連載
新光機器、耐久性40倍のコンタクトチップが溶接を変える
- 投稿日時
- 2024/10/29 14:20
- 更新日時
- 2024/10/29 14:26
すぐ捨てるモノが1週間使える世界へ
短期間で捨てて当然、という認識のモノが世界には溢れている。溶接業界では、アーク溶接でトーチ先端に取り付けワイヤを案内するコンタクトチップがまさに「消耗品」だった。多くは2時間ごとの休憩の度に、現場によっては3ワーク程度で交換・廃棄されるこの部品で、新光機器(名古屋市西区)が従来比40倍もの高耐久を実現した。「ZMコンタクトチップ」(以下ZMチップ)と名付けられたこの製品が今、発売3年で初年度の18倍の売上を記録し、注目を集めている。
同社は溶接用電極が主力の専門メーカー。取引先は3千社に及び、国内外で92件の特許を持つ開発型企業だ。顧客の近くに拠点を構えて要望や課題を聞き、溶接を熟知したエキスパートが相談に乗る現場密着体制で成長。だが同社でもコンタクトチップの寿命は数十年来の課題だった。
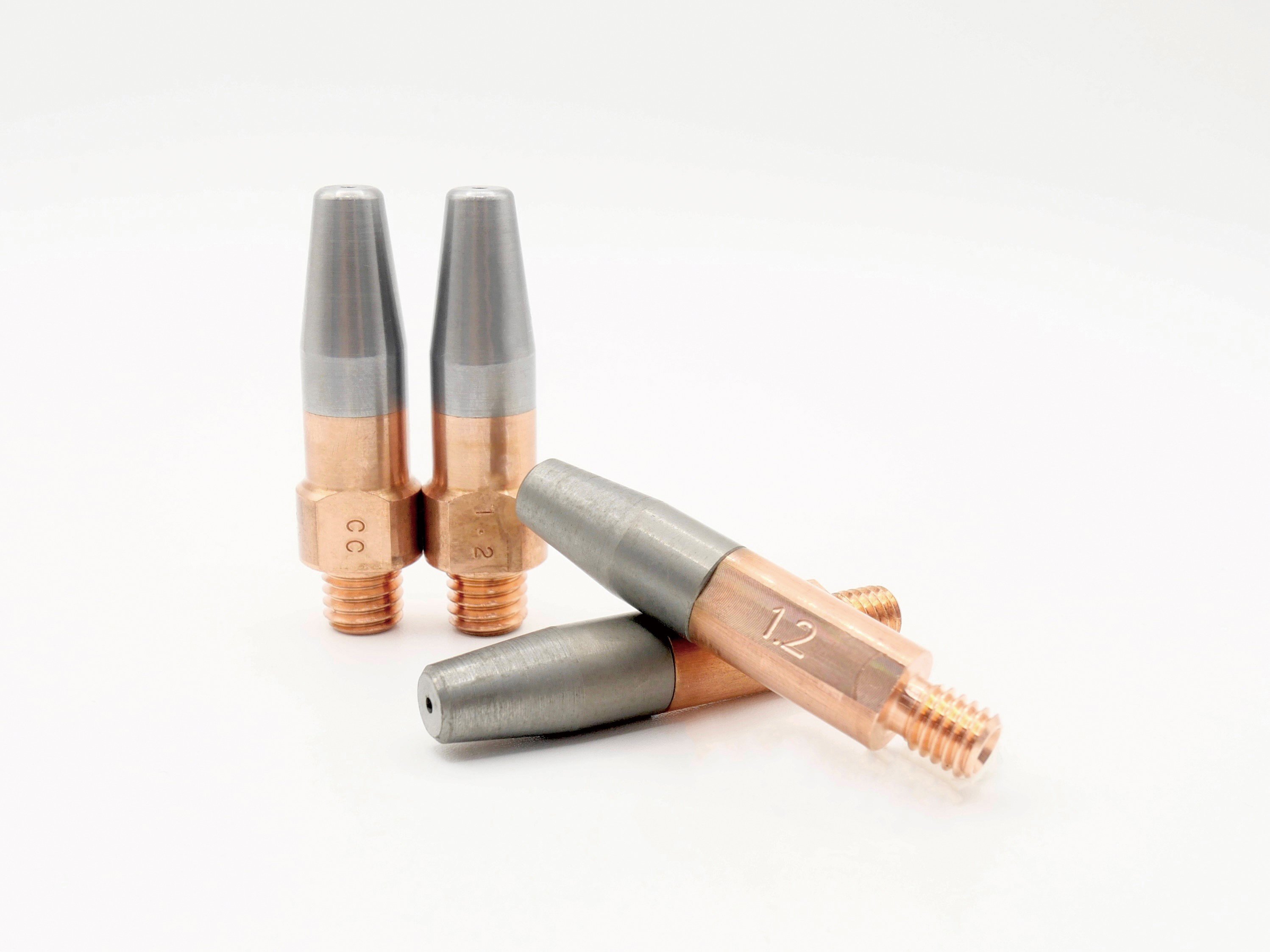
先端に特殊金属を採用したZMコンタクトチップ
上述の通り多くの溶接現場がコンタクトチップを数時間で交換する。チップは溶接中の通電で軟化し、ワイヤの摩擦で内側の穴が真円から楕円に広がるからだ。最終的には溶接の狙いが狂うため、生産性を下げてでも頻繁に交換するのが通例だった。だがZMチップは平均で従来の40倍、使い方次第で96倍の耐久性を持つ。なぜなのか。
「今まで溶接業界に持ち込まれなかった特殊金属を先端に採用した」田中英樹社長は高耐久の理由をそう明かす。通常のコンタクトチップは導電性を重視しクロム銅で作られるが、同社は部品を分割し先端を熱に強く硬い特殊金属、それ以外をクロム銅にした。導電性はクロム銅が特殊金属より勝るが、「加工による構造の工夫」で導電性の問題もクリア。溶接品質は従来通りで桁違いに長寿命な、自動化に適したチップを生み出した。
同条件で溶接後のZMコンタクトチップ(左)と他社製コンタクトチップ(右)の穴径の比較。従来は摩耗で穴形状が楕円に広がってしまう
同製品の発売と前後して自動車業界で低スラグワイヤが急速に普及。低スラグワイヤはチップの摩耗が通常より激しく、2時間どころか1つのワークで交換が必要なため高耐久チップへの置き換えがより急務だ。これを受け、ZMチップの販売本数は初年度の949本から昨年度は1万7401本と3年で約18倍に増えた。国内で専用工場を稼働開始、米国に新工場を設ける構想も進む。
■加工は真似できない
同社はZMチップ以外にナット・ボルト溶接用の下部電極でも廃棄を減らした。通常、下部電極は消耗すれば丸ごと交換するが、電極を3分割して先端のみの交換で済むようにしたのだ。部品を分割した場合、各部品の平面度が高くないと電流がうまく流れない。だが同社は自社で多数の工作機械を揃え、1㍈単位の精度で銅を削り各部品を100%近く内製する。この加工技術がZMチップのような難度の高い部品の開発に活かされている。
「(ZMチップの)先端素材はいつか後追いされるかもしれない。ただ、加工は真似できないでしょう」(田中社長)。今後は切削加工を極めていくと同時に、切削以外の加工法も視野に入れつつより扱いやすい低価格な高耐久コンタクトチップの開発を進める考えだ。
「不思議ですよ。小さなチップひとつで溶接はガラリと変わる。今までもこれからも、他と違う発想で溶接業界に不可欠な存在であり続けます」
田中英樹社長
(日本物流新聞2024年10月25日号掲載)