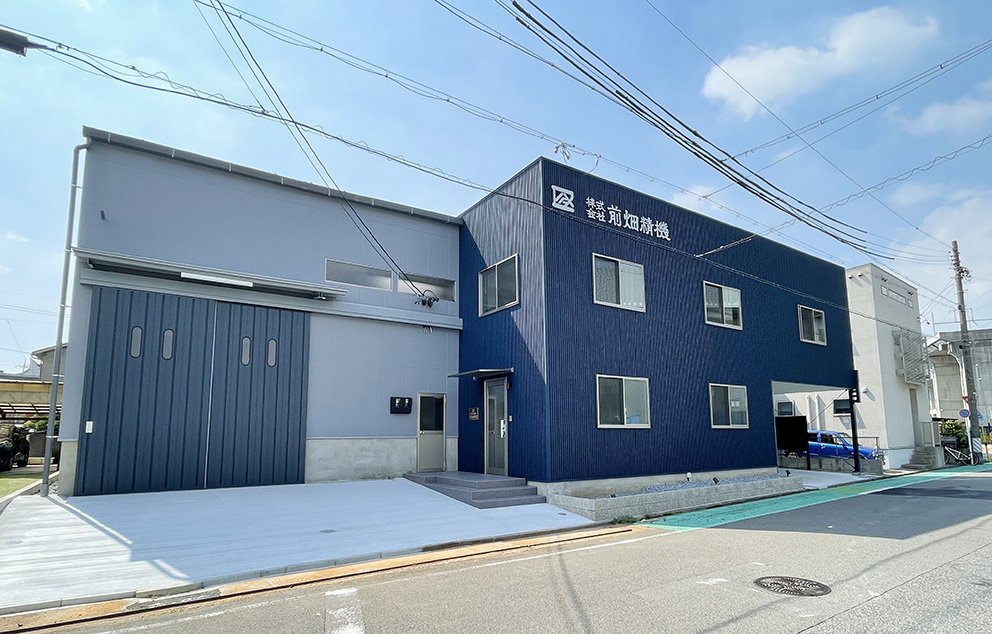
前畑精機の本社
ほとんど無数にも思える指の先ほどの金属部品が、回転する装置へ無造作に投入され、かと思えば綺麗に並んだ状態ですべて同じ向きに整えられて出てくる。しかも供給ペースは1部品あたり数秒。早ければ0.5秒に1個だ。これを行うのはもちろん最新鋭のカメラを備えた高額なロボット――ではなく、回転と振動、重力や摩擦という基本的な物理現象を利用したパーツフィーダーと呼ばれる装置だ。
前畑秀樹社長
発想の原点は「この部品に遠心力や振動が加わったときにどう重心が動くのか?」というシンプルな原則。ボルトやねじならある程度経験から動きが予想できるが、そうではない物に回転や振動を加えたときにどう動くかは未知の世界だ。煮詰まったときには現物を机の上にバラバラと落とし、その動きをじっと見てヒントにすることもある。そうして挙動の傾向を見極めたうえで、からくり的な知見とごく限られた動力を組み合わせて、整列・選別したいモノの動きを狙い通りに制御するパーツフィーダーが完成する。エアー、電気といった動力を極力使わず、かわりに振動上の物理法則と自然現象とをフル活用する。導入費用はロボットシステムの10分の1。そこには某教育番組のからくり装置のように、見ている人を引き込むような機能美が備わっている。
前畑精機は創業当時からこのパーツフィーダーを製作する専業メーカーだ。土地柄もありかつては顧客の9割近くを自動車産業が占めたが、リーマンショックで受注が激減したことを契機に、それ以外の市場の開拓を進めた。今は医薬品や食品、電子・電気など様々な業界に向けてパーツフィーダーを提供。自動車以外の売上も足元では全体の約3割まで増えた。
パーツフィーダーは回転による遠心力と振動などシンプルな物理法則を利用し、対象物を狙った向きに整列させ高速で提供する
例えばボルトやねじ、あるいは錠剤やアンプル、アーモンド、消しゴム、ペットボトルのフタなどあらゆる量産性のある小物が同社が対象とするワークだ。バネやC型のため互いに絡み合ってしまうスナップリングは従来パーツフィーダーが苦手な形状だが、同社はこれらをほぐしつつ選別・整列させる難度の高いパーツフィーダーも開発した(対応の可否は都度テストにて判断)。装置内部でボルトとワッシャーをそれぞれ同じ向きに整列させ、重力を利用してボルトをワッシャーの穴に落とし、組み付けた状態で供給することもできる。ロボットSIerと協同で顧客の要望に対応することもあり、前畑秀樹社長は「単純にパーツフィーダーを売る、ということではなくお客さんの工場における問題解決を重視している」と話す。
前畑精機の創業は1982年。第二次オイルショックによる不景気のさなか、前畑秀樹・現社長の父がたまたまパーツフィーダーをどこかで目にしたことがきっかけだったという。「その当時、父は42歳で私は中学生。いきなり父が脱サラをして前畑精機を起業したので驚きましたよ」と前畑社長は述懐する。詳しくは後述するが、パーツフィーダーは基本的には手作業で製作される。そのため大掛かりな設備投資が不要で、溶接機やコンターマシン、ボール盤程度でスタートできることも創業者がパーツフィーダーを選んだ理由のひとつだったかもしれない。
パーツフィーダーの外観
前畑社長には当初、会社を継ぐつもりはなかったという。しかし「ほんの手伝い程度のつもり」で入社した半年後に父が病気を患い、気づけばそのままなし崩し的に跡を継ぐことになった。フィーダーはワークの挙動に合わせて手作業で細かい調整が必要で、先代は手先が器用で何でも作れたが、「私は手先が不器用で構想はできてもフィーダーの製作はできなくて」。そのため経営を担い始めた当初は「当時在籍してくれていた職人の方に製作を頼り切り」の状態だったという。「ですから職人の技術に対するリスペクトはものすごくあります」と前畑社長は力を込める。
パーツフィーダーは基本的に、主に振動と遠心力という二つの力を利用してワークを狙った向きに揃える。この際、前畑精機ではエアーを「極力使わない」のが原則だ。前畑社長は「職人的なこだわりなのかもしれないけど」と前置きして、こう教えてくれる。「エアーを使うのは私は邪道だと考えています。振動を利用して重力に抗わず、自然と狙った向き、角度に物を動かすのが美しいフィーダーだと考えていますし、だいいち駆動源が増えるとお客さんも喜ばない。そういう『力技』を使わずいかに駆動レスな設備を作れるかが、すなわちパーツフィーダー屋の評価かもしれません。シンプルイズ・ベストなんです」
モーター、エアー等の外部要素をガチャガチャと装置に付け加えた挙句、すべてを取っ払ってシンプルな姿に戻した方がよほどうまくワークをコントロールできた、ということが少なからず起こり得るのがパーツフィーダーの世界なのだという。「これが本当に難しいところであり、面白いところ」だと前畑社長は語る。「例えば『ピタゴラ装置』も、エアーでシュっと吹いて玉を動かしていたら興ざめでしょう? それと近い世界かもしれないね」。なるほど確かに、と思わずうなずいてしまう。
とはいえ使える駆動源が限られる以上、もちろん狙い通りにワークを動かすのは簡単なことではない。しかもある程度のセオリーこそあるものの、パーツフィーダー業界では基本的に図面を描かず、製作者の頭の中で完成形を思い描ければその瞬間から製作がスタートするのだという。具体的にはまず頭の中の構想に従い型紙を切って、コンターマシンで金属板を切り出して各パーツを切り出し、手作業で板を曲げたり溶接したりしながら装置全体を形づくっていく。経験がモノを言う世界であり、形になるまでだいたい3年はかかるそうだ。
このパーツフィーダーでは上からボルトが、下からワッシャーが向きが揃った状態で流れ、双方を組み付けた状態で装置外へ供給する
フィーダーは切り出したパーツを3次元的に曲げる必要があり、通常の手法で3D設計しても、それを展開図にして2D図面化するのが難しい。同社は現在そのためのノウハウを蓄えており、そうして2D化した図面データをレーザー加工機に送り、型紙と人手による部品製作を自動にしたい考えだ。まだ実用化には至っていないが、3D設計したパーツフィーダーを一挙に3Dプリンターで出力する取り組みにも挑戦している。「まだ緒についたばかりですが、実現すれば海外向けのリピート製品も現地で簡単に作れるかもしれない」。これが形になれば、技術者はからくりの構想に時間をかけてより付加価値の高いパーツフィーダーを生み出せるようにもなる。
パーツフィーダーはニッチな製品のため、同業者が市場にどれだけあるか、市場規模がどれほどなのかをつかむことが難しい。前畑社長もリーマンショックを機に徹底して同業者を洗い出して市場規模を掴もうとしたが、手掛かりがなく非常に難航したという。「それでも検索を駆使して同業者の数や客先、売上規模など調べられる情報をすべて洗い出し、自分なりのデータベースを作成しました。私が勝手にその会社の生産台数まで計算して(笑)」。その結果、見えてきたのはやはり「業界全体の売上のうち6、7割を自動車が占めているのではないか」という結論だった。しかし裏を返せばこれは、自動車業界以外にはまだまだパーツフィーダーが必要とされる余地が眠っているということでもある。
「私らが知らないパーツフィーダーの使い方がまだまだありそうだな、とすごく感じます。我々も自分を『パーツフィーダー屋』だと思ってはダメかもしれません。パーツフィーダーはあくまで1つのアイテムで、『選別屋』とか『整列屋』だとか、そういう柔軟な発想で物事を捉えればまだまだニーズはあるだろうなと」
選別、あるいは整列はどちらも普遍的なニーズだ。例えばゴミも整列させないと分別のためのレントゲン検査ができないため、どんなゴミもある程度マルチに整列できる装置を製作したこともある。「ここにきてまだまだ潜在的な用途や市場がありそうなことに、ワクワクしています。要するに最低限の動力とからくりの世界で解決できる物事は意外と世の中に多いのではないかと。そういうことを考えられる仕事はけっこう幸せです。楽しいですよ」
工場内部。パーツフィーダー製作にはあまり加工機を用いないためスッキリしている
(2024年12月10日)