インタビュー
日産自動車 パワートレイン・EVコンポーネント生産技術開発本部 技術企画部 戦略企画・技術統括グループ エキスパートリーダー 塩飽 紀之 氏
- 投稿日時
- 2025/03/13 09:00
- 更新日時
- 2025/04/02 15:20
商品・生産技術のゲームチェンジャー
金属3Dプリンターの活用が生産ラインに大きな変革をもたらすのでは、と自動車業界で目されて久しい。しかし、コストや生産性の課題によって、実現は難しいのではといった声も漏れる。そうした逆風を真正面から浴びながら、現実的な解と理想の実現に向けて取り組むのが日産自動車・パワートレイン・EVコンポーネント生産技術開発本部技術企画部戦略企画・技術統括グループエキスパートリーダーの塩飽紀之(しわく・のりゆき)氏だ。金属3Dプリンター活用の課題と期待を聞いた。
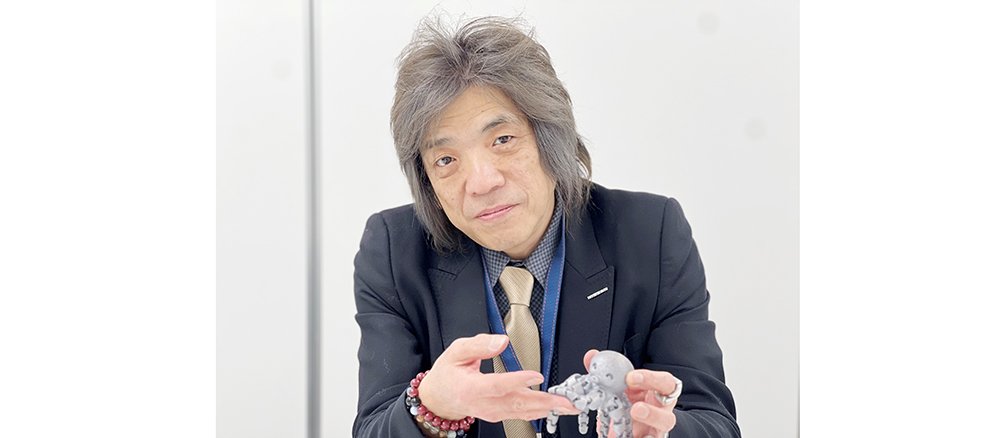
――AM活用を社内外に向けて推進されていますね。
「金属3Dプリンターは歴史が浅く、従来工法と比べると信頼性や生産ラインの考え方が異なり、自動車業界では活用が十分ではありません。しかし、自動車を電動化するにあたり部品の軽量化ニーズはありますし、従来工法では実現しえないデザインや工程集約が可能なため、欧米や中国では活用が進み技術的な差が生まれつつあります。また、ASTMやISOが規格作りに乗り出していて、日本としてそうした枠組みに積極的に入っていかなければ、海外で決められた定義に則ってしか物を作れなくなるという危機感もあります。そこに食い込んでいくためにも、日本国内での活用をより充実させていく必要があると思って取り組んでいます」
――利点もあるのに普及が進まない。障壁はどこにあるのでしょうか。
「生産スピードが遅いため、量産に向かず生産コストが見合わないという見方しかされていない点が一番のハードルだと思います。例えば、現在、自動車の生産ラインで求められるスピードは、鋳造部品で1時間当たり100㍑ぐらいが目安です。一方でAMは一般的なパウダーベッドフュージョン(PBF)方式で100~200CCしか作れない。生産能力に約1000倍の開きがあるわけです。これだけ見るとどうしようもない技術に思えてしまいます。が、鋳造ラインを作るのに10億円の投資が必要だとしたら、1000分の1の100万円で機械を導入できさえすれば、スピードの遅い技術でも機械を並べるだけで投資がイコールになる。このように1部品を作るための投資金額で比較するともう少し違った見え方ができて、十分ペイできる領域も見えてくるのではと考えています」
■エンジン部品としても十分な性能を発揮
――貴社内での活用はいかがでしょうか。
「2016年頃からPBF方式で何ができるか検証し始めました。他社と同様に社内からの反発や懸念は未だに少なくありませんが、今では、Nikon SLM Solutions様のPBF方式と三菱電機様のワイヤーDED方式の2台を活用しています。当社では、AM事業部を独立して立ち上げるのではなく、私を含めた部長級が横浜工場(鶴見、生産技術)とテクニカルセンター(厚木、設計開発)、総合研究所(追浜、基礎研究)の3拠点を兼務して見ているので、比較的現実に則した取り組みができていると思います」
――現状どういった用途で活用している。
「治具用途としては既に現場で使用していますが、量産向けとなるとまだテスト段階です。私の方針として、従来工法の置き換えにAMを使うのは意味がないと考えていますので、AMでしかできないデザインを生かして付加価値を高めていく方向での取り組みを進めています」
――例えば。
「当社には可変圧縮比(VCR)技術を搭載したVC―Turboエンジンという特殊なエンジンがあります。市街地や高速など場面ごとに圧縮比率を変えることで、運転条件が変わっても適切な出力を得ることができる機構です。ピストンとクランクシャフト、ロッドの3点で摺動する一般的なエンジンに、リンク機構を追加することで実現しているため、それぞれの部品をなるべく軽量化したいニーズがありました。従来工法では形状的にも強度的にも難しかったのですが、AMを使うことで機能と信頼性を両立した上で30%の軽量化を実現しました」
「本部品は生産性やコストを度外視して作ったこともあり、実用段階にはないですが、R32GT︱Rのブレーキホースブラケットの取り組みでは、従来3部品を溶接して作っていたものを、機能を維持しながら一体造形し、軽量化も実現しました。また、本部品は外装品なので、従来、融雪剤を撒く地域では板金→溶接→塗装する必要がありましたが、AMならSUS材で造形すれば塗装工程も必要なくなります。生産性は1000分の1ですが、工程集約、材料費低減なども実現でき、もう1、2工夫すればお客様にお届けできる段階にあります」
――AMのさらなる活用に向け一言お願いします。
「一番簡単なのは『何もしない』ことです。従来工法であれば、膨大なバックデータを基にほとんどシミュレーションで物がつくれる状態になっています。ただしそれでは進化しないですし、理想のデザインを工法やデータが作れる形にモディファイしてしまっている可能性もあります。AMなら理想とする形のところに一度立ち戻って、違うアプローチで突破できるのではないかと期待しています」
R32GT-Rのブレーキホースブラケット。右がAMで造形した部品。形は違うがどちらも同じ機能を満たす
バーテンダー≒AM
学生時代はバーテンダーにあこがれた塩飽氏。英国のバーテンダー学校から招待状を受け取るほどだったが、金属材料をブレンドする道を選択した。「マティーニというカクテルがジンとベルガモット、ビターズの3種類のお酒の配合の仕方だけで268種類ものレシピがあるように、金属材料も基本的なエレメントの配合や造形条件を変えることで強度や造形速度が変化する。開発の方向性はポジティブな性質を突き詰めていくこと」
(日本物流新聞2025年3月10日号掲載)