連載
ファザーマシン2/Chapter28
- 投稿日時
- 2024/07/25 13:08
- 更新日時
- 2024/10/09 16:55
複雑形状ワークの加工コスト削減
皆さん、こんにちは。工業系YouTubeチャンネル、なんとか重工のとんこつです。
今回は、「車ハンドル製作依頼編その2」をお送りします。
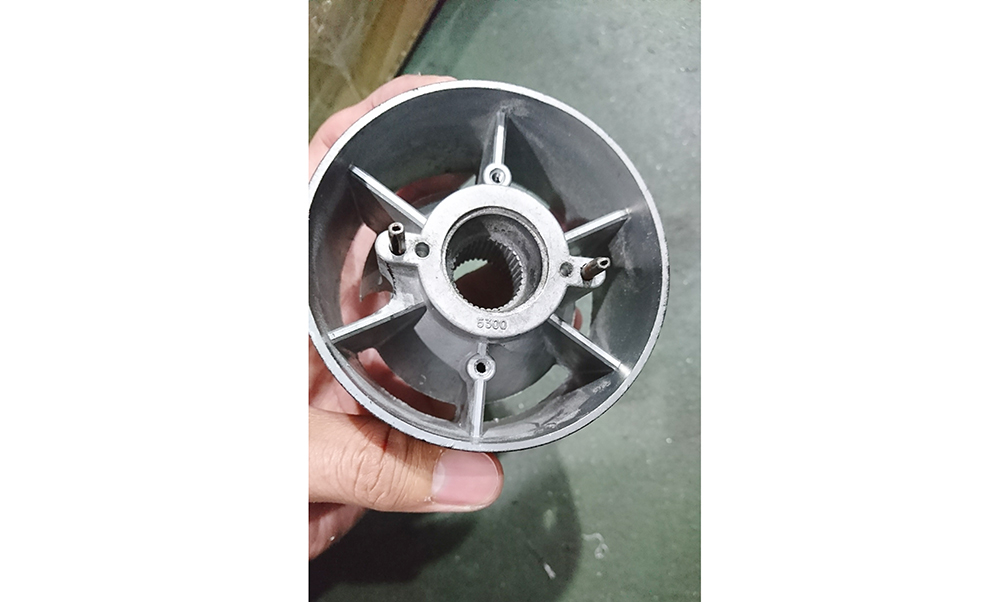
ワイヤ放電で加工したセレーション部分
あれから約1カ月後、ついにハンドルのモデリングにOKをもらったのですが、新たな問題が発生しました。コストが全く合わないのです。
製作費は事前に見積もっていたものの、構造が複雑になり、一体削り出しでは合わなくなってしまいました。そこで、別の提案を行うことにしました。
通常、今回のような削り出しの依頼がある場合、削り出し感を残すことが多いです。ここで言う削り出し感とは、3D形状の部分をモデリング通りの綺麗なサーフェスにするのではなく、 ボールエンドミル等で少し粗めに加工することによりできる凹凸のことを指します。
ボールエンドミルが通るピッチを細かくすればするほどモデル通りの形状に近づきますが、加工時間が莫大に増えます。逆にピッチを粗くすると少し凹凸のある形状になりますが、加工時間は短くなります。この辺りは完全に好みの部分で、バイクパーツなどはあえて粗めに加工されたりします。
そして今回の製作物は、最終的にバフでツルピカに研磨したいそうなので、削り出し感などは残りません。そこで、一体削り出しではなく、溶接構造にしてはどうかと提案してみました。
具体的には、中央のステアリングシャフトと繋がるハブ、持ち手となるリング、ハブとリングを繋ぐスポークをそれぞれ別々のパーツで製作し、あとで溶接する構造です。
溶接箇所は目立つので削り出し依頼の場合は難しいですが、今回は最終的に削って磨き上げるため、無事に採用となりました。製造コストも抑えられ、加工難度もグッと下げられたのでまさにWIN―WINの提案でした。
■現物合わせで加工を依頼
ようやく仕様が決まり製作に入るのですが、新たな問題が発生します。
それは、どこで分割するかということです。どこでも好きに切っていいわけではなく、加工のしやすさや治具の作りやすさ、溶接のしやすさなども考慮する必要があります。この辺りになってくると経験がものを言います。
幸い、私の勤めていた会社は多品種少量生産の会社で、こういったことには慣れていました。また、治具は作ればいいというわけではなく、治具の材料代や加工費、保管にもコストがかかるので、必要ないのであれば作らないに越したことはありません。
もろもろ事前に検証した上で、やっと加工に入れることになりました。しかし、一難去ってまた一難。車のハンドル中央のハブにはセレーションというギアのようなものが切られており、マシニングセンタでは加工できない箇所がありました。
寸法や精度もわからないため、この部分はワイヤ放電加工機を持っている協力工場にステアリングシャフトを送り、現物合わせで加工してもらうことになりました。コストはかかりますが、餅は餅屋です。
依頼者が参加するというカーイベントの締め切りも迫っており、手際よく加工を進めていきます。今回はここまで。次回もお楽しみに!
(2024年7月25日号掲載)
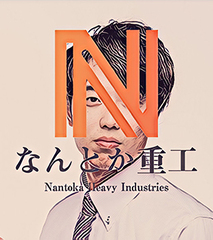
工業系YouTuber【なんとか重工】とんこつ
工業系YouTubeチャンネル【なんとか重工】を、相方のケロと2人で運営。旋盤やフライス、マシニングに溶接機、3Dプリンターなどを活用して自分たちが作りたいモノを作るチャンネル。登録者数は12.5万人(2024年7月25日現在)